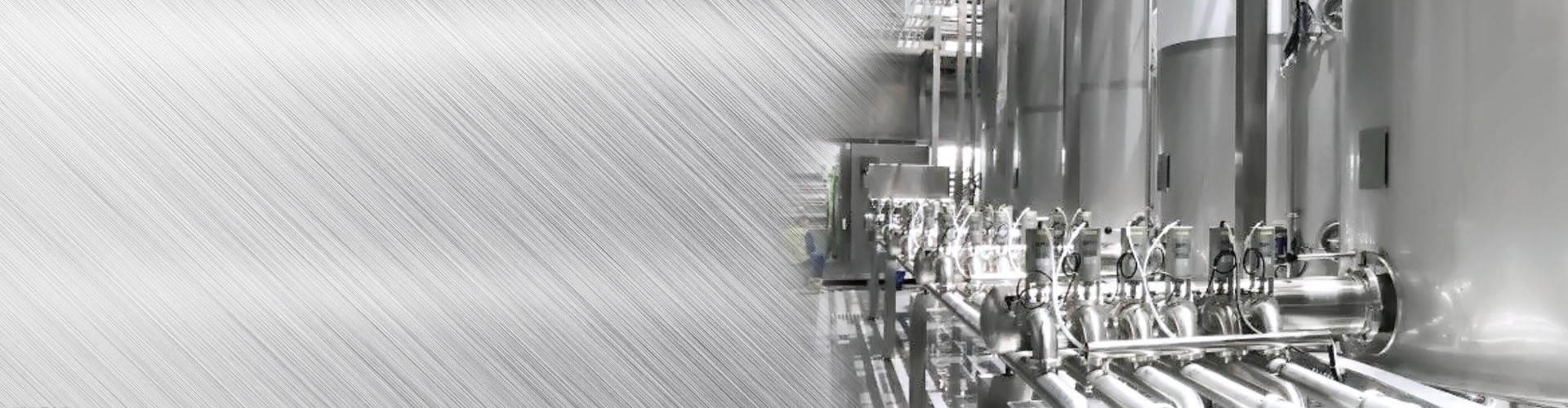
The biopharmaceutical fermentation tank is an indispensable key equipment in the biopharmaceutical industry, mainly used for microbial or cell culture to produce biological products such as vaccines, antibodies, enzymes, bioactive substances, etc. This type of equipment is designed with precision and can provide a strictly controlled environment to optimize the fermentation process.
1. Design and structure: Fermentation tanks are usually made of stainless steel material, ensuring sterility and corrosion resistance. Milo plates or labyrinth jackets are often installed on the tank body, allowing heating or cooling media to circulate through, thereby achieving precise temperature control. This is crucial for the growth of aerobic and anaerobic microorganisms.
2. Specifications and application scope: The capacity of fermentation tanks is diverse, ranging from small laboratory fermentation tanks of 300 liters to industrial production fermentation tanks of 15000 liters or even larger, to meet the production needs of different scales. They are widely used in dairy products, beverages, and a wider range of biotechnology fields.
3. Control System: Modern fermentation tanks are equipped with advanced control systems for monitoring and adjusting thermal and biochemical parameters, such as temperature PH value, dissolved oxygen level, stirring speed, etc. ensure efficient and stable fermentation process. These systems help maintain ideal microbial growth conditions, improve product yield and quality.
4. Flexibility of operation: The fermentation tank can be divided into aerobic and anaerobic types according to the characteristics of the cultivated microorganisms, and has the function of air sterilization (i.e. empty tank sterilization) to ensure sterility before each use. During non use, it is necessary to drain the remaining water in the tank and pipeline to prevent pollution.
As one of the key equipment in the biotechnology industry, the biopharmaceutical fermentation tank integrates multiple advanced technologies to ensure efficient, safe, and controllable fermentation processes.
Here are some technical highlights:
1. Precision control and automation: Modern biopharmaceutical fermentation tanks are equipped with advanced control systems, such as PLC (Programmable Logic Controller) and DCS (Distributed Control System), which can accurately control the temperature during the fermentation process Key parameters such as pH value, dissolved oxygen (DO), stirring rate, pressure, etc. These systems can automatically adjust to ensure optimal fermentation conditions, improve product quality and yield.
2. Efficient heat exchange system: Fermentation tanks are usually designed with a Milo plate or labyrinth jacket structure, which can efficiently heat or cool, ensuring stable temperature control. This design allows the medium to circulate within the jacket, reducing energy consumption while improving reaction efficiency.
