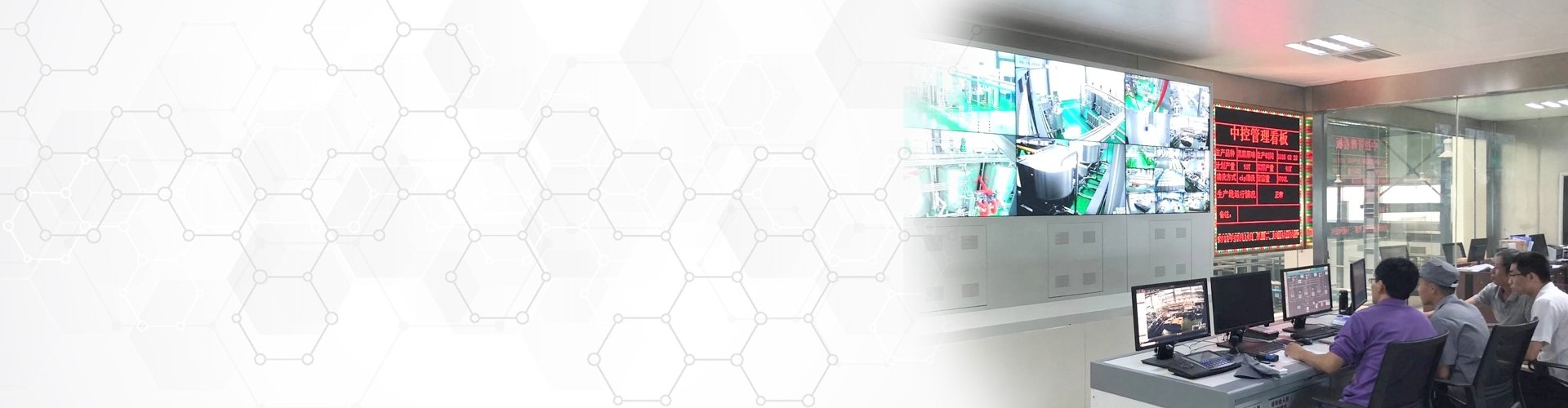
A milk cooling tank, also known as a bulk milk cooler or milk chilling unit, is a refrigerated storage system used to cool and store raw milk on dairy farms. It is an essential part of the milk collection and processing process, ensuring that milk is maintained at a safe temperature before it is transported to dairy processing plants.
Milk cooling tanks vary in size and capacity depending on the needs of the dairy farm. They are typically made of stainless steel for hygiene and durability. The tanks are insulated to maintain a consistent low temperature and are equipped with refrigeration units to cool the milk quickly after milking.
The milk cooling tank works by transferring heat from the milk to a refrigerant, which then cools the milk down to the desired temperature. The tank is designed with agitators or paddles to ensure proper mixing and prevent the formation of cream or separation of milk constituents.
Some milk cooling tanks also have automated features such as temperature monitoring and controls, automatic cleaning systems, and data recording for quality control purposes. These features help to maintain the quality and freshness of the milk, ensuring it meets industry standards and regulations.
Overall, milk cooling tanks play a crucial role in maintaining the quality and safety of raw milk on dairy farms. They help to prevent spoilage, bacterial growth, and degradation of milk components, allowing for the production of high-quality dairy products.
Refrigerated milk cooling tank
Vertical milk chill and storage tank(milk cooling tank, / chilling tank , milk storage tank, milk tank, refrigerator tank , refrigeration tank , refrigerated tank )
Product Description
- this vertical milk cooling tank(also called milk chiller, milk storage tank, stainless steel tank) is mainly used in cooling to storage milk or other liquid;
- It absorbs international advanced technology, adopts importing compress machine, safety and protection system, micro computer monitor, advanced technique and equipment such as polyurethane bubbling, honeycomb board evaporator. It is three layers with jacket layer and Pu insulation layer , outer and inner mirror polish to easy cleaning,and the cooling unit is use famous brand;
- Small land area than horizontal type; bulk milk cooling tank / milk chiller Generally speaking,it is an ideal cooling and storage equipment for pasture, milk station, milk factory, food factory, and beverage factory and pharmacy industry for keeping the milk raw milk in its best situation and prevents the bacteria.
Direct milk cooling tank is mainly used for cooling and storage for fresh milk, also can be used to cooling or storage for other liquid product. The cooling tank is the key equipment for the mechanical milking system in the dairy farms. Also widely used in the manual milking farm and milk collection centers, and milk production plants, which can keep the fresh milk at best state and prevent the bacterial growing.
Technical Parameter:
Model |
Volume(L) |
Rating power(kw) |
Refrigeration capacity(w) |
External size |
Total weight |
BZLG-500 |
500 |
3.6 |
7380 |
1750*1150*1300 |
242 |
BZLG -1 |
1000 |
4.4 |
9280 |
1950*1350*1450 |
285 |
BZLG -2 |
2000 |
6.7 |
15820 |
3950*1550*1750 |
460 |
BZLG -3 |
3000 |
9 |
19534 |
3500*1650*1850 |
645 |
BZLG -5 |
5000 |
13.6 |
31640 |
4000*2050*2150 |
1150 |
BZLG -8 |
8000 |
19.6 |
47460 |
4700*2300*2400 |
1450 |
Condition: New
Brand name: Shanghai Beyond;
Type: whole processing Line/turnkey project/fruit and vegetables processing/dairy processing/beverage processing
Voltage: 220v/380v
Power(W): 100-200kw
Weight: Different size different weight/customized
Dimension(L*W*H): Different size different dimension/customized
Certification: CE&ISO
Warranty: 12 months/1 year
After-sales Service Provided: Engineers available to service machinery overseas
Main material: SUS304 or SUS316
Control type: automatic, semi-automatic
Energy consumption: Low consumption with high efficiency
Capacity: 500-10000L/H-customized
Installation period: 1-3months
Period time: 30 days-120 days
Cups material: pouches, paper box, glass bottle, pet bottle, glass bottle
Product storage condition: room temperature; low temperature;
Milk Cooling Tank has a wide range of applications, mainly concentrated in the following fields:
1. Dairy farms: This is the most direct application scenario for milk cooling tanks. The fresh milk squeezed out from the farm needs to be quickly cooled to low temperatures to inhibit bacterial growth, maintain the freshness and nutritional value of the milk, until it is transported to the processing plant.
