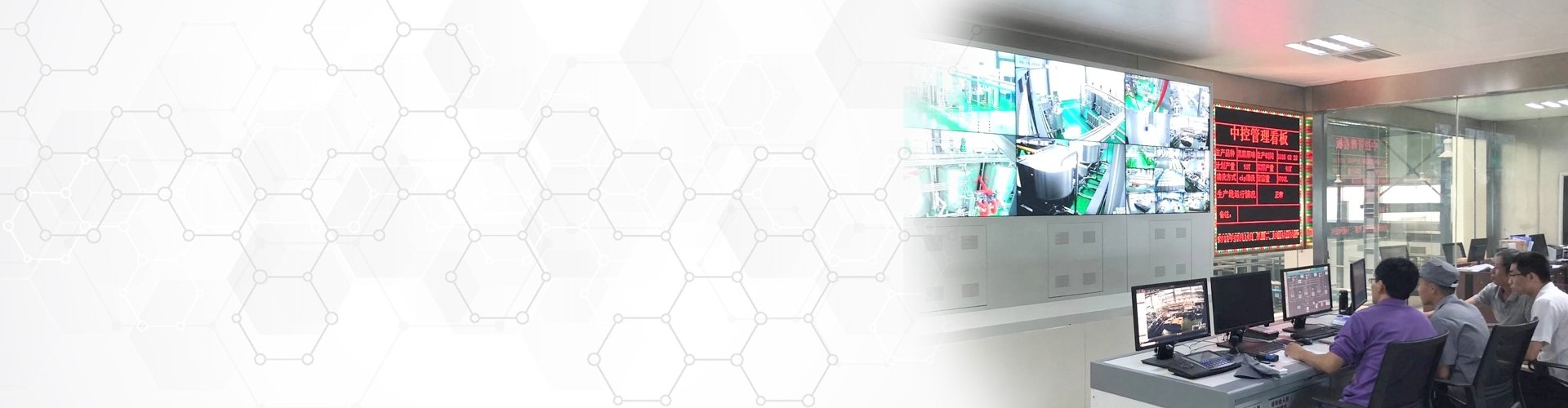
The triple effect falling film evaporator is an efficient liquid evaporation and concentration device, which works based on the principles of evaporation and heat recovery. It mainly includes the following steps:
1. Heating and evaporation: The raw material liquid is evenly distributed from the top of the evaporator to the outer wall of the heating tube, forming a thin film. As the heat source (usually steam) transfers heat through the inner wall of the heating tube, the thin film like liquid is quickly heated to the boiling point, producing a large number of steam bubbles. This is a fast heat transfer process.
2. Multi stage evaporation: "Three effects" means that the system consists of three evaporators connected in series. The secondary steam generated in the primary evaporator (first effect) is used as the heat source for the next evaporator (second effect), and the steam generated in the second effect is supplied to the third effect. This step-by-step utilization of the latent heat of steam achieves efficient recovery and utilization of thermal energy.
3. Condensation recovery: The steam generated by each stage of evaporation is condensed back into its own condenser, and this condensed water can be recycled and reused as needed to reduce water resource consumption.
4. Vacuum operation: The entire evaporation process is usually carried out in a vacuum state, which can lower the boiling point of the material, save energy, and prevent thermal decomposition of thermosensitive materials.
5. Continuous operation: The three effect falling film evaporator is designed for continuous feeding and discharging, suitable for large-scale continuous production and improving production efficiency.
The technical highlights of the triple effect falling film evaporator mainly focus on the following aspects:
1. High efficiency and energy saving: Through three-stage evaporation series, the latent heat of steam is maximally utilized, significantly improving the utilization rate of heat energy and significantly reducing energy consumption compared to single effect evaporation.
2. Fast evaporation speed and high heat transfer efficiency: The falling film evaporation method forms an extremely thin liquid film on the heating wall, increasing the heat transfer area, accelerating the evaporation rate, and ensuring high heat transfer efficiency.
3. Strong adaptability and large processing capacity: Suitable for handling materials with heat sensitivity, high viscosity, and easy crystallization. The continuous operation mode is suitable for large-scale production needs and has strong processing capacity.
4. Automated control, easy to operate: Equipped with a modern automatic control system, it can accurately control various parameters of the evaporation process, reduce manual intervention, and improve production safety and stability.
5. Compact structure and small footprint: Compared with traditional evaporation devices, the integrated design of the three effect falling film evaporator greatly saves space and is more suitable for the layout needs of modern factories.
6. Easy to clean and maintain: Modular design makes equipment cleaning and maintenance more convenient, ensuring hygiene standards in the production process and extending equipment lifespan.
7. Environmentally friendly: While reducing steam consumption, the amount of cooling water used is also reduced, and the evaporation process is carried out in a closed manner, reducing environmental pollution and meeting the requirements of green production.
