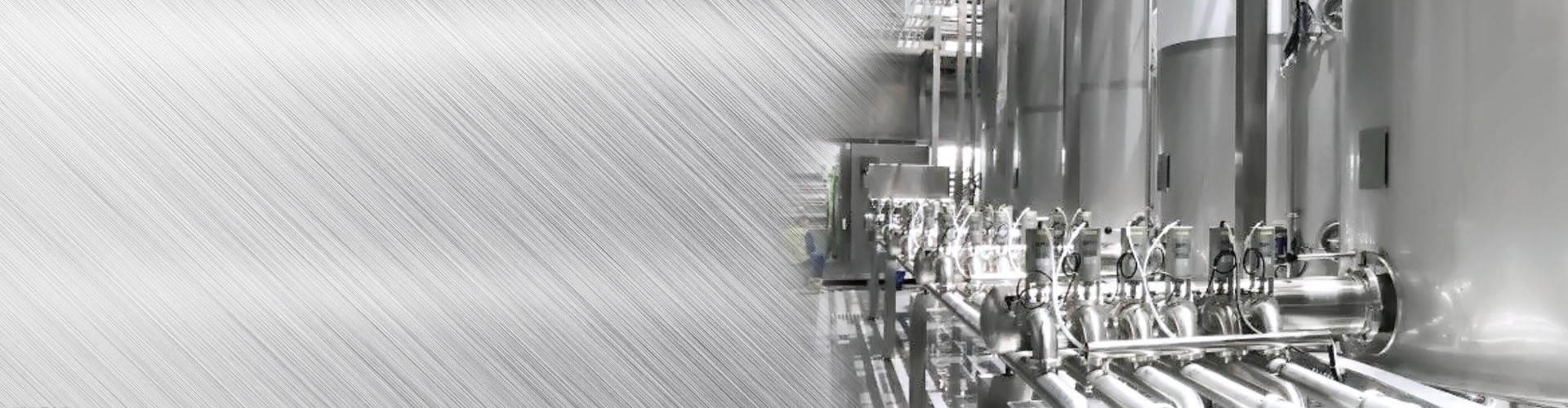
In the pharmaceutical water system, sanitary pressure vessels are widely used, such as demineralized water storage tanks, purified
water storage tanks and water for injection storage tanks, all of which are atmospheric pressure vessels or pressure vessels with
sanitary requirements.
The purpose of designing and building sanitary vessel is to maximize the protection of products, and the product contact surface will not pollute the products and facilitate cleaning, reduce
the breeding corners of chemical or microbial pollution, and facilitate cleaning, maintenance and inspection.
The general requirements of the pharmaceutical industry for sanitary vesseldesign include the following:
The design, selection and installation of the equipment should meet the production requirements, the structure should be simple, and the parts required for cleaning and sterilization should be easy to be disassembled. Equipment that is inconvenient to disassemble and assemble shall be provided with a cleaning port, and a manual cleaning or automatic cleaning device shall be provided;
The surface of the equipment shall be smooth and easily clean, and the inner wall of the equipment directly contacted with material products shall be smooth, flat, easy to clean, corrosion resistance, and avoid dead corners. According to the different requirements of fluid cleanliness level, mechanical polishing or electrochemical polishing shall be adopted respectively to achieve different surface treatment requirements;
The inner surface of the equipment that is in direct contact with the material should be made of materials that do not react with it, not release particles or adsorb materials. Generally, austenitic stainless steel should be used, and glass linedequipment should be avoided as far as possible. Materials that are easy to release particles or adsorb materials, such as rubber lined and fiber reinforced plastic should not be used and should be non-toxic and corrosion-resistant. Sanitary vesselsused for preparation of liquid injections and storage of water for injection shall be made of 316L ultra-low carbon stainless steel;
The transmission parts of the equipment should be well sealed, to prevent the leakage of lubricating oil, coolant and other pollution to raw materials, semi-finished products, finished products and materials. The sealing of the transmission parts is generally not recommended to use packing seal;
For the process requirements for microorganisms, the equipment should not only meet the above requirements, but also meet the requirements of disinfection and sterilization;
Equipment in the clean area, except for special requirements, generally should not be set up with anchor bolts;
The surface of the equipment insulation layer must be flat and smooth, no particulate material falling off. Asbestos cement foam surface shall not be used on the surface. Splicing, flap type insulation shall not be used, It is advisable to use a metal casing for overall protection;
The noise, vibration equipment should be used noise elimination, vibration isolation device, to improve the operating environment. During dynamic testing, the indoor noise level should not exceed 75 decibels;
Pipe connection should be sanitary flange, NA connector, KESTconnector or clamp connector. Sealing material should be PTFE or sanitary rubber seal;
Accessories on the equipment or machinery, such as instruments, measuring devices and liquid level gauge layout should be reasonable. The counting should be accurate. The adjustment and control should be stable and reliable. The material requirements should be the same as the equipment body, and the connection form should meet the requirements of cleaning, disinfection and sterilization;
The design of the equipment should be standardized, generalized, serialized and mechatronics as far as possible.The realization of continuous sealing and automatic detection of the production process is the guarantee for the full implementation of the equipment GMP requirements;
Vessel steel plate should be preferred cold rolled plate, and by solid dissolution and pickling treatment, as far as possible using polishing plate. Manhole, hand hole, sight glass, vessel flange and
pipe flange and other compressed parts must be made of integral stainless steel, not lining, lining ring, composite, pile welding and coating type.
