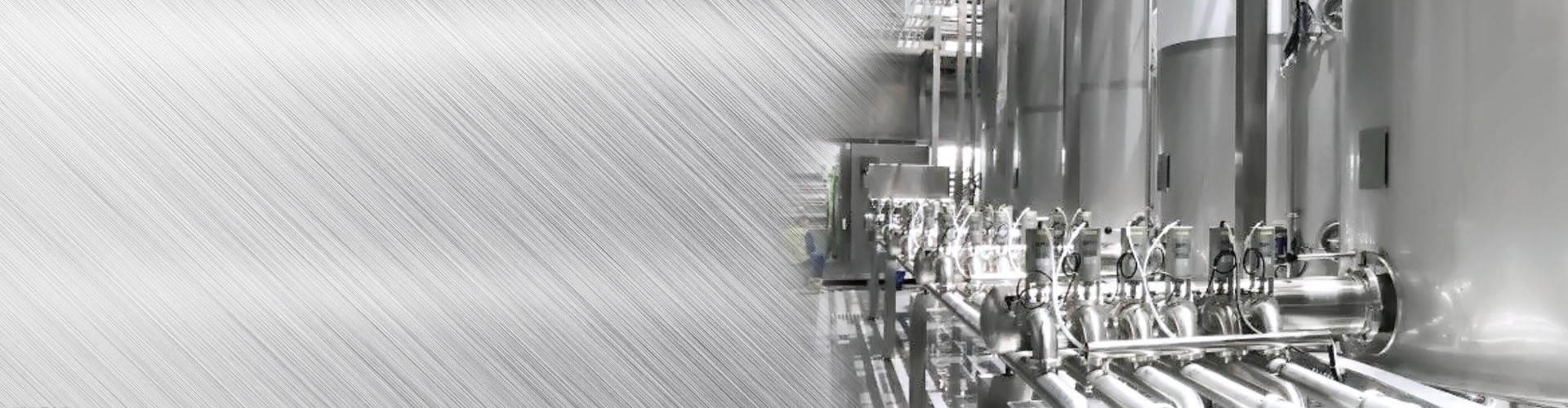
1. Reaction Vessel: Made of high-quality stainless steel, the vessel is typically jacketed for temperature control. It houses the culture medium and provides a sterile environment for cell growth.
2. Agitation System: Consisting of a stirrer and impeller(s), this component helps to mix the contents of the vessel evenly, ensuring that nutrients are distributed throughout and oxygen is supplied to the cells. The agitation speed can be adjusted to minimize shear stress on sensitive cells.
3. Temperature Control: Often featuring a double-walled design with a circulating water or oil jacket, the vessel can be connected to a thermostat-controlled heating/cooling system to maintain the optimal growth temperature for the organisms.
4. Aeration System: A sparger or gas diffuser introduces air or pure oxygen into the culture to provide the necessary dissolved oxygen for aerobic cultures. The gas flow rate can be regulated to control DO levels.
5. PH Control System: Equipped with pH probes and acid/base dosing pumps, the bioreactor allows for real-time monitoring and automatic adjustment of the culture's pH to maintain the ideal condition for cellular metabolism.
6. Level Sensor: To manage the liquid level inside the bioreactor, it might have a sight glass or an electronic level sensor.
7. Sampling Ports: Sterile sampling ports enable researchers to take samples for analysis without compromising the sterility of the system.
8. Automation and Control: The bioreactor comes with a control panel that integrates data acquisition software, allowing users to program and monitor various process parameters such as temperature, pH, agitation speed, and DO levels.
9. Sterilization Capabilities: The bioreactor is designed for easy cleaning and sterilization either manually or via a built-in CIP (Cleaning-in-Place) or SIP (Sterilization-in-Place) system.
10. Accessories: Additional accessories may include probes for measuring biomass, dissolved gases, or metabolites; clamps and seals for securing ports and tubes; and connectors for attaching tubing for nutrient feed, waste removal, and sampling.
This type of small-scale stainless steel bioreactor offers flexibility in experimental design, scalability for pilot studies, and valuable data for scaling up to larger production bioreactors.
Bioreactor parts and their functions
A bioreactor is a device used to accommodate and cultivate microorganisms, cells, tissues, or organs for biochemical reactions under controlled conditions. Its main components and functions are as follows:
1. Reactor body/vessel: • Main function: as the site for biological reactions, storing and mixing biological media (such as culture medium), and providing sufficient space for the growth and reproduction of organisms.
2. Agitation System: • Includes agitator blades, motors, and speed controllers, etc Main function: By stirring, the uniform mixing of biological media inside the reactor is ensured, ensuring consistent distribution of nutrients, oxygen, growth factors, etc., to meet the needs of biological growth.
3. Gas Distribution System: It usually includes an air inlet, bubble diffuser, or microporous aeration head, etc Main function: To deliver necessary gases (such as air or pure oxygen) to the reactor, provide dissolved oxygen required for biological growth, and help eliminate carbon dioxide produced by metabolism.
4. Temperature Control System: • It can include jackets, hot water circulation systems, cooling coils, or built-in heating elements, etc Main function: Precisely control the temperature inside the reactor to adapt to the optimal growth conditions of different organisms.
5. PH Control System: It consists of a pH sensor and an acid-base injection pump Main function: Real time monitoring and automatic adjustment of pH value inside the reactor to maintain a suitable biological reaction environment.
6. Feed System: • Includes feed pumps and pipelines. • Main function: timely addition of nutrients or other essential ingredients during the reaction process to maintain the continuous progress of the biological reaction.
