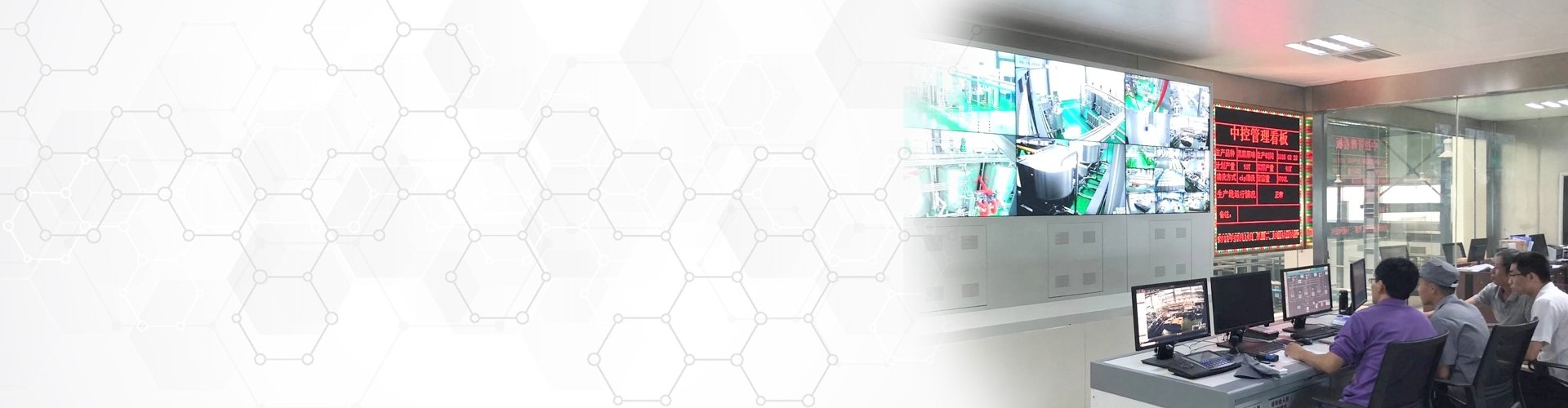
The jujube jam processing production line involves a series of production steps, including the selection of raw dates, pretreatment, boiling, pulping, seasoning, sterilization, filling, sealing, inspection, packaging, etc.
The following are the main technical points and processes of the production line:
Raw material selection and pretreatment: • Select high-quality red dates that are mature, free from pests and diseases, and free from mold as raw materials Cleaning: Thoroughly clean the soil and impurities on the surface of red dates with flowing water De nucleating: Remove the pits from red dates by using a de nucleating machine or manual de nucleating Soaking: Soak the pitted red dates in clean water to soften and facilitate subsequent processing Boiling and beating: • Heating and boiling: Put the processed red dates into a large boiling pot, add an appropriate amount of water, and simmer over low heat until the red dates are soft and tender.
• Beating: Use a beater to beat cooked red dates into a delicate paste, and adjust the degree of beating as needed to obtain the desired jam consistency Seasoning: According to the product formula, add sugar (such as granulated sugar, honey, etc.), lemon juice or vinegar (to adjust acidity), spices, etc. to the jujube paste for seasoning, improving taste and flavor.
• Sterilization and cooling: • Sterilization treatment: High temperature instantaneous sterilization (HTST) or ultra-high temperature sterilization (UHT) technology is used to ensure the food safety of jam and extend its shelf life Rapid cooling: After sterilization, quickly cool to a suitable temperature to prevent excessive heat treatment from affecting flavor and nutritional value.
• Filling and sealing: The automatic filling machine quantitatively pours the cooled jujube sauce into pre disinfected glass or plastic bottles Then proceed with sealing to ensure sealing and avoid secondary contamination Inspection and packaging: • Conduct quality inspections on the filled finished products, including appearance, taste, microbiological indicators, etc Using automated packaging lines for external packaging may include steps such as labeling, boxing, and wrapping, ultimately forming a sales unit.