Sanitary vessel is not allowed to use stainless steel lining structure. This is because the stainless steel liner does not guarantee a complete fit with the carbon steel tank. Its gap has residual air. In steam sterilization, the material will be heat expansion, because the stainless steel sheet, carbon steel tank and residual air expansion coefficient is different, which will make the plug welding part fall off, and produce micro cracks, the liquid in the tank through cracks into the stainless steel lining and carbon steel tank will form a "dead corner". The design of the inner wall and internal structure of the sanitary vessel should avoid dead corners, so as to avoid incomplete sterilization caused by the inability of the steam to be effectively or fully achieved during the steam heating sterilization.
There are three types of sanitary-grade sterile connection modes:
The most common connection method in the pharmaceutical water system is the clamp connection, which needs to be filled with a sealing ring at the joint seal and fastened with a clamp. The NA aseptic connection and the KEST aseptic connection are two new types of sanitary connections. The two designs effectively avoid the risk of contamination caused by the dead angle of the pipe interface, especially in the sterility assurance of the installation of the tank side wall accessories, which have been widely promoted and applied in the aseptic pharmaceutical industry.
After talking about the tank itself and connecting the device, let's take a look at the spray device, which is another important tank accessory for sanitary pressure vessels. In the pharmaceutical
water system, the full wetting of the inner surface of the tank helps the system. Self-cleaning and prevention of microbial reproduction can also ensure that the temperature inside the entire tank is uniform. The spray device mainly plays the function of spray cleaning and wetting of the inner surface of the tank.
According to the different working pressures, the spray devices for pharmaceutical water tanks mainly include two categories: fixed cleaning balls and tangential water outlet cleaning balls . In addition, they can also be classified according to different cleaning angles and installation methods.
The fixed cleaning ball is a medium-low pressure, high-flow cleaning ball. The principle is that a small amount of cleaning liquid is continuously sprayed from each small hole of the fixed cleaning ball to the fixed point on the inner wall of the tank, and the cleaning liquid is distributed in a laminar flow manner. To the inner surface of the storage tank, its working pressure is relatively moderate1.5~6bar, and the impact force is relatively weak during cleaning. In order to achieve the cleaning effect, a large amount of cleaning fluid needs to be consumed, and it is mainly used for less demanding cleaning tasks or surface wetting functions.
Due to its non-rotating feature, it has been recognized by some enterprises, but the pressure and flow of the water for injection return water are limited by the design and operation of the pharmaceutical water system, the cleaning effect is general, the cleaning pressure requirements are relatively high, the water consumption and cleaning agent. Due to the large dosage, the cleaning holes are easy to block and red rust and other defects, which have been gradually replaced by tangential water cleaning balls.
The tangential water cleaning ball, also known as the rotating cleaning ball, is a low-pressure, low-flow cleaning ball.It is composed of a water outlet ball and a high-speed rotating connecting rod. The impact force of the water flow on the tangential water outlet ball is used to make the cleaning ball rotate rapidly.Through the combination of vibration mode and physical impact, the cleaning liquid is evenly sprayed on the inner surface of the tank. The working pressure of the tangential water cleaning ball is moderate, and the impact force is relatively strong during cleaning. It only needs less cleaning agent to obtain the ideal effect. It is mainly used for easy-to-clean tanks. Professional rotating cleaning ball wear test shows that under 2.7bar pressure, after 1100 hours of continuous operation, the mass loss of the spray device will be about 90mg. According to the amount of spray cleaning liquid, the theoretical concentration of iron filings is 0.0052 Micrograms/L, far lower than the quality standard of the pharmaceutical industry for the concentration of iron.
The high-speed rotating spray device must avoid the risk of particulate pollution caused by dry running. It is not allowed to use compressed air or other inert gas for purging, otherwise serious red rust and particulate pollution will occur. This is also where the tangential water cleaning ball needs special attention during use.
If you got any question about Sanitary pressure vessel, please contact Beyond service engineer freely.