2. Small and family farms: For smaller farms or family businesses, milk cooling tanks are equally important to ensure that their products meet food safety standards and are easy to sell or process in the future. 3. Pre production link of dairy processing plants: In large dairy processing plants, milk cooling tanks serve as receiving stations to collect and temporarily store fresh milk transported from various places, waiting for further processing.
4. Mobile milking stations: In areas where it is inconvenient to build fixed refrigeration facilities, mobile milk cooling tanks can be used on-site to instantly cool milk and maintain its quality.
5. Laboratories and research institutions: During dairy quality analysis, new product development, or dairy science research, milk cooling tanks are used for temporary storage of samples to ensure the freshness of test materials and the accuracy of experimental results.
In summary, milk cooling tanks are an indispensable part of the dairy industry chain, ensuring that every step of milk production and processing maintains high quality standards.
The energy-saving and environmentally friendly characteristics of Milk Cooling Tank are mainly reflected in the following aspects:
1. Efficient refrigeration system: adopting energy-saving compressors and optimized refrigeration cycle design, reducing energy consumption while maintaining good cooling efficiency. Modern cooling tanks may also be equipped with variable frequency drives to automatically adjust the compressor speed according to the load, saving energy.
2. Insulation layer: High performance insulation materials are used on the outer wall of the tank to effectively reduce cooling loss, maintain a constant low temperature, and reduce energy consumption for continuous operation.
3. Intelligent temperature control technology: The integrated intelligent control system can accurately control the cooling temperature, avoiding energy waste caused by excessive cooling, and can adjust the working mode during non peak production hours through preset programs to save electricity.
4. Automatic defrosting function: Advanced defrosting technology can reduce energy consumption while ensuring efficiency, avoiding energy waste caused by traditional manual or timed defrosting.
5. CIP (In Place Cleaning) system: The efficient and water-saving CIP design can reduce water and heat consumption during the cleaning process, while ensuring hygiene standards.
6. Durable materials and long-life design: Choose corrosion-resistant and easy to maintain materials to reduce maintenance and replacement frequency, extend the overall service life of equipment, and be more environmentally friendly in the long run.
Customizing a Milk Cooling Tank is a process that involves specific needs assessment and design, primarily considering the following aspects to ensure that your equipment fully meets usage requirements:
1. Capacity requirement: Determine the appropriate volume of the cooling tank based on your milk production, which will directly affect storage capacity and operational efficiency.
2. Refrigeration efficiency: Choose a suitable refrigeration system based on the ambient temperature and the temperature requirements for the milk to quickly cool down, to ensure the quality of the milk.
3. Material and hygiene standards: Stainless steel is usually used to ensure compliance with international food safety standards, and is easy to clean and maintain.
4. Automation level: Whether automatic temperature control, cleaning system, and remote monitoring functions are needed to improve operational efficiency.
5. Installation space and layout: Customize the size and shape of the cooling tank according to the site conditions to ensure that it can seamlessly integrate into the existing production line or space.
6. Budget considerations: Clearly define the budget range so that the manufacturer can provide you with the most cost-effective solution.
The assembly and debugging process of Milk Cooling Tank roughly includes the following steps:
1. On site preparation: Ensure that the installation site is flat, sturdy, and has the necessary water and electricity connection conditions. According to the foundation diagram provided by the manufacturer, prepare the concrete foundation in advance.
2. Equipment positioning: Use a crane or other equipment to carefully place the cooling tank in the designated location, ensuring that the tank is stable and level.
3. Pipeline connection: Connect the milk inlet pipe, outlet pipe, refrigeration system pipeline, and possible CIP (cleaning in place) system correctly according to the drawing guidance. Use appropriate sealing materials to prevent leakage.
4. Electrical wiring: Professional electricians complete the power and control system wiring, including temperature sensors, controllers, and any automation equipment, according to the electrical schematic and wiring diagram.
5. Preliminary inspection: Before adding refrigerant or water, conduct a comprehensive system inspection to confirm that all connections are correct and the valve switch status is correct.
6. Adding medium: Add water to the tank for preliminary testing to check for any leakage points. Afterwards, add the appropriate refrigerant according to the manufacturer's instructions.
7. System debugging: Turn on the refrigeration system, set the target temperature through the control system, observe the temperature drop, and adjust until the expected refrigeration efficiency and stability are achieved.
8. Performance verification: After running the system for a period of time, verify whether the equipment meets the design requirements by detecting the actual cooling effect of the milk and all monitoring parameters.
9. Operation training: Manufacturers or installation teams should provide training to operators on system operation, daily maintenance, and emergency response.
10. Final acceptance: After all tests are correct, the final acceptance signature is carried out to ensure that the equipment can be officially put into use.