• Warehousing and logistics: The packaged jujube jam is stored in the warehouse, sorted and boxed according to order requirements, and delivered to retailers or directly to consumers through cold chain logistics. Throughout the production process, emphasis is placed on hygiene control, quality monitoring, and efficiency optimization to ensure the quality and safety of jujube jam products.
In addition, with technological progress, the application of automation and intelligent technology is becoming increasingly widespread, such as using intelligent control systems to monitor production parameters, using robots for material handling, etc., in order to improve production efficiency and reduce labor costs.
1. Wide range of raw materials, this production line is suitable for the fruit similar to jujube and hawthorn, dry jujube and fresh jujube;
2. The production line has two processes: extraction and beating;
3. According to different investment amount and product positioning of customers, customers can configure ordinary, middle end or high-end products according to their own requirements;
4. The final product has pure flavor, bright color and high comprehensive utilization rate of raw materials;
5.The whole line has high degree of automation, low labor intensity, simple operation, reliable performance and low operation cost;
6. The whole production line adopts sanitary design, with thorough cleaning and high hygiene level.
Technical parameter:
All kinds of raw materials: hawthorn, jujube
Final products: NFC, concentrated juice, clear juice, turbid juice, jujube juice, hawthorn juice, preserved fruit, etc
Capacity: 20 t / D - 400 t / D
Fruit juice yield: ≥ 90%
Solid content: 7 ~ 11brix
Product packaging: aseptic big bag / glass bottle / PET bottle / roof bag / Tetra Pak, etc
Jujube juice extracting system
The jujube extracting process is the core processing in the jujube juice and syrup prcessing line,it mainly includes two steps:hot water extrction and adding enzyme preparation for enzymolysys.The jujube juice yield rate is 55%-60% with these two methods applied.
Hot water extraction: This process is carried out in the SUS304 extraction tank,the jujube pulp and 70°C hot water ratio are 1:3 in the extraction tank,the PH is adjusted to 6.0±0.2,then start the stir to blending for 2 hours.After heating the slurry was filtered through a vibrate screen filter to remove large impurities and insoluble matters.
Enzmatic hydrolysis:Pectinase and cellulose enzyme preparations were added at the rate of 1% for each on a date pulp weight basis in the enzymatic hydrolysis tank.The mixture of date pulp,water and enzyme preparations are mixed carefully and incubated at 50±2°C for 2 hours with a continuous blending.The date juice extraction system results in a main product(date juice)and a by-product(presscake).Crude juice contains soluble and insoluble solids as well as foreign matter.
Date juice clarification system
Several technologies have been employed for clarification of date juice,such as juice pretreatment by boiling,precipitating or hydrolyzing colloids by enzyme,removing insoluble foreign matters by means of filtration or centrifugation,decolorrization using activated carboon or ion exchange,removing the minerals using chemicals or ion exchange,and removing high molecular weight compounds by foaming.The mature technology is that the jujube juice is first filtered through a plate and frame filter,and then use the ultrafiltation system to filter it twice,so that we get a clarified jujube palm juice.
Date syrup concentration system
After refining and filtration,jujube juice with soluble solid content of 20-25% will be obtained,which needs to be concentrated.The most common soluble solid content of jujube syrup is 75%.The falling film evaporator is applied to cocentrated the date juice to jujube syrup.
Date syrup filling machine
The date syrup after concentration,then cooled down to 30°C,and filling into the bottles or metal cans.As the syrup does not pasteurize,to extend the shelf life,the vacuum filling machine is suggested.
