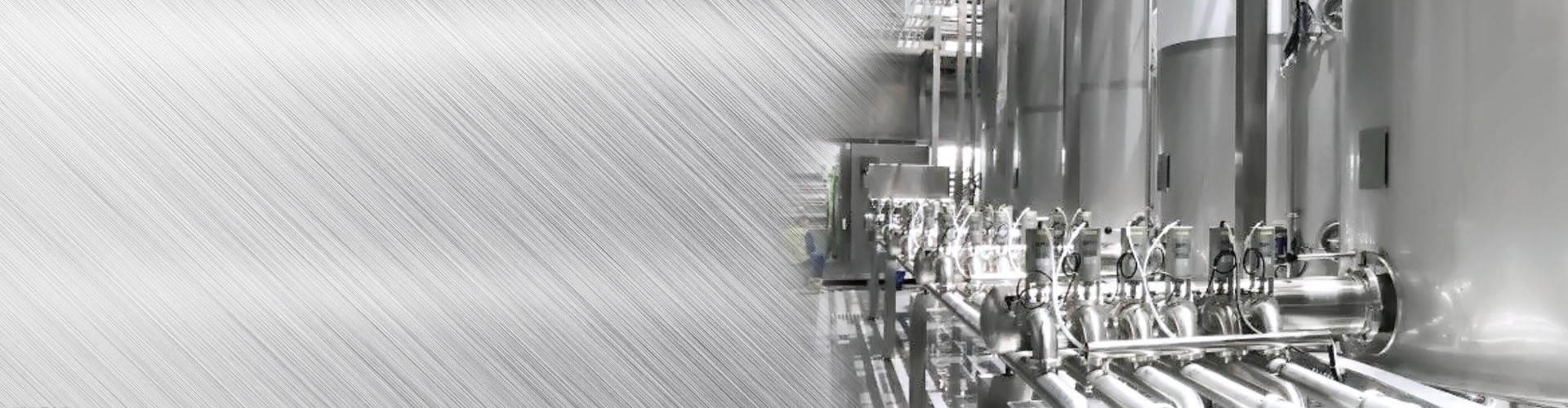
In the dynamic landscape of the dairy industry, the production of milk powder has emerged as a cornerstone for meeting global demands for shelf-stable dairy products. Milk powder factories, also known as milk powder plants or processing plants, play a pivotal role in transforming fresh milk into a versatile, long-lasting powder that can be easily transported and stored. This article delves into the intricacies of milk powder processing plants, highlighting their significance, technological advancements, and the future trajectory of this essential industry.
Milk powder processing plants are integral to the dairy sector, offering a solution to the challenges of milk preservation and distribution. By converting liquid milk into a powdered form, these facilities extend the product's shelf life, making it accessible to consumers in regions where fresh milk supply is limited. Moreover, milk powder serves as a fundamental ingredient in a myriad of food products, from infant formulas and nutritional supplements to baked goods and confectionery.
The evolution of milk powder processing plants is marked by significant technological strides aimed at enhancing efficiency, quality, and sustainability. Modern plants are equipped with state-of-the-art machinery that facilitates the entire production process, from raw milk reception to the final packaging of milk powder.
5. Cooling and Packaging: The dried powder is cooled to room temperature and screened to remove any large particles. The final product is then packaged into various formats, such as plastic bags, paper boxes, or metal cans, ready for distribution.
As the global demand for milk powder continues to rise, milk powder processing plants are poised to embrace further innovation. The focus on sustainability is driving the adoption of energy-efficient technologies and eco-friendly practices. Automation and digitalization are enhancing production efficiency, while stringent quality control measures ensure that every batch of milk powder meets the highest standards of safety and nutrition.
In conclusion, milk powder processing plants are at the forefront of the dairy industry's efforts to meet consumer needs and environmental challenges. By leveraging advanced technology and adhering to stringent quality standards, these facilities are ensuring that milk powder remains a vital and versatile component of the global food supply.
Shanghai Beyond Machinery Co., Ltd.
Beyond Machinery specializes in the design and manufacturing of Milk powder processing plant equipment.Please contact us now, and our professional technical engineers will customize the equipment plan for Milk powder plant and provide a quotation.Please contact us now to obtain the latest equipment plan and quotation.