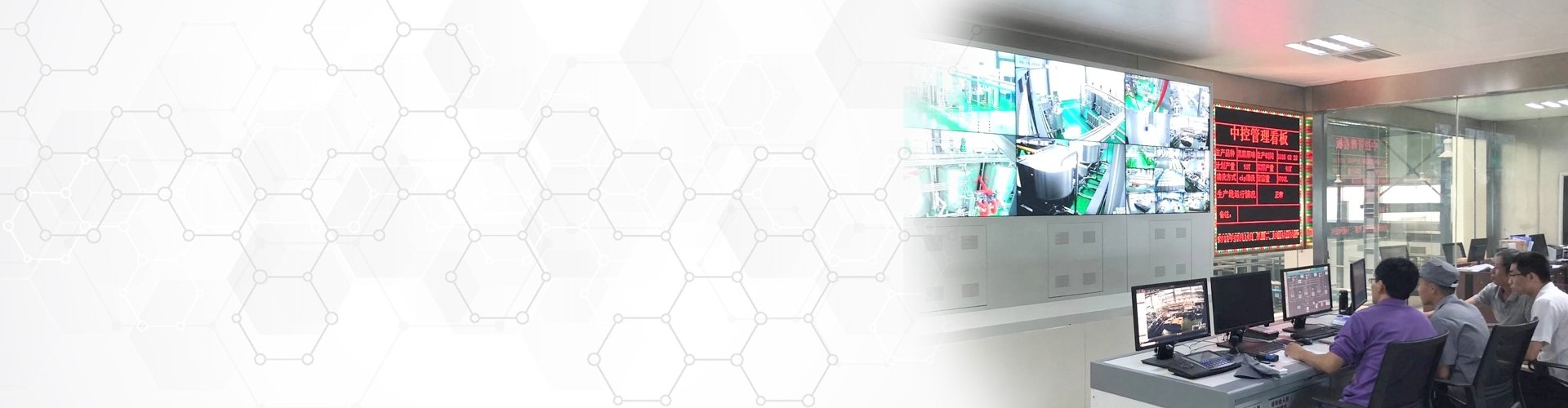
Continuously spraying type pasteurization and cooling tunnels are used in the food and beverage industry to effectively pasteurize and cool products. These tunnels are designed to provide consistent and efficient heat treatment to ensure product safety and quality.
The process begins with the product being transported through a conveyor belt system into the tunnel. As the product moves through the tunnel, it is continuously sprayed with hot water or steam to achieve the desired pasteurization temperature. The spraying system ensures even distribution of heat throughout the product, eliminating any potential bacterial contamination.
After reaching the required pasteurization temperature, the product is then cooled down using a similar spraying system with cold water. This rapid cooling process helps to preserve the quality and freshness of the product while preventing any bacterial growth.
The continuously spraying type pasteurization and cooling tunnel offers several advantages. Firstly, it provides a continuous and automated process, allowing for high production rates and efficiency. The even and thorough heat treatment ensures that all areas of the product are properly pasteurized, reducing the risk of pathogens and extending shelf life.
Additionally, these tunnels can be customized to suit different product types and sizes, making them versatile for various applications. They also feature precise temperature control and monitoring systems, ensuring the product's integrity and consistency.
In conclusion, continuously spraying type pasteurization and cooling tunnels are an essential component in the food and beverage industry. They provide an effective and efficient method for pasteurizing and cooling products, ensuring their safety and quality while maintaining high production rates.
Application
Spraying Sterilizing & Cooling Tunnel is designed specially for milk, juice, drink, beer, food and drug after packaging, which can help to postpone the storage period by sterilizing and cooling. It is recommended as a second pasteurization in the piplining. It can be prepared in different process even with high auto-controlling according to the specific request from customer like heating, sterilizing, warm-keeping and cooling.
The spray sterilization cooling tunnel has a wide and practical application in the food industry. The following are some specific cases:
1. Bottled and canned beverages: such as acidic dairy products, fruit juice drinks, electrolyte drinks, alcoholic beverages, and seasonings. After being filled and sealed, they are sterilized by high-temperature spray hot water through this tunnel, and then cooled in stages to the appropriate storage temperature to ensure safety and quality.
2. Canned fruits and vegetables: Used for processing canned fruits and vegetables, high-temperature sterilization ensures food safety, while preserving product color, nutrition, and flavor, and maintaining commercial sterility.
3. Condiments and sauces, such as tomato sauce, chili sauce, salad dressing, etc., need to be thoroughly sterilized to prevent the risk of microbial contamination caused by high water activity, while protecting product quality from being affected.
4. Dairy products: including yogurt, milk, etc., sterile filled and processed through tunnels to ensure the elimination of harmful bacteria and rapid cooling to the ideal storage temperature, reducing the risk of quality decline.
These cases highlight the important role of spray sterilization cooling tunnel in ensuring food safety, improving production efficiency and maintaining the quality of end products, and reflect its necessity and flexibility in modern food processing.