Flow No. | Name | Size | Main technical parameter |
The first stage for concentrated dates syrup(A,B,D,E system) | |||
Washing & Pulping system | |||
A-1 | Bubble spraying washing machine | 500kg/H | SUS machine frame, eccentric vibration motor, spray cleaning device, air blower, stainless steel air knife, removable sieve, the water collecting pan at the bottom of the machine, concentrated drainage, size:2000*1200mm |
A-2 | Slope type spiral precooking machine | 500kg/H | SUS 304, U shape barrel structure, insulation, with miller jacket, top opening, easy to clean, the cooking time can be adjusted by frequency conversion( no less than 10~60mins), counting based on dry date |
Temperature control system | Spirax Sarce pressure reducing trap valve, German temperature testing system, Burkert angle seat valve, domestic famouse brand stop valve, filter and pressure gauge etc. | ||
Flowmeter | 2T/H | SUS304, pointer-type | |
A-3 | Stone washer | 2T/H | SUS304 support, with ABB motor |
A-4 | Screw pump | 2T/H | The material contact part are all food grade rubber, and the pressure of the outlet is 0.6MPa, frequency conversion speed regulation |
A-5 | Single stage pulping machine | 2T/H | SUS304, rotary speed 960rpm,screen hole diameter 1.0mm, |
A-6 | Buffer tank | 300L | SUS304,double layer, with ladder, adjustable feet, and cone type cover, with flange type outlet at the bottom, electrode type liquid level, digital temperature sensor. With CIP cleaning balls, inlets for pure water and material |
A-7 | Screw pump | 2T/H | The material contact part are all food grade rubber, and the pressure of the outlet is 0.6MPa, frequency conversion speed regulation |
A-8 | Tubular cooler | 2T/H | SUS304, tubular type, tower water cooling |
A-8 | Pulping platform | carbon steel support, anti slip stainless steel checkered plate, steps, guard bar, central drainage,L*W*H=3500mm×3000mm×2000mm | |
B | Filteration and clarification system | ||
B-1 | Storage tank | 2000L | SUS304, double layers,use PU as insullation,miller jacket, rotation speed: 36rpm. airtight manhole, cone type cover, off-center vertical agitator ,and on the top has CIP cleaning balls, digital thermometer, sight glass to show the level, adjustable feet, breathing valve, and tie valve at the bottom |
B-2 | Centrifugal pump | 3T/H | SUS304, lift 24m, mechanical seal |
B-3 | Decanter | 2T/H | Counter-current type, drum max speed:3600 r/min |
B-4 | Receiving vat | 500L | SUS304, single layer, CIP spraying ball, adjustable legs |
B-5 | Centrifugal pump | 3T/H | SUS304, lift 24m, mechanical seal |
B-6 | Storage tank | 2000L | SUS304, double layers,use PU as insullation, airtight manhole, cone type cover, off-center vertical agitator ,and on the top has CIP cleaning balls, digital thermometer, sight glass to show the level, adjustable feet, breathing valve, and tie valve at the bottom |
B-7 | Centrifugal pump | 5T/H | SUS304, lift 36m, mechanical seal |
B-8 | Inorganic membrane Micro filter | 1T/H | SUS 304, Inorganic ceramic membrane filter element, filter precision1 u, with circulation pump |
C | Concentrate system | ||
C-1 | Storage tank | 2000L | SUS304, double layers,use PU as insullation, airtight manhole, cone type cover, off-center vertical agitator ,and on the top has CIP cleaning balls, digital thermometer, sight glass to show the level, adjustable feet, breathing valve, and tie valve at the bottom |
C-2 | Centrifugal pump | 3T/H | SUS304, lift 24m, mechanical seal |
C-3 | Double effect falling film concentrator | 1.5T/H | Product contact: SUS 304,evaporation control, brix/temperature are all fully controlled, falling film evaporator, downstream |
C-4 | Tubular cooler | 0.5T/H | SUS304, tubular type, tower water cooling, cooling temperature 30ºC in one time |
C-5 | Storage tank | 2000L | SUS304,three layers, with miller jacket, use PU as insullation, airtight manhole, cone type cover, and on the top has CIP cleaning balls, digital thermometer, sight glass to show the level, adjustable feet, breathing valve, off-center vertical agitator, and tie valve at the bottom |
C-6 | Rotary pump | 1T/H | The material contact part is SUS304, 0.6MPa, ftrequency conversion |
D | CIP UNIT | ||
D | Semi-automatic CIP system | 3×1T | Three tanks, single circulation, Semi-auto CIP, double layer insulation tank, tank material SUS304 stainless steel,acid&alkali tank with stirrer, high&Low liquid level alarm system, Spirax Sarco temperature auto control, JUMO temperature sensor, Shanghai YUAN brand progress pump 1 pieces, 10T/H, pumping lift 36M, ABB motor,100L concentrated acid & alkali tank which material is SUS316L , The USA imported pneumatic diaphragm pump two pieces. |
