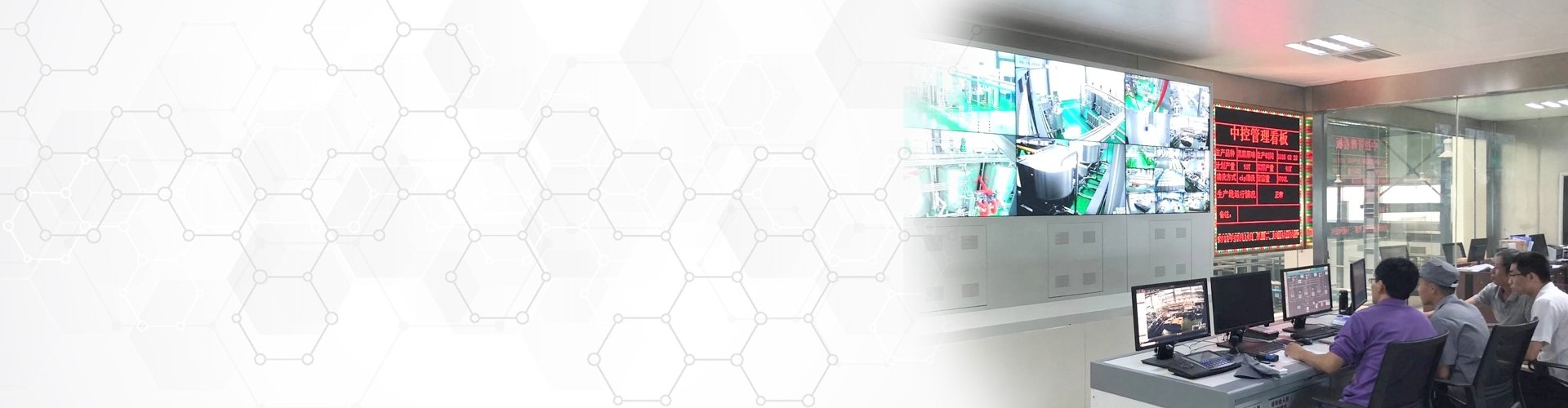
A plate pasteurizer with three sections is a type of food processing equipment used to heat and cool liquids, such as milk, juice, or soup, to kill harmful bacteria and extend the shelf life of the product.
The three sections of the plate pasteurizer typically consist of a preheating section, a heating section, and a cooling section. In the preheating section, the liquid is slowly heated to a set temperature to remove any initial cold spots and prepare it for the pasteurization process.
Next, the liquid enters the heating section, where it is rapidly heated to a specific temperature, usually around 71-74 degrees Celsius (160-165 degrees Fahrenheit), and held at that temperature for a predetermined amount of time, commonly 15-30 seconds. This high temperature kills bacteria, yeasts, and molds that may be present in the liquid, ensuring its safety for consumption.
After the heating section, the liquid moves into the cooling section, where it is rapidly cooled down to a lower temperature to prevent further bacterial growth. The specific cooling temperature and time depend on the type of liquid being processed.
Plate pasteurizers are designed with a series of plates stacked together, with alternating channels for the liquid and for hot/cold water to flow through. This design allows for efficient heat transfer between the liquid and the water, enabling rapid heating and cooling.
The plate pasteurizer with three sections is typically used in small to medium-scale food processing operations, such as dairy farms, juice producers, or soup manufacturers. It offers a cost-effective and energy-efficient method for pasteurizing liquids, ensuring product safety while maintaining the desired taste and quality.
Application:
The fully automatic flat plate pasteurization machine has demonstrated its important value in multiple industries. Here are several specific application cases:
In the dairy industry, these equipment are used to process milk and other dairy products. They are briefly heated at a temperature of 72 ° C to 75 ° C (for 15-20 seconds) to effectively kill bacteria while preserving nutrition and flavor. They are suitable for producing pasteurized milk, yogurt, cheese, etc.
This technology is widely used in the beverage manufacturing industry for sterilization of non-alcoholic beverages, such as carbonated drinks, tea drinks, and fruit juices.
