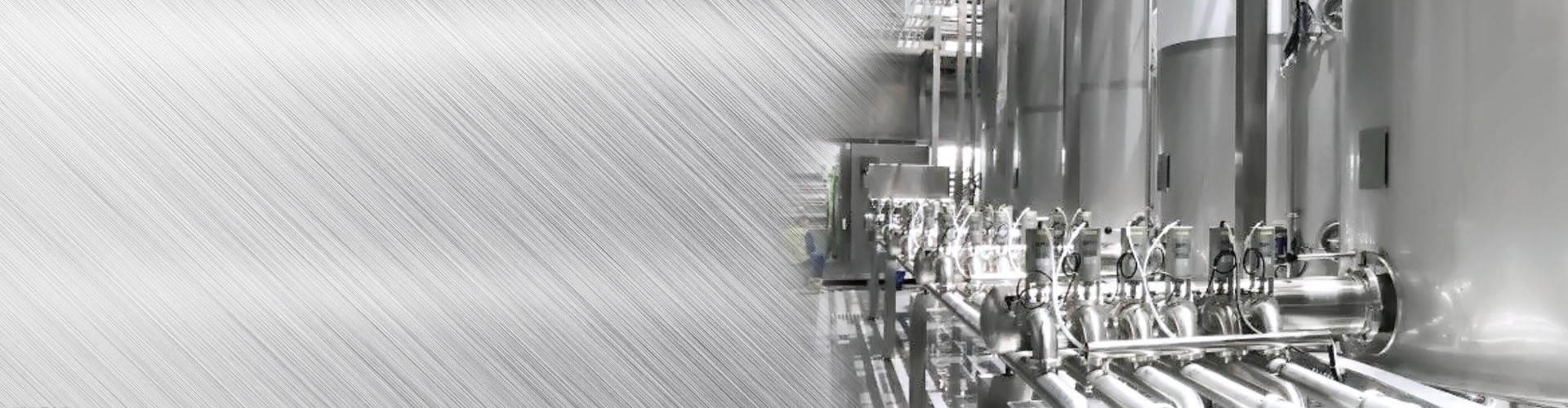
The construction of an apple processing plant involves multiple aspects, including site selection, facility construction, production equipment procurement, human resource allocation, and raw material supply chain. Firstly, market research is needed to determine the geographical location of the processing plant, taking into account its proximity to the apple planting base for obtaining fresh raw materials and facilitating logistics transportation. After determining the site selection, it is necessary to conduct land planning and environmental assessment to ensure that the construction of the factory complies with local regulations and environmental requirements.
In terms of facility construction, it is necessary to design a factory layout that meets production needs, and consider the rationality and efficiency of the production process. At the same time, it is necessary to build supporting office buildings, employee dormitories, canteens and other facilities to provide employees with good working and living conditions.
In terms of production equipment procurement, it is necessary to select appropriate equipment based on the processing technology, such as washing, peeling, slicing, packaging and other equipment, and ensure that the quality and performance of the equipment meet production requirements.
In terms of human resource allocation, it is necessary to recruit technical personnel with processing experience, establish a production management team, develop production plans and quality control standards, train production operators, and ensure the normal operation of the production line.
In addition, building an apple processing plant also requires establishing a sound raw material supply chain, establishing stable cooperative relationships with apple planting bases or suppliers, ensuring timely supply of raw materials and controllable quality.
Finally, it is necessary to consider the marketing strategy and product sales channels of the processing plant, develop a marketing promotion plan, and push the processed apple products to the market to achieve economic benefits.
Apple processing line equipment usually includes the following main parts:
1. Cleaning and sorting equipment: These devices are used to clean and remove impurities from the original apples, and classify them according to size and quality level.2. Peeling and nucleating equipment: For different processing needs, apples may need to be peeled and nucleated. These devices can automate these steps.
3. Slicing or cutting equipment: Slice or cut processed apples for subsequent processing or packaging.
4. Drying equipment: used to dry cut apples to extend their shelf life, and can also be used to produce dried fruit products.
5. Soaking or pickling equipment: If it is necessary to produce products such as preserved fruits or jam, apples may need to be soaked or pickled, which requires corresponding equipment.
6. Packaging equipment: Finally, the processed apple products need to be packaged. This includes equipment such as packaging bags, sealing machines, labeling machines, etc.
The above are the basic components of general apple processing line equipment, and of course, the specific processing line equipment may vary depending on the processed products.
1. Cleaning and sorting: Clean the picked apples to remove surface impurities and dirt. Then sort according to characteristics such as size and maturity for subsequent processing and use.
