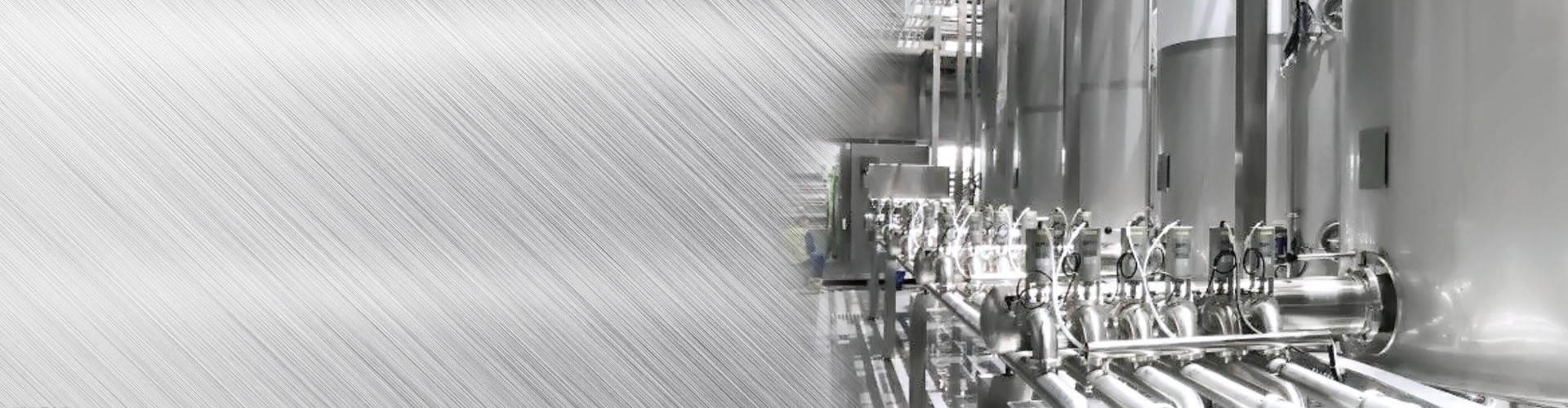
1. Receiving and Sorting Area:•Raw tomatoes are delivered to the plant and unloaded onto conveyors.•A sorting process takes place to remove foreign materials, overripe, underripe, or damaged tomatoes.
2. Cleaning and Washing:•Tomatoes pass through a cleaning stage where they are washed with water to remove dirt, leaves, and other debris.•Some plants may use brushes or air jets for more thorough cleaning.
3. Pre-Processing (Optional):•Depending on the processing method, tomatoes might be blanched to facilitate peeling or passed through a pulper to break down the fruit.
4. Peeling:•After washing, the tomatoes are typically steam-peeled to remove the skin without losing too much pulp.
5. Pulping:•The peeled tomatoes are then processed through a pulper which crushes and separates the juice from the seeds and skins.
6. Sieving:•The resulting mixture is sieved to separate any remaining seeds and larger particles from the tomato pulp.
7. Evaporation:•The tomato juice/pulp enters an evaporator where it is heated under vacuum conditions to reduce its water content. This concentrates the solids (soluble solids content) to achieve the desired Brix level for the final product (e.g., 28-30°Brix for tomato paste).
8. Sterilization/Pasteurization:•The concentrated tomato product is heat-treated to kill any bacteria and extend shelf life. This can be done via indirect heating methods like tubular sterilizers or by direct steam injection.
9. Storage Tanks:•Once sterilized, the concentrate is stored in temperature-controlled tanks before further processing or packaging.
10. Filling and Packaging:•The concentrate is transferred to filling machines that can handle different types of packaging, such as cans, pouches, or drums.•Automatic lines include sealing, labeling, coding, and cartoning systems.
11. Quality Control:•Throughout the process, there are various quality control checkpoints to ensure the product meets standards for color, consistency, pH, Brix, and microbiological safety.
12. Waste Management:•Waste generated during the process, such as tomato skins and seeds, can be managed through drying and composting or utilized for animal feed or biogas production, depending on local regulations and facility capabilities.
Each step must comply with food safety regulations and good manufacturing practices to ensure a high-quality and safe end-product. The efficiency and effectiveness of each component in the tomato concentrate line play a significant role in determining the overall productivity and profitability of the operation.
