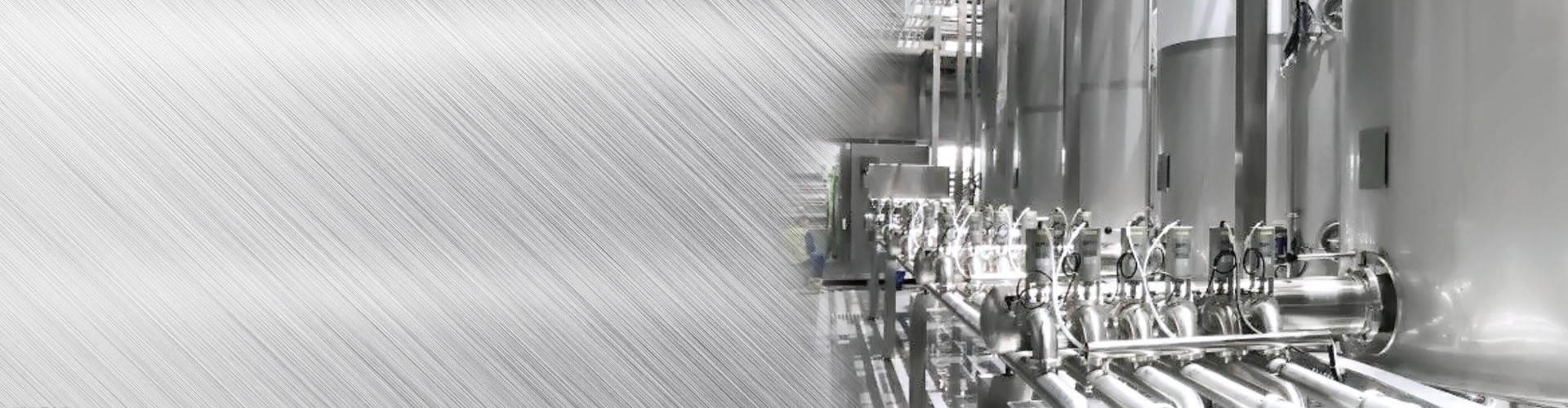
1. Receiving and Sorting• Reception: Tomatoes are delivered to the plant and offloaded into designated areas, where they are inspected for quality and sorted based on ripeness and size.• Sorting: Advanced sorting machinery uses cameras and sensors to automatically separate good tomatoes from those with defects, ensuring only high-quality tomatoes proceed to further processing.
2. Washing and Cleaning• Washing: Tomatoes pass through a series of washing systems, typically involving water sprays and brushes, to remove dirt, pesticides, and other contaminants.• Sanitizing: After washing, tomatoes may be treated with a mild sanitizing solution to eliminate surface microorganisms.
3. Crushing and Pulping• Crushing: The washed tomatoes are crushed to break them down into a pulp. Crushers or mills gently rupture the fruit, separating the flesh from the skin and seeds.• Dejuicing: The crushed pulp is pressed or screened to extract the juice, which is then sent to the next stage.
4. Heating and Evaporation• Preheating: Tomato juice is preheated to inactivate enzymes and improve the flavor profile.• Concentration: Using evaporators, the juice is heated under vacuum to remove excess water, concentrating it into paste. Falling film or rising film evaporators are common technologies employed.
5. Pasteurization• Sterilization: The concentrated paste undergoes high-temperature short-time (HTST) pasteurization or ultra-high temperature (UHT) treatment to destroy pathogens and increase shelf life.
6. Cooling and Packaging• Cooling: The hot paste is rapidly cooled to prevent spoilage and maintain quality.• Packaging: Once cooled, the paste is packed into various containers (cans, pouches, drums, etc.) using automated filling and sealing machines. Aseptic packaging is often used to ensure sterility.
7. Quality Control and Laboratory Testing• Testing: Throughout the process, samples are taken for quality checks, including pH, Brix (soluble solids content), color, and microbiological testing.• Final Inspection: Finished products are visually inspected before being dispatched.
8. Waste Management• Byproduct Utilization: Seeds, skins, and other residue can be processed into secondary products like animal feed or compost.
9. Maintenance and Sanitation• Regular cleaning and sanitation of equipment and facilities are critical to maintaining food safety standards.
10. Automation and Control Systems• Modern plants incorporate advanced automation and control systems, including PLCs and SCADA, to manage the entire process, ensuring consistency, efficiency, and traceability.
Setting up a tomato paste processing plant requires careful planning, adherence to food safety regulations, and investment in appropriate machinery and infrastructure. It's also essential to consider environmental sustainability practices, such as efficient water usage and waste management systems.
Tomato paste processing machine installation and debugging
Installing and debugging a tomato paste processing machine involves several steps to ensure that the equipment operates safely and efficiently.
Here’s a general guide on how this process might unfold:Installation Process
Site Preparation:• Ensure the facility meets the requirements for installing the machinery, including electrical supply, water supply, drainage, and space.• Prepare the foundation or mounting area as per the manufacturer's specifications to support the weight and stability of the machines.• Delivery and Unpacking:• Receive the machinery at the site and carefully unpack it, checking for any damages during transit.• Verify all components against the delivery list.• Assembly:• Assemble the machinery following the manufacturer’s instructions or with the assistance of their technical team if required.• Connect all the components, such as conveyor belts, processing units, and packaging machines, ensuring they are aligned properly.• Piping and Electrical Connections:• Install necessary piping for water, steam, and other utilities.• Connect electrical wiring, ensuring compliance with local safety codes.
Hygiene and Safety Setup:• Install any required safety devices and hygiene controls, such as emergency stop buttons and sanitization stations.• Documentation:• Keep detailed records of the installation, including serial numbers, installation dates, and any modifications made.Debugging Process1. Initial Checks:• Perform a visual inspection to ensure everything is assembled correctly and there are no obvious issues.• Check all connections for leaks or loose fittings.
Electrical Testing:• Test the electrical systems to confirm that all components receive power and function as intended.• Pneumatic and Hydraulic Testing:• If applicable, test pneumatic and hydraulic systems for leaks and proper operation.• Run Tests:• Conduct initial run tests using a small batch of tomatoes to check the performance of each component.• Observe the operation of the machine to ensure it runs smoothly and efficiently.• Calibration:• Adjust settings such as temperature, pressure, and speed based on the test results.• Calibrate sensors and control systems to optimize performance.• Process Optimization:• Work with the manufacturer’s technicians to fine-tune the process parameters for maximum efficiency and product quality.• Safety and Quality Assurance:• Confirm that all safety protocols are functioning and that the quality of the tomato paste meets standards.• Train staff on safety procedures and operation guidelines.• Documentation:• Record the results of the debugging process, including any adjustments made and their effects on the machine’s performance.
Final Inspection:• Have a final inspection conducted by an engineer or technician to ensure all systems are ready for full-scale production.• Training:• Provide training sessions for the operational team to ensure they understand how to operate and maintain the machine properly.• Maintenance Plan:• Develop a maintenance schedule to keep the machine running optimally and prevent breakdowns.
Shanghai Beyond Machinery Co., Ltd.
Beyond Machinery specializes in the design and manufacturing of tomato paste processing plant.Please contact us now, and our professional technical engineers will customize the equipment plan for tomato paste processing plant and provide a quotation. Please contact us now to obtain the latest equipment plan and quotation.