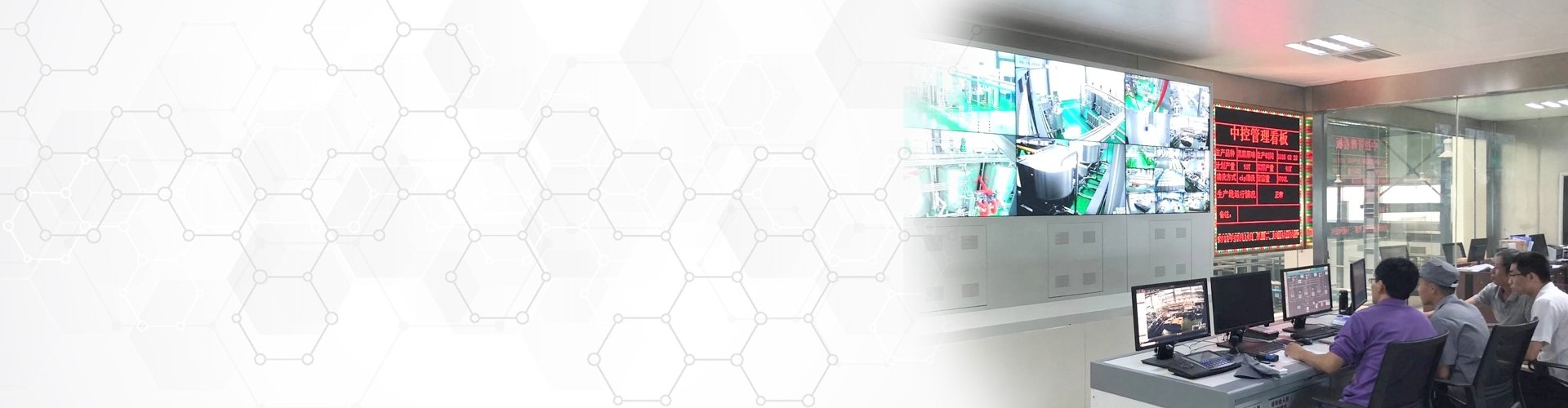
A milk jacket tank is a specific type of storage tank that is designed to store and transport milk or dairy products. These tanks are usually made of stainless steel, which is easy to clean and maintain the hygiene standards required for milk storage. The jacket tank design includes an inner tank where the milk is stored and an outer jacket that surrounds it. The jacket can be filled with chilled water or refrigerant to help maintain the desired temperature of the milk.
Milk jacket tanks are commonly used in dairy farms, milk processing plants, and transportation of bulk milk. They are equipped with various features such as agitators to prevent milk separation, temperature control systems, and outlets for easy filling and emptying. The jackets also provide insulation to keep the milk at the desired temperature during transportation. Overall, milk jacket tanks are essential for ensuring the safe and efficient storage and transport of milk and other dairy products.
Product overview
The insulation tank is designed according to the relevant hygienic standards and requirements of the food industry. The material is high-quality stainless steel SUS304. The tank body is mechanically polished with high finish; Fillet transition is adopted at the joints of head and nozzle, which is easy to clean and has no sanitary dead corner. It can be equipped with manhole, feed inlet, discharge outlet, cleaning port, etc. according to customer requirements.
Usage:for juice or milk or other liquid product blending,with paddel type agitator or propeller agitator, with accessories:
a) one air tight side manway;b) anti butterfly and dirt air vent;
c) One digital thermometer, temperature indication range 0~100℃;
d) CIP cleaning ball;
e) Discharge valve with union;
f) one sanitary sample valve;
g) product inlet/outlet
we can design according to customer's exact requirement
Model |
Diameter (L) |
Inner diameter (mm) |
Height (mm) |
Insulation mm |
Jacket mm |
Diameter of inlet/outlet |
BYJG-500 | 500 | 800 | 2140 | 50 | 1.5 | φ38 /φ51 |
BYJG-1 | 1000 | 1050 | 2380 | 50 | 1.5 | φ38 /φ51 |
BYJG-1.5 | 1500 | 1180 | 2550 | 50 | 1.5 | φ38 /φ51 |
BYJG-2 | 2000 | 1340 | 2760 | 50 | 1.5 | φ38 /φ51 |
BYJG-2.5 |
2500 |
1420 | 2940 | 50 | 1.5 | φ38 /φ51 |
BYJG-3 | 3000 | 1540 | 3050 | 50 | 1.5 | φ38 /φ51 |
BYJG-4 | 4000 | 1650 | 3200 | 50 | 1.5 | φ38 /φ51 |
BYJG-5 | 5000 | 1780 | 3250 | 50 | 1.5 | φ38 /φ51 |
BYJG-6 | 6000 | 1900 | 3350 | 50 | 1.5 | φ38 /φ51 |
BYJG-8 | 8000 | 2100 | 3800 | 60 | 1.5 | φ65 /φ51 |
BYJG-10 | 10000 | 2300 | 4050 | 60 | 1.5 | φ65 /φ51 |
BYJG-12 | 12000 | 2520 | 4450 | 60 | 1.5 | φ65 /φ51 |
BYJG-15 | 15000 | 2540 | 4700 | 60 | 1.5 | φ65 /φ51 |
Equipment transportation and hoisting
The equipment has been packed before leaving the factory. During transportation, it shall be placed according to the orientation indicated on the package. At the same time, when the equipment is transported far away, the mixing in the tank shall be fixed to avoid damage to the tank wall. During hoisting, it shall be hoisted according to the hoisting position indicated on the package.
Hoisting shall be carried out at the lifting lug of the upper head.
Equipment use and cleaning
1. Inspection before the equipment is in place. After the equipment arrives at the user, check whether the random parts are complete and whether the tank is transported Whether there is damage in the.
2 Inspection before equipment use
(1)After the equipment is in place, adjust the adjusting bolt at the support foot to keep the tank vertical and stable.
(2)For tanks with agitators, check whether the transmission machinery is installed correctly and firmly. Turn the mixer by hand and turn it freely before turning on the power supply.
(3) The rotation direction of the mixer shall be in accordance with the directions indicated in the attached drawings or the machine body.
3.Use and cleaning of equipment
(1) Clean water shall be used to flush out the residual materials in the equipment before or after the tank is used until there is no material in the outflow water.
(2) Heat 1-1.5% sodium hydroxide solution to 85 ℃ and circulate for 15 minutes, then rinse with clean water to flush out all the alkali liquor until the water is clear.
(3) Heat the acid solution with concentration less than 1% to 80-85 ℃ for 20 minutes, and then clean it with clean water at about 90 ℃; Then use sterile normal temperature water for cooling, or self cooling.