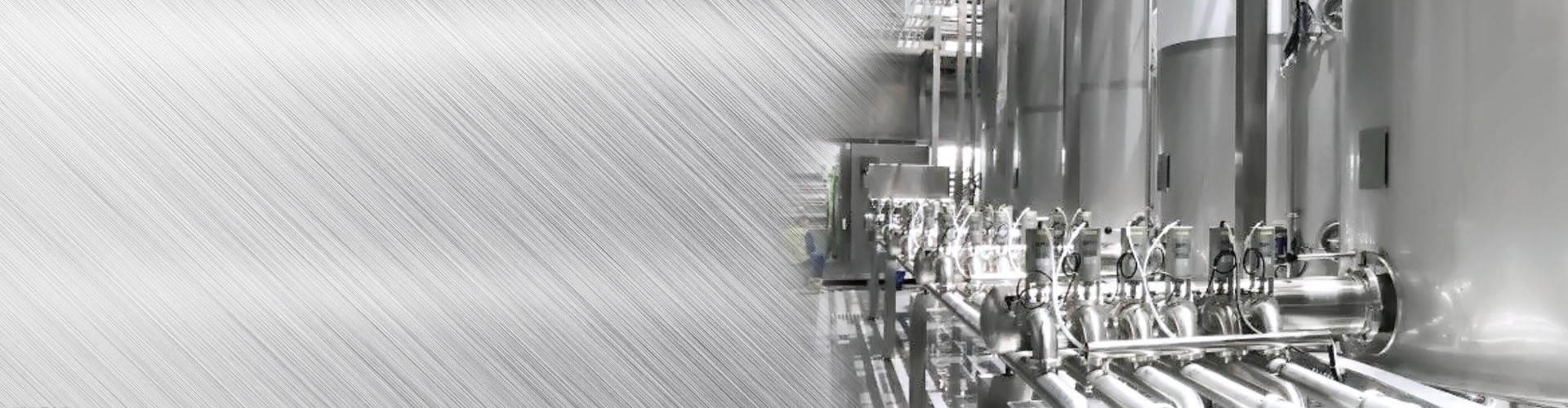
Case 1: A globally leading tomato product manufacturer - a seasoning group
Background:
• Company name: Seasoning Group
• Product type: Various tomato products, including tomato sauce, tomato sauce, tomato puree, etc
• Production scale: Leading globally with multiple large processing plants
Main equipment:
• Raw material receiving and cleaning: Fully automatic cleaning line equipped with conveyor belt and high-pressure spray system to ensure thorough cleaning of tomatoes.
• Crushing and pretreatment: Large crushers can quickly crush tomatoes into pulp while removing impurities.
Boiling and Concentrating: A multifunctional continuous boiling pot equipped with a steam heating system for efficient concentration.
Seasoning and mixing: A large mixing tank used to add various seasonings and mix them evenly.
• Filtration: An efficient centrifugal filter machine is used to remove the skin and seeds, ensuring the delicacy of tomato sauce.
• Filling and sealing: The fully automatic filling and sealing machine can quickly and accurately fill tomato sauce into bottles and seal them.
Sterilization: High temperature instantaneous sterilization equipment (UHT) ensures product safety and shelf life.
• Cooling: The rapid cooling system quickly cools the sterilized tomato sauce to room temperature.
• Packaging: Fully automatic packaging line, including labeling machines, packing machines, etc., to achieve complete packaging of finished products.
• Refrigeration and Storage: Large refrigerated warehouses ensure the freshness of products during storage and transportation.
technological process:
1. Raw material receiving and cleaning: Tomatoes enter the fully automatic cleaning line through a conveyor belt and are thoroughly cleaned by a high-pressure spray system.
2. Crushing and pretreatment: The cleaned tomatoes enter a large crusher and are crushed into a slurry.
3. Boiling and Concentrating: Tomato paste enters a multifunctional continuous boiling pot and is boiled and concentrated to the desired concentration through a steam heating system.
4. Seasoning and mixing: The concentrated tomato paste is poured into a large mixing tank, and various seasonings are added and evenly mixed.
5. Filtration: The mixed tomato sauce is filtered through an efficient centrifugal filter to remove the skin and seeds, resulting in a delicate tomato sauce.
6. Filling and sealing: Tomato sauce is filled into bottles and sealed using a fully automatic filling and sealing machine.
7. Sterilization: The sealed bottle enters the high-temperature instantaneous sterilization equipment (UHT) for sterilization treatment.
8. Cooling: The sterilized bottle is rapidly cooled to room temperature through a rapid cooling system.
9. Packaging: After cooling, the bottles enter the fully automatic packaging line and complete the packaging steps such as labeling and packing.
10. Refrigeration and Storage: Packaged finished products are stored in large refrigerated warehouses to ensure their freshness and shelf life.