Juice processing is particularly beneficial as it can be processed for a short period of time at 85 ° C to 90 ° C, maintaining the color, aroma, taste, and nutrition of the juice, ensuring safety, and extending shelf life. For juice processing of beverages containing fruit grains, the fully automatic flat plate pasteurizer can adjust parameters to protect the integrity of the fruit pulp while completing effective sterilization. Its automated cleaning function (CIP) maintains high hygiene standards for the production line.
These examples demonstrate how fully automatic flat plate pasteurizers can support the high standard production needs of the food and beverage industry with efficient and precise operation.
Technical:
Model |
Process capacity |
Heat exchanging area(m2) |
Power (kw) |
Steam cost (kg/h) |
External diamension (mm) |
Total weight of machine (kg) |
BR16-3-0.5 | 0.5 t/h | 5 | 5.2 | 52 | 1200×1200×1500 | 790 |
BR16-3-1 | 1 t/h | 8 | 5.2 | 60 | 1500×1500×1800 | 880 |
BR16-3-2 | 2 t/h | 13 | 6 | 104 | 1800×2000×1800 | 980 |
BR26-3-3 | 3 t/h | 20 | 6 | 156 | 2000×2000×2200 | 1080 |
BR26-3-4-5 | 4.5 t/h | 30-45 | 8 | 260 | 2250×2000×2200 | 1250 |
BR26-3-6-8 | 6-8 t/h | 35-50 | 8 | 400 | 2250×2000×2200 | 1250 |
BR26-3-10 | 10 t/h | 60 | 11 | 520 | 2800×2000×2200 | 1650 |
BR35-3-15 | 15t/h | 75 | 15 | 780 | 3000×2200×2200 | 2150 |
BR35-3-20 | 20t/h | 80 | 18 | 945 | 3300×2200×2200 | 2350 |
We can provide you with the following professional and detailed suggestions for customized solutions for pasteurization system products in milk production lines:
1. Key points of customized solutions for pasteurization system products:
According to the actual needs of the milk production line, a customized pasteurization system solution should include the following key points:
a. Equipment selection: Select pasteurization equipment that meets relevant standards and industry certifications, such as pasteurization machines, pasteurization tanks, etc. The equipment should have stable heating and cooling functions, precise temperature control system, and a complete operating interface and automation control system.
b. Sterilization process design: Based on product type and scale requirements, design a reasonable pasteurization process, including appropriate heating time, temperature curve, instantaneous cooling and other parameter settings. The process design should meet the sterilization requirements of milk and ensure the best product quality and taste.
c. Sterile filling system: equipped with a sterile filling system that meets hygiene requirements, ensuring that milk is sealed and packaged after sterilization to avoid secondary contamination.
d. Cleaning and disinfection system: Install a complete cleaning and disinfection system to regularly clean and disinfect the pasteurization equipment to ensure its hygiene and operational reliability.
e. Data monitoring and recording: It is recommended to install a data monitoring and recording system to monitor and record key data such as temperature, pressure, and time during the pasteurization process in real time, providing a basis for quality traceability and risk analysis in the later stage.
f. After sales service and training: Provide comprehensive after-sales service and operation training to ensure the normal operation of equipment and the technical mastery of operators.
2. Advantages of customized solutions:
Through customized pasteurization system product solutions, you can achieve the following advantages:
a. Product quality and safety: Customized solutions can ensure that the sterilization effect of milk meets relevant national standards according to your needs, ensuring product quality and safety.
b. Improving production efficiency: Reasonable selection and design of equipment, as well as optimized process flow, can improve production efficiency, reduce energy consumption and labor costs.
c. Comprehensive after-sales service: Reliable suppliers will provide comprehensive after-sales service and technical support, timely solve equipment operation problems, and reduce production line downtime.
d. Traceability and risk control: Through data monitoring and recording systems, quality traceability and risk control of the pasteurization process can be achieved, improving product reliability and credibility.
