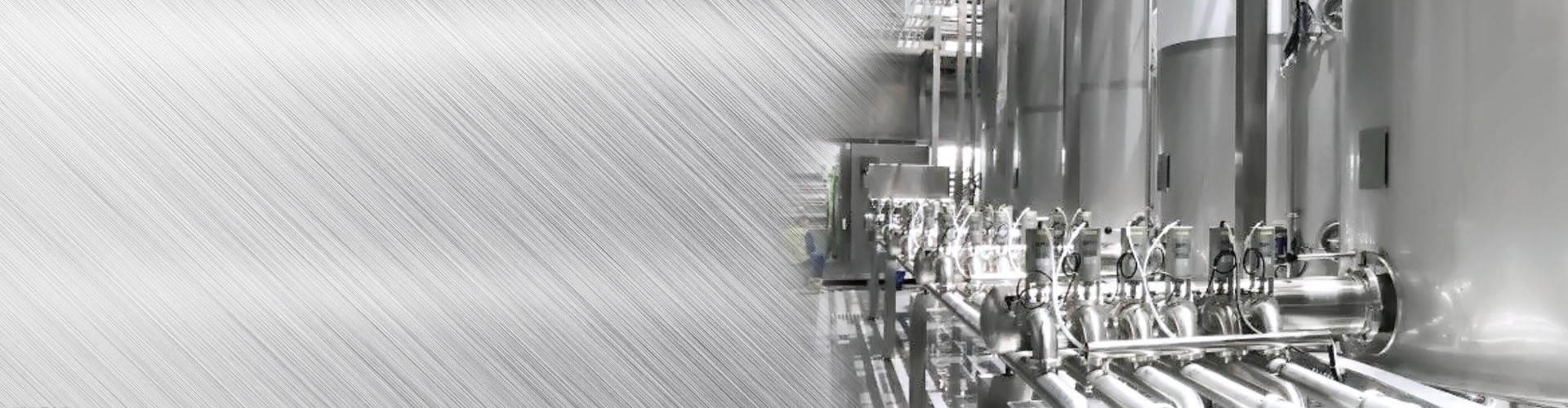
1. Raw material preparation and mixing
•Dry Blender:
•Used to evenly mix dry substances such as skim milk powder, milk powder, sugar, stabilizer, etc.
•Ensure that the ingredients are evenly distributed to avoid agglomeration.
•Liquid Mixing Tank:
•Add water and cream or other liquid ingredients to the mixing tank for preliminary mixing.
•Equipped with a stirrer to ensure that the liquid and dry substances are fully mixed.
2. Preheating and homogenization
•Preheater:
•Preheat the mixed emulsion, usually to 40°C to 50°C.
•Maintain uniform temperature during heating to prevent local overheating.
•Homogenizer:
•Pass the emulsion through a valve with a tiny aperture under high pressure to break the fat globules and evenly disperse them.
•Ensure the product has a delicate taste and extend the shelf life.
3. Pasteurization
•Pasteurizer:
•Pasteurize the reconstituted milk, usually heating it to 72°C to 75°C for 15 to 20 seconds.
•Kill harmful microorganisms and retain nutrients and flavor.
•Plate Heat Exchanger:
•Used for heat exchange during heating and cooling to improve energy efficiency.
•Achieve rapid heating and cooling to ensure product quality.
4. Cooling and Storage
•Cooling System:
•Use a plate heat exchanger or cooling tower to quickly cool the pasteurized emulsion.
•Cool to about 4°C to prevent bacteria from reproducing.
•Cold Storage Tank:
•Store the cooled emulsion in a low-temperature environment to maintain the freshness of the product.
• Check the temperature regularly to ensure that the storage conditions are appropriate.
• Aseptic Filler:
• Fill reconstituted milk into packaging containers such as cartons and plastic bottles under a sterile environment.
• Ensure aseptic operation during the filling process to avoid contamination.
• Sealer:
• Automatically seal the packaging container to ensure a good seal and prevent leakage.
• Mark the production date, shelf life and other information for easy traceability.
6. Quality Control and Testing
• Laboratory Testing Equipment:
• Including microbial detectors, physical and chemical analyzers, etc., for regular sampling and testing of product quality.
• Testing items include microbial indicators, nutrients, heavy metals, etc.
• Automated Control System:
• Use PLC or DCS system to monitor parameters such as temperature, pressure, flow and other parameters during the production process.
• Real-time data acquisition and remote monitoring to ensure that the production process is stable and controllable.
7. Environmental protection and safety
•Wastewater Treatment System:
•Treat wastewater generated during the production process to ensure that the discharge meets the standards.
•Recycle cleaning water to reduce water waste.
•Air Pollution Control Equipment:
•Reduce odor and harmful gas emissions generated during the production process.