These technological advantages make the triple effect falling film evaporator an ideal choice for efficient and environmentally friendly concentration treatment in many industries.
Due to the characteristics of thin film flow, the sensitivity of falling film evaporators to scaling and pollutants is relatively low.
Application
The triple effect falling film evaporator has been widely used in multiple industries due to its efficient evaporation capacity and good energy-saving characteristics. Here are some typical application cases:
1. Food industry: In the concentration process of fruit juice, milk, seasonings, etc., the triple effect falling film evaporator can effectively retain the color, aroma, and taste of the original product, while significantly reducing moisture, improving product concentration and shelf life.
2. Pharmaceutical industry: used for the concentration of traditional Chinese medicine extracts, antibiotic solutions, etc., to ensure that the active ingredients of the drugs are not destroyed, meet GMP standards, and ensure the hygiene and safety of the production process.
3. Chemical industry: In the process of organic solvent recovery, wastewater treatment, and purification of chemical products, the three effect evaporator can effectively separate and concentrate useful components, reduce waste emissions, and optimize production costs.
4. Textile printing and dyeing: Treating printing and dyeing wastewater, recycling dyes and water, reducing environmental pollution, while saving water resources and dyeing material costs.
5. Dairy processing: whey protein concentration, lactose dehydration, etc., to increase product added value, reduce waste emissions, and optimize the sustainability of production processes.
6. Starch sugar alcohol production: In the production process of sugar alcohols such as corn starch and malt syrup, a three effect evaporator is used to increase sugar concentration, reduce subsequent crystallization energy consumption, and improve overall production efficiency. To provide more specific case details, I will search for some successful stories or project overviews in practical applications.
These cases demonstrate the widespread application and effectiveness of triple effect falling film evaporators in improving production efficiency, resource recovery, and environmental protection.
Designed parameter
Machine type | Three-stage falling film downstream evaporator |
Steam consumption: | ~1600kg/h;0.1~0.3Mpa; |
Evaporating capacity | 4T/h, material inlet: 5t/h; |
Cooling water consumption | ~96t/h,inlet30°C,outlet38°C |
First stage evaporating temperature | 72~82℃ (-0.071~-0.051) |
Second stage evaporating temperature | 60~70℃(-0.080~-0.069) |
Third stage evaporating temperature | 45~55℃(-0.09~0.085) |
Total rated power | ~28KW |
3. Energy conservation and environmental protection
The performance of the triple effect falling film evaporator in energy conservation and environmental protection is mainly due to several key features of its design and operating mechanism:
1. Multi stage evaporation and heat recovery: The three effect evaporator operates at a lower temperature through three series connected evaporation chambers, using the secondary steam from the previous stage as the heat source for the subsequent stage. This design minimizes the demand for external steam to the greatest extent possible, thereby significantly reducing energy consumption.
2. Efficient heat transfer and falling film technology: During the falling film evaporation process, the material liquid forms a thin film on the surface of the heating tube for rapid evaporation, reducing thermal resistance and improving heat exchange efficiency. This not only accelerates the evaporation process, but also reduces energy waste caused by heat loss.
3. Closed loop and emission reduction: The system is usually designed as a closed loop to reduce the direct discharge of steam and condensed water. At the same time, the condensed water can be recycled, reducing the consumption of fresh water resources and also helping to reduce thermal pollution.
4. Adaptive heat source: The three effect evaporator can flexibly adapt to various heat sources, including waste heat, waste heat, etc., further improving the flexibility and efficiency of energy use and reducing dependence on traditional high carbon energy.
5. Intelligent control and optimization: The integrated automation control system can monitor the evaporation process in real time, optimize operating parameters, avoid overheating or insufficient heating, and ensure that the system always operates in the most energy-efficient state.
6. Material and structural optimization: Efficient insulation materials are used to reduce heat loss, and structural optimization is used to reduce resistance and improve the overall energy efficiency of the system.
Through the application of these designs and technologies, the three effect falling film evaporator effectively reduces energy consumption and environmental impact while meeting production needs, meeting the requirements of modern industry for sustainability and environmental protection.