Background:
• Company name: A large food company
• Product type: Various tomato products, including tomato sauce, tomato puree, tomato juice, etc
• Production scale: Regional large-scale processing plants
Main equipment:
Raw material receiving and cleaning: Fully automatic cleaning line equipped with conveyor belt and high-pressure spray system.
• Crushing and pretreatment: Large crushers can quickly crush tomatoes and remove impurities.
Boiling and Concentrating: A multifunctional continuous boiling pot equipped with a steam heating system.
Seasoning and mixing: A large mixing tank used to add various seasonings and mix them evenly.
• Filtration: Efficient centrifugal filter to remove fruit peels and seeds.
• Filling and sealing: Fully automatic filling and sealing machine, capable of high-speed and precise filling and sealing.
Sterilization: High temperature instantaneous sterilization equipment (UHT) ensures product safety and shelf life.
• Cooling: The rapid cooling system quickly cools the sterilized tomato sauce to room temperature.
• Packaging: Fully automatic packaging line, including labeling machines, packing machines, etc.
• Refrigeration and Storage: Large refrigerated warehouses ensure the freshness and shelf life of products.
technological process:
1. Raw material receiving and cleaning: Tomatoes enter the fully automatic cleaning line through a conveyor belt and are thoroughly cleaned by a high-pressure spray system.
2. Crushing and pretreatment: The cleaned tomatoes enter a large crusher and are crushed into a slurry.
3. Boiling and Concentrating: Tomato paste enters a multifunctional continuous boiling pot and is boiled and concentrated to the desired concentration through a steam heating system.
4. Seasoning and mixing: The concentrated tomato paste is poured into a large mixing tank, and various seasonings are added and evenly mixed.
5. Filtration: The mixed tomato sauce is filtered through an efficient centrifugal filter to remove the skin and seeds, resulting in a delicate tomato sauce.
6. Filling and sealing: Tomato sauce is filled into bottles and sealed using a fully automatic filling and sealing machine.
7. Sterilization: The sealed bottle enters the high-temperature instantaneous sterilization equipment (UHT) for sterilization treatment.
8. Cooling: The sterilized bottle is rapidly cooled to room temperature through a rapid cooling system.
9. Packaging: After cooling, the bottles enter the fully automatic packaging line and complete the packaging steps such as labeling and packing.
10. Refrigeration and Storage: Packaged finished products are stored in large refrigerated warehouses to ensure their freshness and shelf life.
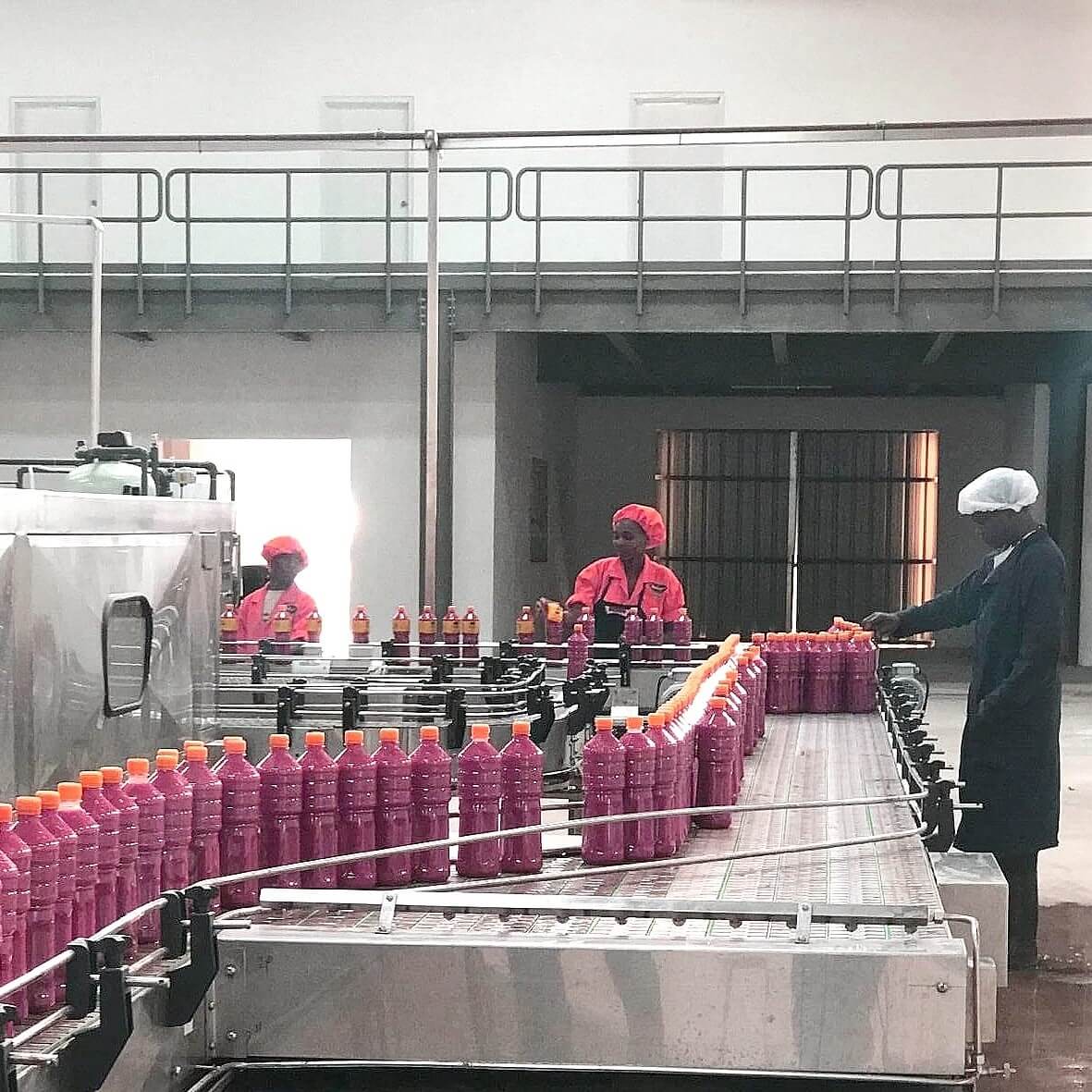
Case 3: A Modern Tomato Products Processing Factory - A Food Factory
Background:• Company name: A certain food factory
• Product type: Various tomato products, including tomato sauce, tomato puree, tomato soup, etc
• Production scale: modern large-scale processing plants
Main equipment:
Raw material receiving and cleaning: Fully automatic cleaning line equipped with conveyor belt and high-pressure spray system.
• Crushing and pretreatment: Large crushers can quickly crush tomatoes and remove impurities.
