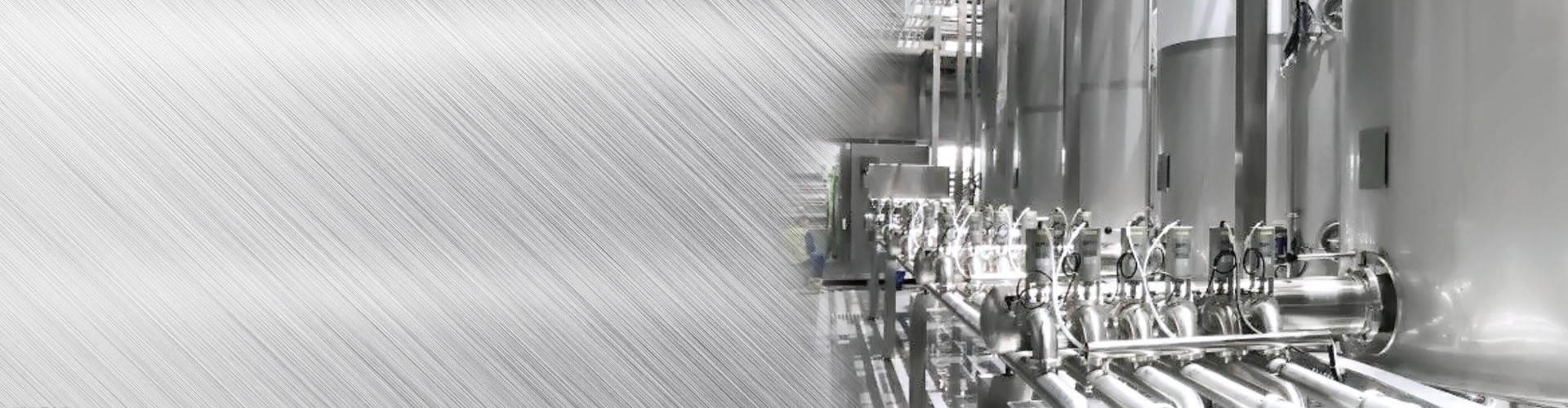
It is expected that the jelly market will continue to expand in the coming years, mainly due to the increasing demand for healthy foods from consumers, as well as the pursuit of novel flavors and innovative products. In addition, the popularity of jelly among consumers of different age groups is also one of the driving factors for market expansion. Consumers are paying more attention to the nutritional value and ingredient list of products, and the demand for natural ingredients and organic certified jelly products is also increasing. The demand for health, innovation, and convenience from consumers will drive market growth and encourage manufacturers to continuously improve product quality and innovation capabilities.
Jelly production line is an automated equipment used for producing jelly products. It usually consists of multiple workstations, each responsible for different production steps. The following is the general workflow of a jelly production line:
1. Raw material preparation: Prepare the required raw materials, such as juice, sugar, gelatin, etc., according to the formula, and conduct necessary testing and screening.
2. Mixing and heating: Mix the raw materials in a certain proportion and heat them in the heating equipment to dissolve and mix evenly.
3. Solidification and molding: Pour the mixed jelly liquid into a mold or container, and solidify it by cooling or other means.
4. Packaging: The formed jelly products can be packaged using automated packaging machinery for packaging, label attachment, etc.
5. Testing and quality control: Conduct quality testing on packaged jelly products, including inspection of appearance, weight, taste, and other aspects, to ensure that the products meet the standards.
6. Finished product storage and distribution: Jelly products that have passed quality inspection will be stored and distributed or sold according to order requirements.
The automation level of the jelly production line can be adjusted according to the production scale and demand, including automated mixing, filling, packaging, quality inspection, and other processes. Through automated production lines, production efficiency can be improved, labor costs can be reduced, and product consistency and quality stability can be ensured.
Jelly production line equipment usually includes the following main parts:
1. Raw material processing equipment: used for processing and purifying raw materials such as fruit juice and puree, including fruit juice extractors, purees, filters, etc.
2. Mixing and seasoning equipment: used for mixing and seasoning raw materials to achieve the desired taste and flavor, including mixing tanks, seasoning tanks, mixers, etc.
3. Saccharification equipment: used to carry out saccharification reactions on mixed raw materials, so that the jelly has a certain viscosity and coagulation, including saccharification tanks, heating equipment, etc.
4. Gel equipment: It is used to gel the saccharified jelly liquid to make it become a solid jelly product, including gel machine, cooling equipment, etc.