The second stage(dates clear juice system) | |||
E. Filteration and clarification system | |||
E-1-2,3 | Enzyme tank for clear juice | 2000L | SUS304, double layers,use PU as insullation,dimple jacket, airtight manhole, cone type cover, off-center vertical agitator ,and on the top has CIP cleaning balls, digital thermometer, sight glass to show the level, adjustable feet, breathing valve, and tie valve at the bottom |
E-4 | Enzyme Circulation tank | V=5000L | SUS304, single-layer, top offset vertical mixing 36rpm, ladder, conical head, digital thermometer, sampling valve, adjustable legs, glass tube level, climbing ladder |
E-5 | The cleaning tank | V=5000L | SUS304, single-layer, ladder, conical head, digital thermometer, adjustable legs, glass tube level, climbing ladder |
E-6 | Membrane filtration unit | 1T/H | SUS304, aperture: 0.01 μ m; with cleaning device, automatic control |
E-7 | Storage tank | 2000L | SUS304, double layers,use PU as insullation, airtight manhole, cone type cover, off-center vertical agitator ,and on the top has CIP cleaning balls, digital thermometer, sight glass to show the level, adjustable feet, breathing valve, and tie valve at the bottom |
E-8 | Centrifugal pump | 5T/H | SUS304, lift 36m, mechanical seal |
R | CIP return pump | 20T/H | SUS316L stainless steel, pump lift is 24 meters, mechanical seal |
F . Dates clear juice: decoloration unit | |||
F-1 | Resin decolorizing tank | SUS304 material, 2m³ resin tank, it's easy to loading, unloading, resin can be regenerated, without the resin | |
F-2 | Resin regeneration tank | 2000L | SUS316L, double insulation, taper sealing head and eccentric vertical mixing, the respiration valve, the digital display thermometer, steam coil heating, manual control temperature, glass tube liquid level meter |
F-3 | Acid tank | 1000L | SUS316L, single layer, taper sealing head and eccentric vertical mixing, the respiration valve, the digital display thermometer, glass tube liquid level meter |
F-4 | Alkali tank | 1000L | SUS316L, single layer, taper sealing head and eccentric vertical mixing, the respiration valve, the digital display thermometer, glass tube liquid level meter |
F-5 | Centrifugal pump | 10T/H | SUS316L, lift 36m, machinery seal |
F-6 | Operating platform | SUS304, anti slip stainless steel checkered plate, steps, guard bar, central drainage,L*W*H=6000mm×1000mm×1500mm | |
F-7 | Twin piping filter | 2T/H | SUS304 stainless steel, duplex type, Stainless Steal Filter 200 Mesh |
G | Date vinegar fermetation system | ||
G-1 | Plate sterilizer | 1T/H | Full automatic control by Siemens PLC, sterilization temperature of 95 ºC, 30S, discharge temperature of 30 ºC, the British Sipaishake steam temperature control system, with its CIP cleaning system |
G-2 | Dates alcohol fermentation tank | 8000L | SUS304, three-layer, miller jacket, insulation, conical head, top agitator, ladder, glass tube level, digital thermometer, sampling valve, discharge valve with union. |
Temperature sensor | PT100 | SUS304, 4-20mA signal output, tail length 100mm | |
G-3 | Centrifugal pump | 3T/H | Material is SUS304 stainless steel, high quality mechanical seal, H=24m, ABB motor |
G-4 | Plate and frame filter | 3T/H | plate and frame filtering machine, 400mesh, SUS 304 plate frame, filtering area 10M² |
G-5 | Date vinegar fermentation tank | 8000L | SUS304, three-layer, miller jacket, rock-wool thermal insulation, butterfly head ,top agitator, product inlet, steam inlet, sealed manhole, ladder, glass tube level, digital thermometer, sampling valve, discharge valve with union |
Temperature sensor | PT100 | SUS304, 4-20mA signal output, tail length 100mm | |
PH-instrument | 4-20mA signal output | ||
Dissolved oxygen detector | 4-20mA signal output | ||
G-6 | Centrifugal pump | 3T/H | Material is SUS304 stainless steel, high quality mechanical seal, H=24m, ABB motor |
G-7 | Plate and frame filter | 3T/H | plate and frame filtering machine, 400mesh, SUS 304 plate frame, filtering area 10M² |
Raw materials and products of date processing production line
1. Raw materials
The raw materials required for the production of date syrup mainly include:
1. Date:
• Variety selection: Select the appropriate date variety according to market demand and product quality requirements. Commonly used are Medjool Dates, dates, etc.