•Use clean energy (such as solar energy and natural gas) to reduce carbon emissions.
Customize the process of recombining milk processing equipment according to your needs. The following is the detailed process flow and customized equipment required for the recombining milk processing plant. This process will ensure that the production process is efficient, safe, and meets food safety standards.
1. Project planning and design
• Requirement analysis:
Set daily production targets.
Confirm the product variety (such as whole fat reconstituted milk, low-fat reconstituted milk, flavored reconstituted milk, etc.).
Analyze the market and customer needs.
• Factory location and layout:
Choose a location with convenient transportation, sufficient water sources, and stable power supply.
Reasonable planning of functional areas such as production workshops, warehouses, laboratories, and offices.
• Material selection and procurement:
Select suitable key equipment such as dry mixers, liquid mixing tanks, homogenizers, pasteurizers, etc. based on production capacity.
Purchase auxiliary equipment such as high-quality filters, cooling systems, packaging materials, etc.
2. Preparation and mixing of raw materials
Dry mixer:
Used for uniformly mixing dry matter such as skim milk powder, milk powder, sugar, stabilizers, etc.
Ensure even distribution of ingredients and avoid clumping.
Liquid Mixing Tank:
Add water, cream, or other liquid ingredients to the mixing tank for pre mixing.
Equipped with a mixer to ensure good mixing of liquids and dry matter.
3. Preheating and homogenization
Preheater:
The mixed lotion is preheated, usually to 40 ° C to 50 ° C.
Maintain a uniform temperature during heating to avoid local overheating.
Homogenizer:
• Make the high-pressure lotion pass through the micropore valve, decompose the fat ball and disperse evenly.
Ensure that the product has a delicate taste and extend its shelf life.
4. Pasteurization
• Pasteurization machine:
Recombinant milk is pasteurized, typically heated to 72 ° C to 75 ° C and held for 15 to 20 seconds.
Kill harmful microorganisms and maintain nutrition and flavor.
Plate Heat Exchanger:
Used for heat exchange during heating and cooling processes to improve energy efficiency.
Allow for rapid heating and cooling to ensure product quality.
5. Cooling and storage
Cooling System:
• Use plate heat exchanger or cooling tower to quickly cool lotion after pasteurization.
• Cool to about 4 ° C to prevent bacterial growth.
Cold Storage Tank:
• Store the cooled lotion in a low temperature environment to keep the product fresh.
Regularly check the temperature to ensure suitable storage conditions.
6. Packaging
Aseptic filling machine (aseptic filling machine):
In a sterile environment, pack the reconstituted milk into packaging containers such as paper boxes, plastic bottles, etc.
Ensure sterile operation during the filling process to avoid contamination.
Sealing machine:
Automatically seal packaging containers to ensure good sealing and prevent leakage.
Record the production date, shelf life, and other information for traceability purposes.
7. Quality control and inspection
Laboratory Testing Equipment:
Including microbial detectors, physical and chemical analyzers, etc., used for regular sampling to test product quality.
The detection elements include microbial indicators, nutritional components, heavy metals, etc.
Automatic Control System:
Use PLC or DCS system to monitor temperature, pressure, flow and other parameters during the production process.
Real time data collection and remote monitoring ensure a stable and controllable production process.
8. Environmental protection and safety
Wastewater Treatment System:
Treat the wastewater generated during the production process to ensure that the discharge meets the requirements.
Recycling clean water to reduce water waste.
• Exhaust gas treatment equipment (air pollution control equipment):
Reduce odors and harmful gas emissions generated during the production process.
Reduce carbon emissions by using clean energy sources such as solar energy and natural gas.
9. Project implementation and debugging
Installation and debugging:
After equipment installation, conduct comprehensive debugging to ensure that each link works properly.
Conduct pilot production, adjust parameters, and optimize production processes.
• Staff training:
Train operators to operate and maintain equipment.
Training includes daily maintenance, troubleshooting, safety practices, etc.
10. Continuous improvement and optimization
• Feedback mechanism:
Establish a problem feedback mechanism to promptly collect issues and suggestions related to the production line.
Regularly evaluate production efficiency and product quality, and continuously optimize the process flow.
• Technological upgrade:
Pay attention to the latest technology and industry development trends, and timely introduce new technologies and equipment.
Improve the level of production automation, reduce labor costs, and enhance production efficiency.
Through the customized design of the above process, the restructured dairy processing plant can efficiently and safely produce high-quality products, meet market demand, and ensure consumer health.
Shanghai Beyond Machinery Co., Ltd.
Beyond Machinery specializes in the design and manufacturing of recombined Recombined milk processing equipment.Please contact us now, and ourprofessional technical
engineers will customize the equipment plan for Recombined milk processing plant and provide a quotation.Please contact us now to obtain the latest
equipment plan and quotation.