5. Molding and packaging equipment: used for molding and packaging of gel jelly, including molding machine, packaging machine, sealing machine, etc.
In addition, auxiliary equipment such as cleaning equipment, disinfection equipment, conveying equipment, and control systems may also be involved to ensure the hygiene, safety, and automation level of the jelly production line. Suitable equipment needs to be selected based on specific production scale and process requirements.
The technical highlights of the jelly processing line are mainly reflected in the following aspects:
1. Automated production: The jelly processing line adopts advanced automation technology, which can achieve a fully automated production process from raw material placement to packaging and packaging. Through the application of automation equipment and control systems, production efficiency and product quality stability have been greatly improved.
2. Accurate ingredient control: The jelly processing line is equipped with an accurate ingredient control system, which can accurately measure various raw materials according to product formula requirements and achieve precise mixing and stirring processes. This can ensure that each batch of jelly products has the same taste and quality.
3. Temperature control technology: The jelly processing line needs to heat and cool the jelly liquid during the production process to achieve solidification and molding. Advanced temperature control technology can ensure that the jelly is processed within the appropriate temperature range, avoiding quality issues caused by improper temperature.
4. Multi functional mold design: The mold design of the jelly processing line is flexible and diverse, and can produce jelly products of various shapes and sizes. By replacing different molds, jelly products with different flavors and demands can be met in the market.
5. Health and safety control: The jelly processing line pays attention to health and safety control in the design and manufacturing process, using food grade materials and equipment that meets hygiene standards. At the same time, the processing line is also equipped with a cleaning and disinfection system to ensure the hygiene of the production environment and the safety of the products.
Overall, the technological highlights of jelly processing lines lie in the application of automated production, precise ingredient control, temperature control technology, multifunctional mold design, and hygiene and safety control, making jelly production more efficient, stable, and safe.
The process flow of a jelly processing line usually includes the following main steps:
1. Raw material preparation: Choose fresh fruits or juice as the main raw material. Wash, peel, and seed the fruits, then extract juice or cut them into small pieces for later use.
2. Mixing of ingredients: According to the formula requirements of the jelly product, mix the juice, sugar, acidity regulator, thickener and other ingredients together in a certain proportion. Food coloring, essence and other condiments can be added as required.
3. Heating and dissolving: Pour the mixed ingredients into a heating container, and dissolve the sugar and other ingredients in the juice by heating. The heating temperature and time vary depending on different jelly products.
4. Thickening and coagulation: Add a thickener (such as gelatin) to the heated juice and stir thoroughly to make the juice viscous. Then pour the juice into the mold and let it solidify for a period of time.
5. Cooling and packaging: After the jelly has completely solidified, place the mold in a cooling chamber or cooling equipment for cooling to make the jelly stronger. Finally, remove the jelly from the mold and package and seal it.
It should be noted that the specific jelly processing line process may vary due to factors such as production scale, product types, and process requirements. The above is only a general introduction to the process, and adjustments and improvements need to be made according to specific situations in actual operation.
The final product of the jelly processing line is jelly products of various flavors and shapes. These jelly products are usually made from fruit juice, sugar, gelatin, and other ingredients, and processed through a series of production processes such as heating, solidification, and molding. The final product can be various flavors of jelly blocks, jelly strips, jelly balls, jelly sugars, etc. The specific product form and taste depend on the design of the processing line and customer needs.
The operation and maintenance of the jelly processing line are key to ensuring the smooth operation of the production process and the normal operation of the equipment. The following are the general steps for operating and maintaining a jelly processing line:
1. Operation:
-Preparation work: Operators need to be familiar with the working principle of the jelly processing line and the functions of each equipment to ensure that the equipment and work area are clean and hygienic.
-Raw material preparation: Prepare the required raw materials according to the production plan, and conduct necessary inspections and quality control.
-Equipment settings: Adjust equipment parameters and workflow according to product requirements to ensure that the equipment can operate normally.
-Production operation: According to the process flow, input the raw materials into the equipment for processing, and pay attention to controlling key parameters such as time, temperature, and pressure.
-Monitoring and adjustment: Real time monitoring of various indicators during the production process, such as temperature, flow rate, pressure, etc., and timely adjustment of equipment parameters to maintain a stable production state.
-Fault handling: In case of equipment malfunction or abnormal situation, stop the machine in a timely manner and take corresponding maintenance or handling measures.
