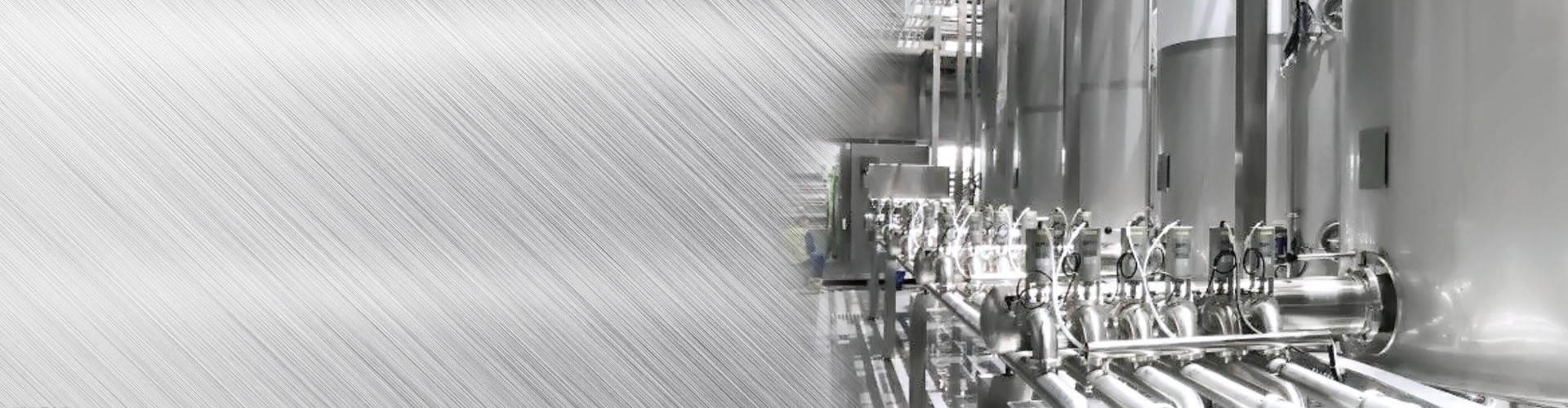
In order to better adapt to the development trend of society, the beverage industry has changed traditional beverage production lines, introduced automation control technology, and introduced PLC for control in automation control technology. The addition of PLC makes the operation of automated beverage production lines more stable and functional, greatly improving the production efficiency of beverages.
1.1 Composition and structure of PLC
The essence of Programmable logic controller (PLC) is a computer dedicated to industrial control, so it has many similarities with other controls and mechanisms.
(1) Power supply
PLC power supply plays a very important role in the whole system. Without a power supply with high and stable Factor of safety, the whole system cannot operate normally. Therefore, PLC makers attach great importance to the design and manufacture of power supply.
(2) Central Processing Unit (CPU)
CPU is the core of Programmable logic controller (PLC), mainly composed of memory and microprocessor. It can receive and store relevant data information, check the working status of power and memory in real time, and remind users of operational errors to make timely corrections.
(3) Programming equipment
Programming device is an important peripheral device of Programmable logic controller, which can effectively check, modify, debug and monitor user programs.
(4) Input and output modules
The input and output module is the main interface between the Programmable logic controller (PLC) and the field equipment to ensure the normal operation of the PLC.
(1) Flexible PLC system control
PLC is a high-performance processor that combines the advantages of high integration and small size. Introducing PLC into the control system has a great effect on improving the automated beverage production line, as it can replace the cumbersome circuits and wiring in the original system. Because PLC system control is relatively flexible, PLC technology is very suitable for automated beverage production lines. It can keep up with the development pace of the times for real-time updates, and there is no need for large-scale changes during updates. Simply disassemble the original PLC and replace it with a new processor.
(2) High security
The emergence of PLC systems has greatly reduced human workload. In some engineering monitoring, human monitoring is no longer required. Instead, the PLC provides corresponding sensors to transmit the specific situation of the project site to the PLC processor, which can effectively monitor the data parameters of the project in detail. This working mode greatly reduces errors in the work and improves accuracy.
The normal operation of the automated beverage production line system is mainly achieved by setting the manual production mode to automatic production mode through a switch. Once the switch is activated, the conveyor belt begins to operate, and this behavior is maintained until the switch is turned off or the filling sensor detects that another bottle is full. When the next empty bottle reaches the sensor, the conveyor belt will be restarted. The specific requirements for its operation are: first, when the empty bottle is under the filling sensor, pause for 1 second, and then fill the number of boxes. Once again, upload the recorded number of beverage containers at regular intervals and reset the counter to continue recording.