4. Performance characteristics
1. Steam heating is uniform, with high heat transfer efficiency and short heating time;
2. Waste heat can be fully used as a heat source to reduce the amount of raw steam;
3. The materials are evenly distributed in the heating tubes of the evaporator through the distribution device. Under the induction of gravity and vacuum and the action of air flow, the materials form a film and flow from top to bottom. During the movement, they exchange heat with the heating steam on the outer wall of the heating tube and evaporate;
4. The evaporation process is in a vacuum environment, the evaporation temperature is relatively low, and the evaporator is not easy to scale;
5. It is applicable to the evaporation and concentration of foaming materials. As the material liquid evaporates in a film form in the heating tube, that is, vapor-liquid separation is formed. At the same time, at the bottom of the effect, most of the material liquid is pumped away, and only a small part of the material liquid and all the secondary steam enter the separator to strengthen the separation. The whole process of the material liquid does not form too much impact, avoiding the formation of foam;
6. For the evaporation and concentration of fruit juice or dairy products, the equipment can also have the sterilization function. The materials are preheated first, and then enter the sterilizer, which can reach 90-125 degrees, and maintain for about 30-60 seconds, that is, enter the effect body. The materials flash rapidly, and the temperature drops instantly;
7. This equipment can be equipped with CIP cleaning system to realize on-site cleaning. The whole set of equipment is easy to operate without dead corners;
8. It can be equipped with steam jet pump to reduce steam consumption and save operation cost;
9. Continuous feeding and discharging of the equipment;
10. This equipment can be configured with an automatic control system with complete configuration, operation, monitoring and control functions. The system includes communication interface, display alarm, print report, control and other parts to realize automatic control of feeding volume, heating temperature, discharge concentration and cleaning.
Equipment configuration list
NO. | Name | Spec | Qty | Unit | Remarks |
1 | First stage evaporator | 57m2 | 1 | piece |
Material: SUS304, tubular type; with material distributing device;shell diameterΦ442,thickness:3mm, |
2 | Second stage evaporator | 73m2 | 1 | piece |
Material: SUS304, tubular type; with material distributing device;shell diameterΦ546,thickness:3mm, |
3 | Third stage evaporator | 86.6m2 | 1 | piece |
Material: SUS304, tubular type; with material distributing device;shell diameterΦ622,thickness:3mm, |
4 | First stage separator | Φ800X1600X4 | 1 | piece | Tangent intubation are connected to the evaporator; with sight glasses and cleaning nozzle; The steam-liquid separation; 304 shell material, oval head |
5 | Second stage separator | Φ800X1600X4 | 1 | piece | Tangent intubation are connected to the evaporator; with sight glasses and cleaning nozzle; The steam-liquid separation; 304 shell material, oval head |
6 | Third stage separator | Φ1000X2000X4 | 1 | piece | Tangent intubation are connected to the evaporator; with sight glasses and cleaning nozzle; The steam-liquid separation; 304 shell material, oval head |
7 | Condensor | 83m2 | 1 | piece |
Material: SUS304, tubular type; with material distributing device;shell diameterΦ548,thickness:4mm, |
8 | Valve pipe fittings |
|
1 | set | The connection tubes between the evaporator system, the material 304, excluding raw steam pipes, cooling water pipes, process water pipe and outer pipe system |
9 | Electric instrument |
|
1 | set |
Including thecontrol cabinet, thermometer, pressuregauge, system cable, flowmeter etc. |
10 | Platform |
|
1 | set | Carbonated steel |
6. Working process:
The primary steam firstly enters into the first stage heating chamber to heat the materials, and in the vacuum condition, injects into first stage evaporating chamber through tubes, the materials return back to heating room through curve, and are heated again then injected to evaporating section, and form the circular. When the material liquid is sprayed into the evaporation chamber and nebulized, moisture is quickly evaporated, and the evaporated second steam enters to the second stage heating chamber to heat the material, and in the vacuum condition, injects into second stage evaporating chamber through tubes, the materials return back to heating room through curve, and are heated once more then injected to evaporating section, and form the circular. Then the material liquid is sprayed into the evaporation chamber and nebulized, moisture is quickly evaporated, and the evaporated third steam enters to the third stage heating chamber to heat the material and finally the steam goes into the condensor, and cooled by tap water into condensate water, and discharged tilll it reaches hlaf of the sight glass.
The moisture in the liquid material is continiously evaporated and concentration is increased to the expected rate and discharged from outlet.
The cooling water temperature will be increased to 30 -40 degree after the condenser exchanging, and sent to the water resource for whole plant usage or cooling tower recycling .
Process Flow
7. Assembly and Debugging
The assembly and debugging of the triple effect falling film evaporator are important steps to ensure the efficient and stable operation of the equipment. The specific steps are as follows:
1. Assembly preparation: • Confirm that all components and accessories have arrived on site and completed quality inspection Prepare the necessary tools and lifting equipment for assembly Ensure that the assembly area is clean and meets installation requirements.
2. Basic inspection and positioning: • Check whether the foundations of each evaporator unit and auxiliary equipment meet the requirements of the installation drawings Use cranes and other equipment to accurately position the evaporator body, heater, condenser, and other components.
3. Pipeline connection: According to the design drawings, connect the steam, material, condensate, and drainage pipelines between the evaporators to ensure that all connections are sealed and leak free Install and adjust various valves, such as inlet and outlet valves, steam valves, condensate discharge valves, etc.