Boiling and Concentrating: A multifunctional continuous boiling pot equipped with a steam heating system.
Seasoning and mixing: A large mixing tank used to add various seasonings and mix them evenly.
• Filtration: Efficient centrifugal filter to remove fruit peels and seeds.
• Filling and sealing: Fully automatic filling and sealing machine, capable of high-speed and precise filling and sealing.
Sterilization: High temperature instantaneous sterilization equipment (UHT) ensures product safety and shelf life.
• Cooling: The rapid cooling system quickly cools the sterilized tomato sauce to room temperature.
• Packaging: Fully automatic packaging line, including labeling machines, packing machines, etc.
• Refrigeration and Storage: Large refrigerated warehouses ensure the freshness and shelf life of products.
technological process:
1. Raw material receiving and cleaning: Tomatoes enter the fully automatic cleaning line through a conveyor belt and are thoroughly cleaned by a high-pressure spray system.
2. Crushing and pretreatment: The cleaned tomatoes enter a large crusher and are crushed into a slurry.
3. Boiling and Concentrating: Tomato paste enters a multifunctional continuous boiling pot and is boiled and concentrated to the desired concentration through a steam heating system.
4. Seasoning and mixing: The concentrated tomato paste is poured into a large mixing tank, and various seasonings are added and evenly mixed.
5. Filtration: The mixed tomato sauce is filtered through an efficient centrifugal filter to remove the skin and seeds, resulting in a delicate tomato sauce.
6. Filling and sealing: Tomato sauce is filled into bottles and sealed using a fully automatic filling and sealing machine.
7. Sterilization: The sealed bottle enters the high-temperature instantaneous sterilization equipment (UHT) for sterilization treatment.
8. Cooling: The sterilized bottle is rapidly cooled to room temperature through a rapid cooling system.
9. Packaging: After cooling, the bottles enter the fully automatic packaging line and complete the packaging steps such as labeling and packing.
10. Refrigeration and Storage: Packaged finished products are stored in large refrigerated warehouses to ensure their freshness and shelf life.
Success factors
Technological innovation: Adopting advanced production equipment and technology to improve production efficiency and product quality.
Quality control: Strict production process management and quality testing ensure that products meet international standards.
Market expansion: Expand the market through various channels, including supermarkets, catering industry, food processing plants, etc.
Supply chain management: Optimize supply chain management to ensure stable supply of raw materials and cost control.
These cases demonstrate typical applications of large-scale industrial tomato sauce processing factories, and we hope this information is helpful to you.
Shanghai Beyond Machinery Co., Ltd.
Beyond Machinery specializes in the design and manufacturing of tomato paste processing plant.Please contact us now, and ourprofessional technical engineers will customize the equipment plan for tomato paste processing plant and provide a quotation.Please contact us now to obtain the latest equipment plan and quotation.