3.1 Design of PLC hardware control system
The design of the conveying part in PLC hardware is mainly a conveying device that controls the bottles. According to relevant requirements, the conveying belt requires a dedicated motor for control, and at the same time, a frequency converter is also used to smoothly adjust the speed of the motor. The conveyor belt is a carrier for transporting bottles, which needs to be continuously rotated and transported to a fixed position. It can also be said to be a transportation machine. Conveyor belts are classified based on the presence or absence of traction components, and are divided into conveyor belt machines with traction components and conveyor belt machines without traction components.
In the design process of PLC systems, a ladder diagram (as shown in Figure 3) is usually used, which is characterized by a more visual and intuitive observation of the entire structure. When the PLC system starts to operate, its initial current is relatively large. If the motor is judged to operate normally only because of the current, it is easy to cause misjudgment. We can effectively avoid alarm problems caused by high initial current through the design of system software, so that the working current can enter the normal monitoring state. In the software design process, an emergency stop button is set so that the entire production line cannot be stopped in case of unexpected situations. At present, the design concept of PLC ladder diagram is mainly based on rich experience, and the design concept of empirical method is mainly based on the circuit diagrams of traditional relays and contactors, using ladder diagram as the programming language to achieve control of the entire motor system. Because each experience is different, different ladder diagrams may appear.
With the rapid development of the Social market economy, the competitiveness of enterprises in the market is growing. If you want to stand firm in the market and move forward, you must improve the production efficiency of enterprises and reform the production technology of products. At present, people's pace of life is becoming faster and faster, and beverages have become a necessity in people's lives. The beverage industry has also developed rapidly. In order to improve the production efficiency of the beverage industry, enterprise leaders have begun to innovate and reform the production line of beverages. The introduction of PLC system in the production line of automated beverages by enterprises has improved the shortcomings of the original automated beverage production line, greatly improved the production efficiency of beverages, and reduced the production costs of enterprises. PLC itself has great advantages in data analysis and storage. By connecting the entire production line through electronic information technology, it is convenient for leaders to guide the production line. Relevant leaders can also timely understand some possible problems in automated beverage production lines, conduct detailed data analysis of the problems that may arise, and develop effective solutions.
5. Strengthen installation management and daily maintenance
The main purpose of strengthening installation management and daily maintenance is to ensure the safety of the PLC system when applied in automated beverage production lines. Firstly, before installing the PLC in the original automated beverage production line, it is necessary to strictly control the quality issues of the PLC and conduct comprehensive inspections. Only after the inspection results are qualified can the installation be carried out to avoid malfunctions in future work. Secondly, after the installation of the PLC system, the relevant workers should strengthen the daily maintenance and overhaul of the equipment. In addition, during the overhaul, the quality of the overhaul should be guaranteed, and not perfunctory. Some system modifications and changes in the Technology roadmap should be recorded in detail for later inspection and maintenance. Once again, the main equipment that ensures the safety of the PLC system includes the following parts: power supply, central processing unit, signal template, relay for output and input of life elements, and the entire installation status. The safety performance of each part is strictly checked to ensure that it can operate normally. Finally, improve the overall quality level of relevant staff, strengthen the management of staff, ensure that staff are capable of their own job positions, familiar with relevant work processes, and also possess professional computer skills. Relevant leaders should attach great importance to the training of staff, regularly organize skill training, improve their knowledge and skills, and enable their thinking to keep up with the pace of development of the times and keep up with the times.
6 Conclusion
The emergence of PLC systems has pushed the development of industrial automation to a new climax. The application of PLC systems in automated beverage production lines has to some extent simplified the control process of beverage production lines, improved control efficiency and production efficiency. The article analyzes the relevant overview of PLC, understands the main characteristics of PLC system, flexible control and high safety, understands the control requirements and software design of beverage production lines, and provides a detailed analysis of the application status of PLC in automated beverage production lines. The application of PLC is beneficial for improving production efficiency and reducing production costs of enterprises. At the same time, research was conducted on how to strengthen the installation management and daily maintenance of the PLC system, ensuring the safety of the operation of the automated beverage production line, and providing favorable conditions for promoting the development of the enterprise.