2. Maintenance:
-Daily maintenance: Regularly clean, lubricate, and inspect the jelly processing line to ensure smooth and safe operation of the equipment.
-Preventive maintenance: According to the maintenance manual provided by the equipment manufacturer, carry out regular maintenance and repair work, such as replacing vulnerable parts, calibrating sensors, etc.
-Troubleshooting: For equipment malfunctions, careful investigation and analysis are required to identify the cause of the problem and take corresponding repair measures.
-Training and updates: Regularly train operators and maintenance personnel to understand the latest operating techniques and maintenance methods, improve work efficiency and equipment reliability.
The operation and maintenance of jelly processing lines require professional knowledge and skills to ensure the quality and efficiency of the production process. Meanwhile, reasonable operation and maintenance can also extend the service life of equipment, reduce failure rates, and improve production efficiency.
The information technology of jelly processing line refers to the application of modern information technology to various links of jelly production and processing line to improve production efficiency, quality control, and management level. The following are common information technologies used in jelly processing lines:
1. Automation control system: Through sensors, actuators, and controllers, the automation control and monitoring of the jelly processing line are achieved. It can monitor production parameters in real-time, such as temperature, pressure, flow rate, etc., and automatically adjust according to set rules to improve production efficiency and stability.
2. Production Planning and Scheduling System: Using computer software to optimize and schedule the production plan of the jelly processing line, reasonably arrange production tasks and resources, and improve production efficiency and resource utilization.
3. Process data collection and analysis system: Real time production data of various stages of the jelly processing line, such as temperature, humidity, pH value, etc., are collected through sensors and data acquisition equipment. Then use data analysis software to process and analyze the data, identify potential problems and make timely adjustments to improve product quality and production efficiency.
4. Quality traceability system: Through barcode, RFID and other technologies, each production batch on the jelly processing line is uniquely identified and recorded, achieving product quality traceability. It can track the source of raw materials, production process parameters, production personnel, and other information to improve product quality management and risk control capabilities.
5. Energy management system: By monitoring and analyzing the energy consumption of the jelly processing line, optimizing energy usage plans, reducing energy waste, and lowering production costs.
6. Remote monitoring and maintenance system: Utilize network and remote monitoring technology to achieve remote monitoring and fault diagnosis of jelly processing lines. It can detect problems in a timely manner and perform remote maintenance, reduce downtime, improve equipment reliability and maintenance efficiency.
In summary, the information technology of jelly processing lines can improve production efficiency, quality control, and management level, bringing higher competitiveness and economic benefits to jelly production enterprises.
The preparation for the investment of the jelly processing line needs to consider the following aspects:
1. Market research: Before investing, it is necessary to conduct market research to understand the demand and competition in the jelly market, and determine product and market positioning.
2. Technical preparation: The jelly processing line needs to have corresponding production technology and process flow. This includes the selection of raw materials for jelly, formulation research and development, selection and debugging of production equipment, etc. Consider collaborating with professional food engineers to ensure the scientific and stable production process.
3. Equipment procurement: Select suitable jelly processing line equipment based on production scale and product types. This includes jelly production equipment, packaging equipment, quality inspection equipment, etc. Consider factors such as the quality, performance, production capacity, and after-sales service of the equipment.
4. Raw material supply: Ensure stable raw material supply channels, select high-quality raw materials such as fruit juice, pectin, sugar, etc., and establish long-term cooperative relationships with suppliers to ensure product quality and stability.
5. Personnel training: In order to ensure the normal operation of the production line and product quality, it is necessary to train operators to master relevant operational skills and quality control knowledge.
6. Production planning and management: Establish a scientific production planning and management system, including raw material procurement, production scheduling, inventory management, quality control, etc., to ensure the stability of production efficiency and product quality.
7. Safety and hygiene: The jelly processing line needs to comply with relevant food safety and hygiene standards to ensure the safety and hygiene quality of the products. Establish a sound production environment and operating standards, and conduct regular cleaning and disinfection.
The above are the general steps and considerations for the preparation of the jelly processing line, and the specific situation needs to be analyzed and planned according to the actual situation of the enterprise.
Shanghai Beyond Machinery Co., Ltd
Beyond Machinery specializes in the design and manufacturing of Jelly production line. Please contact us now, and our professional technical engineers will customize the equipment plan for Jelly production line and provide a quotation. Please contact us now to obtain the latest equipment plan and quotation.