• Quality standard: Dates should be fresh, free of mold and pests, with moderate water content and high sweetness.
2. Water:
• Water quality requirements: The water used to wash dates and dilute syrup should meet the drinking water standards to ensure no pollution and no odor.
3. Auxiliary materials (optional):
• Preservatives: Add a small amount of food-grade preservatives to extend the shelf life of the syrup.
• Thickeners: Such as pectin, agar, etc., to adjust the viscosity of the syrup.
• Flavoring agents: Such as flavors, citric acid, etc., to improve taste and flavor.
2. Products
The processing line of dates (also known as dates) can produce a variety of high value-added products. The specific product types and characteristics are as follows:
1. Dried dates
•Appearance: brown to dark brown, dry texture, smooth or slightly wrinkled surface.
•Taste: sweet, fragrant, with natural date aroma, no odor.
•Use: direct consumption, as a snack or added to baked goods, salads, desserts, etc.
2. Date Syrup
•Appearance: brownish red to dark brown, clear or slightly turbid.
•Taste: sweet, rich, with natural date aroma, smooth in the mouth.
•Use: used as a natural sweetener, widely used in food processing, catering industry and household consumption. It can replace white sugar or other artificial sweeteners.
3. Date Paste
•Appearance: dark brown, soft and sticky texture.
•Taste: sweet, delicate, with a strong date flavor
• Application: used in baked goods (such as bread, cake), candy making, jam spreading, etc.
4. Date Powder
• Appearance: light brown to brown, powdery, fine texture.
• Taste: moderate sweetness, with the unique aroma of dates.
• Application: used as ingredients in food processing, such as beverages, cakes, energy bars, ice cream, etc.; can also be used in health products and functional foods.
5. Date Concentrate
• Appearance: dark brown, highly concentrated, high viscosity.
• Taste: very sweet, with a strong date flavor.
• Application: used as a condiment and sweetener, widely used in the production of beverages, yogurt, desserts, etc.
6. Date Slices
• Appearance: evenly sliced, consistent thickness, maintaining the original color and texture of the dates.
• Taste: sweet, fragrant, suitable for chewing.
• Application: eaten directly, or as a snack, dessert ingredient, can also be used in baked goods
7. Date Extract
• Appearance: Brown liquid or powder, depending on the extraction method.
• Ingredients: Rich in polyphenols, antioxidants and other bioactive substances.
• Uses: Used in health products, skin care products and functional foods, and is highly favored for its antioxidant and nutritional ingredients.
8. Date Candies
• Appearance: Transparent or translucent, with various shapes, such as spheres, bars, etc.
• Taste: Sweet but not greasy, with the fragrance of dates.
• Uses: As a snack or holiday gift.
9. Date Beverages
• Appearance: Brown or amber, clear or with slight precipitation.
• Taste: Sweet and mellow, with the natural aroma of dates.
• Uses: Healthy drinks, such as date milkshakes, date tea, date juice, etc.
Customizing a Dates Paste and Syrup production line is a complex and multi-step process that involves multiple stages such as raw material processing, processing, and packaging. Here is a detailed customized solution to help you plan and implement this project:
1. Requirement analysis
•
Product Objective: Determine the date syrup and type of syrup you wish to produce (such as plain, low sugar, organic, etc.).
•
Production scale: Determine the daily or hourly production capacity.