Here's a comprehensive list of equipment typically found in a tomato concentrate production line:
1. Receiving and Unloading Equipment:•Truck dumpers or forklifts•Conveyors for transporting tomatoes from the unloading area
2. Sorting and Cleaning Equipment:•Grading tables for manual sorting•Optical sorters (optional) for automated sorting•Tomato washing machines with water sprayers, brushes, or air blowers•Water tanks and filtration systems for cleaning water recirculation
3. Peeling Equipment:•Steam peeling machines to remove tomato skins using hot water vapor
4. Pre-Processing Equipment (Optional):•Hot break system: steam kettles for pre-cooking tomatoes before pulping•Cold break system: pulpers that crush tomatoes without prior heating
5. Pulping Machines:•Rotary or hammer mills for crushing tomatoes into pulp and juice•De-stemmers to separate stems from fruits•Seed separators to extract seeds from the pulp
6. Sieving and Filtration Equipment:•Vibrating sieves or rotary screens to filter out seeds and skin remnants•Centrifugal filters to further refine the product
7. Evaporation Systems:•Falling film evaporators or rising film evaporators to reduce water content and increase solids concentration•Vacuum pumps and vacuum receivers for efficient evaporation under low pressure•Condensers to recover and reuse evaporated water
8. Sterilization/Pasteurization Equipment:•Tubular sterilizers or plate heat exchangers for indirect heating•Direct injection pasteurizers for high-temperature short-time (HTST) treatment•Cooling tunnels or chillers to quickly cool down the product after heat treatment
9. Storage Tanks:•Stainless steel holding tanks with agitators for storing concentrated tomato paste/puree at controlled temperatures
10. Filling and Packaging Equipment:•Filling machines for cans, pouches, bottles, or drums•Sealing machines (for cans or pouches)•Labeling machines•Cartoning machines or case packers•Capping machines (for bottles)
11. Quality Control Equipment:•pH meters and refractometers for measuring acidity and Brix levels•Metal detectors and X-ray machines for foreign object detection•Sample preparation equipment for lab analysis
12. Utilities and Support Systems:•Boiler for producing steam•Compressed air systems for operating pneumatic components•CIP (Clean-in-Place) systems for automatic cleaning and sanitation of processing equipment•Waste handling equipment for skins, seeds, and other byproductsEach facility may customize their line based on capacity requirements, available technologies, and desired end-products.
Regular maintenance and calibration of these machines are crucial for ensuring optimal performance and food safety.
The installation and debugging of a tomato concentrate line involve several complex steps to ensure efficient operation, product quality, and compliance with food safety standards. Here's an outline of the process:Installation Process
1. Site Preparation:•Clear the area and create a stable foundation for equipment.•Ensure electrical, water, steam, and compressed air utilities are available and properly installed at each machine's location.•Set up drainage systems for wastewater.
2. Equipment Unloading and Assembly:•Carefully unload all components and machinery according to manufacturer instructions.•Assemble conveyors, sorting machines, peeling units, pulping systems, evaporators, sterilizers, storage tanks, and packaging equipment.
3. Mechanical Integration:•Connect conveyor belts between processing stages.•Install piping and fittings for water, juice flow, and cleaning solutions.•Align and secure all rotating parts, including motors, gears, and pumps.
4. Electrical Connections:•Wire all electrical components such as motors, control panels, PLCs, and sensors.•Ensure power distribution meets safety regulations and is suitable for the equipment load.
5. Automation Setup:•Program PLCs (Programmable Logic Controllers) and SCADA systems to control the production line.•Configure HMI interfaces for operator control and monitoring.
6. Pneumatic and Hydraulic Systems:•Install and connect pneumatic actuators, valves, and cylinders.•Test hydraulic systems where applicable, e.g., in peelers or pressurized cleaning systems.
7. Quality Control Equipment Calibration:•Calibrate pH meters, Brix refractometers, and other testing devices.•Verify that metal detectors, X-ray machines, and other inspection tools are functioning correctly.
8. CIP (Clean-in-Place) System Installation:•Mount spray balls, nozzles, and other cleaning elements within tanks and pipes.•Integrate chemical dosing systems and controls for automated cleaning cycles.