2. Peeling and nucleating: Peeling and nucleating apples can be done automatically through mechanical equipment to improve efficiency.
3. Slicing or chunking: According to product requirements, apples are sliced or chunked, usually classified according to different specifications.
4. Dehydration treatment: Cut apples are dehydrated to remove excess moisture, which helps maintain the taste of the product and extend its shelf life.
5. Drying: Apples that have undergone dehydration treatment are usually dried using hot air circulation drying equipment to achieve the required moisture content.
6. Packaging: Finally, the processed apple products are packaged, usually using vacuum packaging or modified atmosphere packaging, to maintain the freshness and quality of the products.
The above is the general process of an apple processing line, and the specific design of the processing line may vary depending on the type and scale of the product.
The operation and maintenance of apple processing lines involve multiple aspects, including equipment operation, production management, and equipment maintenance. The following are the relevant contents for the operation and maintenance of apple processing lines in general:
-Operators need to receive professional training to understand the operating procedures, safety precautions, and operating procedures of apple processing equipment.
-According to the requirements of the operation manual, operate the cleaning, peeling, slicing, squeezing and other processing equipment correctly to ensure standardized and safe operation.
2. Production management:
-Ensure the quality of raw materials, conduct preliminary screening, cleaning, and classification of apples to ensure that the processed products meet quality standards.
-Control the temperature, humidity, and processing time during the production process to ensure product quality and safety.
3. Equipment maintenance:
-Regularly inspect and maintain apple processing equipment, including cleaning, lubrication, and replacing vulnerable parts, to ensure the normal operation of the equipment and extend its service life.
-Promptly handle equipment malfunctions, and for larger malfunctions, professional maintenance personnel are required for repair and upkeep.
4. Security management:
-Strengthen safety awareness training, ensure that operators strictly follow operating procedures, use personal protective equipment correctly, and prevent potential accidental injuries during operation.
-Strengthen equipment safety protection, ensure that equipment meets safety standards, set up safety warning signs, and conduct regular safety inspections to ensure safety during the production process.
The above is the relevant content for the operation and maintenance of apple processing lines in general, and the specific situation needs to be analyzed and operated according to the actual situation.
The automation control of apple processing line refers to the use of advanced control systems and equipment to automate and monitor various aspects of the apple processing production line. This includes automatic control of apple sorting, cleaning, cutting and packaging.
On the apple processing line, a PLC (Programmable Logic Controller) can be used as the control core to obtain information about apples, such as size, weight, color, etc., through sensors, and then sort and locate them according to the preset program. Next, automated equipment such as robotic arms and conveyor belts will be used to clean, cut, and package apples. The entire process can be monitored and scheduled through a human machine interface (HMI).
In addition, a visual recognition system can be introduced to detect and sort apples through cameras, improving the accuracy and efficiency of automated control. At the same time, data collection and analysis are also an indispensable part of automation control. Through the analysis of production data, the production process can be optimized, and production efficiency and quality can be improved.
Overall, the automation control of apple processing lines can improve production efficiency, reduce labor costs, reduce human errors, and adapt to production of different scales and needs.
The final product of an apple processing line can be various apple products, such as apple juice, apple jam, dried apples, apple cider vinegar, apple jam, etc. These products can be consumed directly or used as raw materials for food processing, and are widely used in the food industry.
The energy consumption of apple processing lines depends on many factors, including production scale, equipment efficiency, processing process, and energy type. Generally speaking, the energy consumption of apple processing lines mainly includes the following aspects:
1. Mechanical equipment: Various mechanical equipment used in apple processing lines, such as cleaning equipment, cutting equipment, drying equipment, etc., usually require electricity or other forms of energy drive.
2. Heating and cooling: In processes such as juice extraction and jam production, heating or cooling equipment may be required, which typically consumes a large amount of energy.
3. Lighting and air conditioning: The lighting and air conditioning systems inside the processing plant also consume a lot of energy, especially in large processing plants.
4. Transportation and packaging: Energy consumption also includes the transportation of raw materials and finished products, as well as the energy required during the packaging process.
In order to reduce the energy consumption of apple processing lines, a series of measures can be taken, such as optimizing equipment efficiency, adopting energy-saving equipment, improving processing processes, and promoting the utilization of renewable energy. At the same time, energy consumption can also be monitored and optimized through energy management systems to achieve sustainable development and improve resource utilization efficiency.
Shanghai Beyond Machinery Co., Ltd
Beyond Machinery specializes in the design and manufacturing of apple processing plants. Please contact us now, and our professional technical engineers will customize the equipment plan for apple processing plants and provide a quotation. Please contact us now to obtain the latest equipment plan and quotation.