•
Quality standards: Clarify the quality standards of the product, including taste, color, nutritional content, etc.
•
Market positioning: Determine the target market and consumer group of the product.
2. Process flow design
Raw material processing
•
Raw material receiving: Set up a raw material receiving area to ensure the freshness and hygiene of the raw materials.
•
Cleaning: Use a cleaning machine to remove impurities and dust from the surface of raw materials.
•
De nuclear: Use a de nuclear machine to remove jujube pits.
•
Slicing/cutting: Slice or cut the pitted jujube fruit for subsequent processing.
machining
•
Steaming/Softening: Use steam or hot water to soften jujube fruits, making them easier to process.
•
Beating: Use a beater to mash softened jujube fruits into a pulp.
•
Filtration: Use a filter to remove fibers and other impurities from the slurry.
•
Concentrate: Use an evaporator to concentrate the slurry to the desired concentration, forming syrup.
•
Mixing: Add other ingredients (such as water, sugar, preservatives, etc.) as needed to adjust the taste and quality of the syrup.
packing
•
Cooling: Cool the concentrated syrup to a suitable temperature.
•
Filling: Use a filling machine to fill syrup into bottles or bags.
•
Sealing: Use a sealing machine to seal the packaging to ensure sealing.
•
Labeling: Use a labeling machine to attach labels to the packaging, indicating product information.
3. Equipment selection
•
Raw material receiving area: conveyor belt, storage bin.
•
Cleaning machine: Bubble cleaning machine or spray cleaning machine.
•
De nuclear machine: an efficient de nuclear machine.
•
Slicing/cutting machine: Multi functional slicing and cutting machine.
•
Steaming/softening equipment: steam tank or hot water tank.
•
Beating machine: Efficient beating machine.
•
Filter: Multi stage filter.
•
Evaporator: Vacuum evaporator or thin film evaporator.
•
Mixing tank: Stainless steel mixing tank.
•
Cooling equipment: Plate heat exchanger or cooling tower.
•
Filling machine: Automatic filling machine.
•
Sealing machine: rotary sealing machine or heat sealing machine.
•
Labeling machine: automatic labeling machine.
4. Technical consultation and evaluation
•
Supplier selection: Choose experienced equipment suppliers for technical consultation to understand the strengths and weaknesses of different suppliers.
•
Cost assessment: Evaluate the cost of equipment, including purchase cost, installation cost, operating cost, and maintenance cost.
•
Technical evaluation: Evaluate the technical performance of equipment to ensure that it meets production requirements and quality standards.
5. Scheme confirmation
•
Technical exchange: Conduct detailed technical exchanges with suppliers to confirm the specific configuration and technical details of the equipment.
•
Contract signing: Sign a contract with the supplier to clarify the rights and obligations of both parties.
6. Production and manufacturing
•
Production preparation: The supplier prepares for production based on the confirmed plan, including raw material procurement, component processing, etc.
•
Assembly and debugging: After the equipment is assembled, preliminary debugging is carried out to ensure the normal operation of each component.
7. Installation and debugging
•
On site installation: Transport the equipment to your factory for on-site installation.
•
System debugging: Debugging the entire production system to ensure smooth operation of every link.
•
Performance testing: Conduct performance testing to ensure that the equipment achieves the expected production efficiency and product quality.
8. Training and Acceptance
•
Operation training: The supplier provides training to your operators to ensure they are proficient in operating the equipment.
•
Equipment acceptance: Conduct a comprehensive acceptance of the equipment to ensure that it meets the technical requirements and performance indicators stipulated in the contract.
9. Post service
•
Technical support: Suppliers provide necessary technical support to solve problems that arise during equipment operation.
•
Maintenance and upkeep: Regularly maintain and upkeep equipment to extend its service life.
Matters needing attention
•
Regulatory compliance: Ensure that the design and production of equipment comply with local food safety regulations and standards.
•
Environmental protection: Consider the environmental performance of equipment and reduce the discharge of wastewater and exhaust gas.
•
Safety measures: Ensure the safety performance of the equipment and prevent accidents during operation.