9. Safety Features:•Install emergency stop buttons, safety barriers, and interlocks.•Check fire suppression and ventilation systems.
Debugging and Commissioning
1. Dry Run Testing:•Conduct individual tests on each piece of equipment without any products to verify mechanical and electrical operations.•Check all moving parts, seals, and connections for leaks, wear, and tear.
2. System Integration Testing:•Perform integrated tests to confirm the smooth transition from one process stage to another.•Evaluate automation sequences and interlocking mechanisms.
3. Process Validation:•Conduct test runs using tomatoes to fine-tune parameters such as temperature, pressure, and speed.•Monitor quality indicators like Brix levels, viscosity, color, and taste.
4. Cleaning and Sanitation Verification:•Validate CIP systems by running full cleaning cycles and swabbing surfaces to check cleanliness.•Adjust cleaning protocols if necessary.
5. Performance Optimization:•Optimize throughput rates, energy consumption, and waste reduction.•Address any bottlenecks or inefficiencies identified during testing.
6. Documentation and Training:•Document the entire installation process and all changes made during debugging.•Train operators and maintenance staff on the proper use, cleaning, and troubleshooting of the equipment.
7. Regulatory Compliance:•Ensure all aspects of the installation meet local and international food safety and hygiene standards.•Obtain necessary certifications and approvals before commencing full-scale production.
After thorough installation and rigorous debugging, the tomato concentrate line should be ready for ongoing production. Continuous monitoring, regular maintenance, and periodic performance evaluations will help maintain high-quality output and optimal efficiency.
The tomato concentrate line can benefit from various information technology (IT) applications to improve efficiency, quality control, and overall plant management. Here are some IT solutions commonly implemented in a modern tomato concentrate production facility:
1. Process Automation and Control Systems:•PLCs (Programmable Logic Controllers) for controlling individual machines and processes.•SCADA (Supervisory Control and Data Acquisition) systems for monitoring and controlling the entire production line from a central location.•HMI (Human Machine Interfaces) that allow operators to interact with the equipment and view real-time process data.
2. ERP (Enterprise Resource Planning) Software:•ERP systems manage all business processes, including supply chain management, inventory control, procurement, production planning, and financial reporting.•Integration with the production line allows for accurate forecasting of raw material requirements and efficient scheduling based on demand.
3. MES (Manufacturing Execution System):•MES software provides real-time data about production activities, helping managers make informed decisions to optimize performance and quality.•It captures key metrics such as yield, throughput, and downtime, facilitating continuous improvement initiatives.
4. Quality Management Systems:•LIMS (Laboratory Information Management Systems) to track sample testing, analyze results, and ensure compliance with food safety standards (e.g., pH, Brix, color, and taste).•Real-time quality control using inline sensors and smart devices to monitor parameters like temperature, pressure, and viscosity.
5. Internet of Things (IoT) and Industrial IoT (IIoT):•Sensors and connected devices provide continuous data streams on machine health, product quality, and environmental conditions.•Predictive maintenance algorithms can detect potential equipment failures before they occur, reducing downtime.
6. Artificial Intelligence (AI) and Machine Learning (ML):•AI and ML can be used to analyze large amounts of production data, identifying patterns and trends that help optimize processes and minimize waste.•They can also enhance quality control by improving sorting accuracy or predicting shelf life based on processing conditions.
7. Barcode/RFID Technology:•For tracking materials and finished products throughout the supply chain, ensuring traceability and compliance with regulatory requirements.
8. Cloud Computing and Data Analytics:•Storing and analyzing data in the cloud allows for remote access to critical information and facilitates collaboration among different departments.•Advanced analytics can uncover hidden insights into production efficiency and cost optimization.
9. Mobile Applications and Digital Work Instructions:•Operators can use tablets or smartphones to access work instructions, report issues, or adjust process parameters on the go.
By leveraging these IT solutions, tomato concentrate plants can achieve higher levels of automation, precision, and responsiveness, ultimately contributing to better product quality, increased productivity, and reduced operational costs.
Shanghai Beyond Machinery Co., Ltd
Beyond Machinery specializes in the design and manufacturing of tomato concentrate line. Please contact us now, and our professional technical engineers will customize the equipment plan for tomato concentrate line and provide a quotation. Please contact us now to obtain the latest equipment plan and quotation.