7. Sampling System: Generally equipped with sampling ports and sterile sampling bottles Main function: Regularly obtain internal samples of the reactor for analyzing information such as the number of organisms, product concentration, and nutrient consumption.
8. Online Monitoring System: • Includes sensors for dissolved oxygen measurement, turbidity measurement, biomass monitoring, etc Main function: Real time monitoring of important parameters inside the reactor, providing a basis for process optimization.
9. Cleaning and Sterilization System: • Such as CIP (Cleaning in Place) and SIP (Sterilization in Place) devices. • Main function: Conveniently and quickly clean and sterilize the interior of the reactor, reducing the risk of cross contamination.
The above parts work together to form the core function of the bioreactor, enabling effective control of biological processes in laboratories or industrial production to achieve the production of target products.
The final product of a bioreactor
Bioreactors can produce a wide range of biological products, mainly derived from the growth, metabolism, or expression activities of microorganisms, cells, or biomolecules. The following are some final products that bioreactors may produce:
1. Medical products: • Drug proteins: therapeutic protein drugs such as insulin, interferon, growth hormone, monoclonal antibodies, etc Vaccines: such as viral particle vaccines, recombinant subunit vaccines, etc Disease diagnostic reagents, such as enzyme labeled antibodies in enzyme-linked immunosorbent assay (ELISA).
2. Bioenergy: • Biofuels: Liquid fuels obtained through microbial fermentation, such as ethanol and butanol Biohydrogen: Some microorganisms can produce hydrogen gas under specific conditions.
3. Food additives and nutrients: • Enzyme preparations: Enzymes widely used in food processing and beverage production, such as amylase and lipase Functional food ingredients: such as probiotics, dietary fiber, functional polysaccharides, etc.
4. Chemical raw materials: • Biobased chemicals: such as precursors of bioplastics, biobased lubricants, biosurfactants, etc Fermented products: organic acids and alcohol compounds such as lactic acid, citric acid, acetone butanol, etc.
5. Environmental governance: • Bioremediation agents: Microbial agents used for wastewater treatment or soil remediation Biological desulfurizer: Utilizing microorganisms to remove sulfides from harmful gases.
6. Scientific research applications: Various molecular biology tools such as recombinant proteins and RNA used in basic scientific research.
In summary, bioreactors play a crucial role in the modern biotechnology industry, optimizing biological processes to achieve large-scale production and commercial application of various biological products.
The installation and debugging of a bioreactor is a meticulous and professional task, covering multiple steps and technical points. Below is an overview of the main steps of bioreactor installation and debugging:
Installation phase
1. On site preparation: • Ensure that the installation area is clean, level, dust-free, and complies with biosafety and electrical safety regulations Arrange appropriate support foundations or frames according to the weight and size of the equipment.
2. Equipment positioning: Use appropriate lifting tools and personnel, and correctly handle and place the main body and ancillary equipment of the bioreactor according to the instructions, such as controllers, power equipment, pipelines, and instruments.
3. Pipeline connection: Install inlet and outlet pipelines, circulation pipelines, ventilation pipes, cleaning liquid pipes, sewage pipes, etc., and ensure that all connections are sealed reliably to avoid leakage.
4. Electrical installation: Professional electricians shall complete the installation of power cables, signal cables, control panels and other electrical parts according to the electrical drawings, ensuring good grounding and stable installation of electrical components.
5. Instrument configuration: Install various sensors such as temperature probes, pH electrodes, dissolved oxygen meters, pressure gauges, etc., and calibrate them to normal working conditions.
6. Control system integration: • Integrate the reactor with its supporting automatic control system (such as PLC or DCS), set and debug various control parameters.
Debugging phase
1. Preliminary startup: • Turn on the power, conduct a comprehensive inspection of the control system, confirm that each unit is functioning properly, and execute the preset self-test program.
2. No load operation: Start the stirring system, temperature control system, ventilation system, etc. of the reactor without biological load, conduct no-load debugging, and test the equipment performance and system stability.
3. Simulated operation: • Use simulated solutions instead of actual biological media for trial operation, test the operation status of the equipment under conditions close to actual operating conditions, and adjust and optimize control strategies.
4. Introduction of Bioburden: Based on experimental or production plans, introduce microbial or cellular bioburden and gradually adjust it to process conditions suitable for biological growth and metabolism.
5. Process parameter optimization: Based on the biological reaction process, dynamically adjust parameters such as temperature, pH value, dissolved oxygen, and nutrient supply to achieve ideal product yield and quality.
6. Safety inspection and verification: • Ensure that all safety measures are in place, including over limit alarms and effective emergency stop functions, and conduct verification of CIP (Cleaning in Place) and SIP (Sterilization in Place) systems.
7. Performance evaluation and acceptance: • Test and evaluate various performance indicators of the bioreactor, record debugging results, and conduct formal acceptance after meeting design expectations and user requirements.
During the entire installation and debugging process, strict adherence to operating procedures and safety regulations should be followed. If necessary, manufacturer technical personnel should be invited to provide on-site guidance or cooperate with third-party testing agencies for acceptance. At the same time, a detailed equipment operation and maintenance manual should be established for long-term stable operation and troubleshooting in the future.
Shanghai Beyond Machinery Co., Ltd
Beyond Machinery specializes in the design and manufacturing of stainless steel bioreactor. Please contact us now, and our professional technical engineers will customize the equipment plan for stainless steel bioreactor and provide a quotation. Please contact us now to obtain the latest equipment plan and quotation.