3. Aseptic operation and pollution prevention design: In order to avoid bacterial contamination, the fermentation tank adopts a strict aseptic design concept, including CIP (on-site cleaning) and SIP (on-site sterilization) systems, as well as advanced filtration and sealing technology, effectively preventing external pollutants from entering and ensuring the purity of the fermentation process.
4. Materials and Corrosion Resistance: The main materials of the fermentation tank are mostly made of high-quality stainless steel such as 304, 1cr18Ni9Ti, etc. These materials not only have strong corrosion resistance but also comply with GMP (Good Manufacturing Practice) standards, ensuring product safety and long-term stability of the equipment.
5. Modularization and flexibility: Many fermentation tanks are designed with a modular structure, which can quickly adjust capacity and configuration according to production needs, adapting to different stages from small-scale laboratory research to large-scale industrial production.
6. Energy conservation and emission reduction: Modern fermentation tank design focuses on energy efficiency, using energy-saving mixing systems and heat exchange technology to reduce energy consumption, while reducing production costs and environmental impact.
7. Online monitoring and data analysis: The integrated sensors and data collection system can monitor various indicators during the fermentation process in real time. Combined with bioinformatics analysis, it achieves refined management of the fermentation process and timely adjusts strategies to respond to abnormal situations.
8. Compatibility and Scalability: In order to adapt to the rapid development of the biopharmaceutical industry, the design of fermentation tanks considers compatibility with other biological manufacturing equipment and downstream processing systems, facilitating technological upgrades and process optimization.
These technological highlights have jointly driven the biopharmaceutical industry towards a more efficient, environmentally friendly, and intelligent direction.
Installation and commissioning of biopharmaceutical fermentation tanks
The installation and debugging of biopharmaceutical fermentation tanks are important steps to ensure their normal operation and achieve expected production goals, mainly including the following steps:
1. Location selection and size confirmation: Firstly, select a suitable installation location and determine its size based on the specifications and terrain conditions of the fermentation tank. This step requires consideration of the convenience of equipment feeding and discharging, maintenance space, and coordinated layout with other production equipment.
2. Basic construction: Prepare basic materials such as concrete or bricks according to the design drawings for basic construction. The foundation must be able to withstand the weight of the fermentation tank when fully loaded and the dynamic load generated during operation, ensuring stability and non tilting.
3. Tank installation: Place the fermentation tank on a prepared foundation and securely secure the tank with bolts. This step requires ensuring that the tank body is level to avoid problems caused by imbalance during subsequent operation.
4. Pipeline and system connection: connect the inlet and outlet of the fermentation tank, ventilation system, and possible sterile air supply system. All connecting parts must be sealed to prevent leakage, and pressure testing should be conducted to check for any air leakage.
5. Electrical and control system installation: Install electrical control components such as motors, controllers, and instruments, and complete the laying of electrical circuits. Conduct preliminary system debugging, including sensor calibration, program settings, etc., to ensure that the control system can accurately monitor and regulate the fermentation process.
6. Inspection and debugging: After all hardware installations are completed, conduct a comprehensive equipment inspection and confirm that there are no errors before starting debugging. This includes single machine trial operation, linkage trial operation, and testing under simulated fermentation conditions to ensure smooth operation of all systems, with various parameters such as temperature Control the pH value, dissolved oxygen, etc. within the predetermined range.
7. Sterility verification and cleaning: Before formal use, sterility verification is also required to ensure that the entire system is in a sterile state. At the same time, develop and implement CIP and SIP procedures to verify the effectiveness of cleaning and sterilization, and prepare for production.
8. Personnel training: Operators need to receive professional training to understand the operation process, maintenance points, and emergency measures of the fermentation tank, to ensure safe and efficient use of equipment.
During the installation and debugging process, strict adherence to the installation guidelines provided by the manufacturer and relevant national safety regulations should be followed. If necessary, professional technical personnel should be invited to provide guidance to ensure the safe and stable operation of the fermentation tank.
Shanghai Beyond Machinery Co., Ltd.
Beyond Machinery specializes in the design and manufacturing of biopharmaceutical fermentation tank.Please contact us now, and our professional technical engineers will customize the equipment plan for biopharmaceutical fermentation tank and provide a quotation. Please contact us now to obtain the latest equipment plan and quotation.