Fully automatic flat plate pasteurizers are often designed with environmental and energy-saving characteristics in mind to meet the requirements of modern production for sustainable development. The following points reflect its performance in these two aspects:
1. Energy efficiency optimization: Adopting advanced heat exchange technology, such as multi-layer flat plate design, can minimize heat loss and improve heat exchange efficiency to the greatest extent possible. Some high-end models are also equipped with a heat recovery system, which can recover the emitted heat energy for preheating the feed or other production processes, thereby significantly reducing energy consumption.
2. Precise temperature control: Through a precise temperature control system, it ensures that only necessary energy is used to reach the sterilization temperature, avoiding energy waste caused by excessive heating and maintaining product quality.
3. Water saving design: Integrated CIP (In Place Cleaning) system, optimized cleaning program and circulating water design, reducing water resource consumption. Intelligent cleaning technology can adjust the water and cleaning agent usage according to actual needs, achieving established hygiene standards while saving resources.
4. Environmentally friendly materials: Equipment manufacturing often uses corrosion-resistant and easily recyclable stainless steel materials to reduce the environmental impact during production and scrapping stages.
5. Modular construction: Modular design facilitates maintenance and upgrades, extends equipment lifespan, and reduces waste generated by frequent equipment replacement.
Regarding customized services for fully automatic tablet pasteurizers, different manufacturers can usually provide personalized design and manufacturing services based on specific customer needs. Customized content may cover the following aspects:
1. Capacity matching: Customize suitable processing capacity based on your production scale, from small-scale experimental models to large-scale industrial ones.
2. Material selection: Based on the characteristics of the processed material and hygiene standards, choose suitable contact materials, such as stainless steel 304 or 316L.
3. Control system: Customized HMI (Human Machine Interface) and PLC programming to achieve more intelligent automation control and monitoring functions.
4. Special functions: If it is necessary to adapt to the processing of specific products, such as materials with high viscosity and particulate matter, special structured heat exchange plates and pumping systems can be customized.
5. Space layout: Customize equipment size and shape based on the existing layout of the factory, and optimize the integration of the production line.
6. Additional features: such as automatic CIP system upgrade, energy recovery module integration, etc., to improve energy efficiency and operational convenience.
In summary, customized pasteurization system product solutions will provide safe, efficient, and reliable sterilization processes and equipment for milk production lines according to your needs, providing strong support for your product quality and business development.
The installation and commissioning of a fully automatic flat plate pasteurizer is a professional process that involves multiple steps to ensure proper operation and optimal performance of the equipment. Although I cannot personally guide the installation, I can outline the general installation and debugging process:
Preparation before installation
1. On site assessment: Confirm whether the space, water and electricity supply, drainage, and ground bearing conditions of the installation area meet the equipment requirements.
2. Technical exchange: Communicate in detail with the technical team of suppliers or manufacturers to understand the installation drawings, technical parameters, and special requirements of the equipment.
3. Infrastructure construction: Depending on the size and weight of the equipment, it may be necessary to pour concrete foundations in advance and ensure levelness.
Equipment installation
1. Positioning and fixing: According to the drawing instructions, place the sterilizer in the predetermined position and fix it with anchor bolts.
2. Pipeline connection: Connect the feed pipe, discharge pipe, steam pipe, condensate pipe, and CIP cleaning pipeline to ensure that all connections are sealed and leak free.
3. Electrical wiring: Professional electricians complete the wiring work of power supply, control panel, and sensors according to the electrical drawings.
Debugging phase
1. Single machine testing: Firstly, conduct a separate operation test of the equipment to check whether the motor, pump, valve, and heating and cooling system are working properly.
2. System integration testing: Connect the equipment to the entire production line, conduct linkage testing, and verify the coordinated operation of each link.
3. Temperature control calibration: Use a temperature calibrator to calibrate the temperature sensor of the heat exchange system to ensure temperature control accuracy.
4. Production test: Conduct sterilization tests using water or simulated materials, adjust sterilization time and temperature to achieve the predetermined sterilization effect.
5. Cleaning and disinfection: Conduct comprehensive CIP cleaning and disinfection after the first operation to ensure the hygiene and safety of the production environment.
Training and Acceptance
1. Operation training: Provide training to operators on equipment operation, daily maintenance, and troubleshooting.
2. Performance acceptance: Conduct final acceptance of equipment performance according to contract terms and standards.