Technical parameter:
Model |
PLS-3000 |
PLS-6000 |
PLS-8000 |
PLS-12000 |
PLS-18000
|
|
Maximum sterilize temperature |
100℃ |
|||||
Line speed of the conveyor |
110-553mm/min Step-less speeding |
|||||
Heating steam pressure |
0.4MPa |
|||||
Heating water consumption |
21 |
40 |
55 |
80 |
120 |
|
Total power (kw) |
9.6 |
10.6 |
13.6 |
16.5 |
25 |
|
External dimension (mm) |
Length |
6500 |
14000 |
18880 |
21880 |
31000 |
Width |
2250 |
2750 |
||||
Height |
1735 |
1735 |
||||
Weight(kg)
|
3000 |
5000 |
6500 |
8500 |
12000 |
|
Tunnel area(m2)
|
13.5 |
26.5 |
34 |
51 |
76 |
This machine can be designed according to the customer’s requirements.
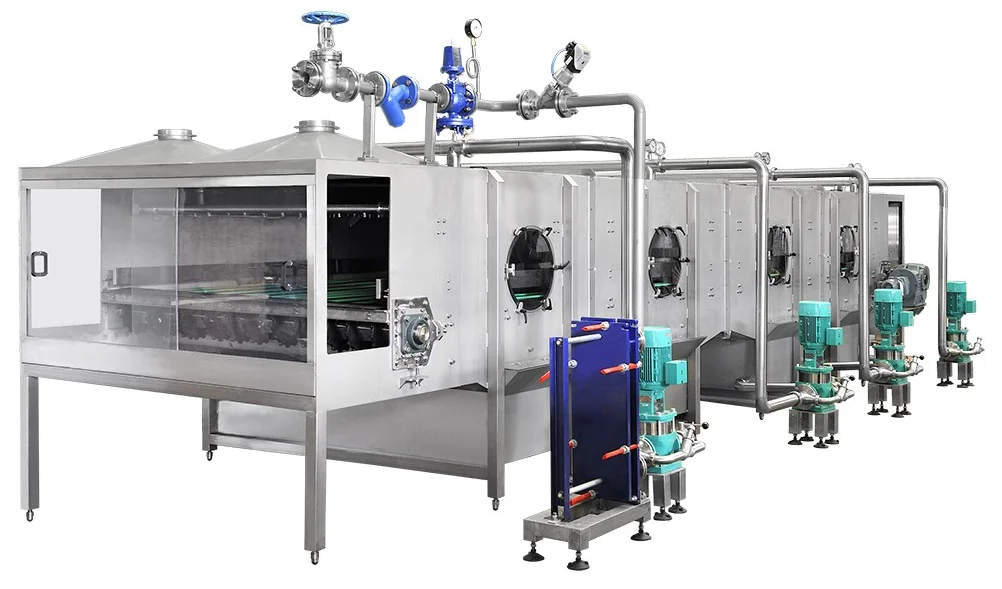
Material
|
AISI304/316
|
Sterilizing temperature
|
65-105℃ (adjustable)
|
Holding time
|
0-5min (adjustable)
|
Control type
|
Siemens PLC full-automatic touch screen control;
|
|
connnection for homogenizer and degasser are reserved, connection type is union type or clamp type, connection size to be
provided by clients. |
Customization of spray sterilization cooling tunnel
The customized service of spray sterilization cooling tunnel is designed and produced according to the specific needs of customers. To provide the most suitable solution for you, the following steps are usually key steps in the customization process:
1. Requirement analysis: Firstly, we will have a detailed understanding of your production requirements, including product types, output, production line speed, factory layout, and any special requirements such as space constraints, energy efficiency targets, etc.
2. Design consultation: Based on the collected information, our engineers will have in-depth communication with you to discuss possible design solutions. This includes the size of the tunnel, configuration of the spray system, accuracy of the temperature control system, material selection (corrosion resistance and cleaning convenience need to be considered), etc.
3. 3D modeling and review: Use CAD software to create a 3D model of the equipment, allowing you to visually see the design layout. This step facilitates the review and adjustment of design details by both parties, ensuring that all technical requirements and expectations are met.
4. Prototype testing: In some cases, prototypes may be made or local functional tests may be conducted to verify the feasibility and performance indicators of the design, especially when there are innovative designs or special requirements.
5. Production and installation: Once the design scheme is confirmed, we will enter the production phase. Each component of the customized equipment will be manufactured strictly according to the design specifications, and a professional team will be arranged to be responsible for on-site installation and debugging.
6. Training and after-sales service: After the equipment is installed, we will provide detailed training for your operators to ensure that they are proficient in operating and maintaining the equipment.
In addition, we will provide long-term technical support and after-sales service to ensure the long-term stable operation of the equipment. If you want to learn more about customized services or start discussing your specific project, please contact the sales or technical support team of the equipment supplier, who will provide you with personalized consulting services and quotations.