4. Electrical and instrumentation installation: Install motors, control system cabinets, temperature and pressure sensors, and other instruments Wiring and pre debugging according to control logic, including PLC programming and verification.
5. Vacuum system assembly: Install vacuum pumps and corresponding pipelines to ensure that the entire system can achieve the required vacuum degree as designed.
6. Single machine test run: Conduct separate test runs on each evaporator unit and its auxiliary equipment to check whether the motor direction, pump head, heating efficiency, etc. meet the standards.
7. System debugging: • Turn on steam supply, gradually heat the first stage evaporator, observe steam flow, material evaporation, and the operation status of the second and third stage evaporators Adjust the pressure balance and material flow between each effect to ensure effective heat transfer and achieve the expected evaporation efficiency.
8. Performance testing: Conduct full load operation testing to evaluate key indicators such as evaporation rate, energy consumption, and product quality Fine tune system parameters based on test results until optimal performance is achieved.
9. Cleaning and disinfection: Before formal use, the system should be thoroughly cleaned and disinfected to ensure compliance with production hygiene standards.
10. Operation and maintenance training: Provide detailed operation manuals and maintenance guidelines for operators Conduct on-site operation training to ensure that the team is proficient in daily operations and basic troubleshooting skills.
11. Final acceptance: Organize project acceptance and submit relevant documents, including installation and commissioning reports, performance testing reports, etc Ensure that all debugging work complies with safety, environmental protection, and industry standards.
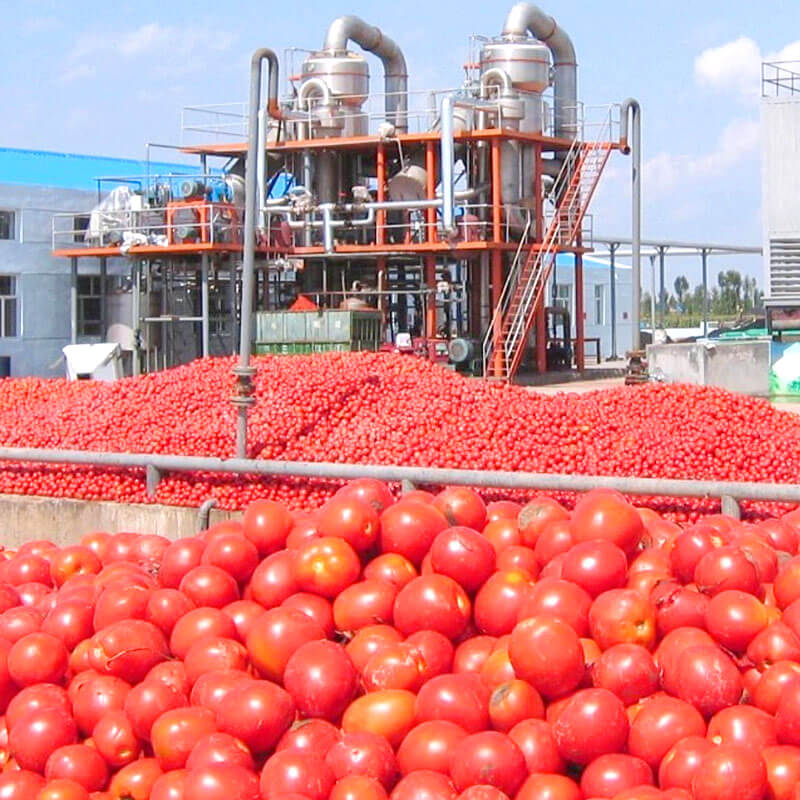
Model | BYJM-3-3 | BYJM-3-5 | BYJM-3-10 | BYJM-3-20 | BYJM-3-30 | BYJM-3-50 | |
Water evaporation(kg/hr) | 3000 | 5000 | 10000 | 20000 | 30000 | 50000 | |
Steam consumption(t/hr) | 0.9-1.2 | 1.5-2 | 3-4 | 6-8 | 9-12 | 15-20 | |
Steam pressure(Mpa Absolute pressure) | 0.4-0.8 | ||||||
Water evaporation(tons)/1ton steam | 2.5-3.33 | ||||||
vacuum degree | 1 effect(MPa) | -0.01-0.18 | |||||
3 effect(MPa) | -0.085 | ||||||
Evaporation temperature | 1 effect(MPa) | 70-115 | |||||
3 effect(MPa) | 45-55 | ||||||
External dimension(LxWxH) | 5x2.8x10 | 6x3.5x11 | 7.2x4.1x11.3 | 9x5x14 | 11x6x14 | 12.5x7.6x14 |
8. Customized triple effect falling film evaporator
Customizing a three effect falling film evaporator requires careful planning to meet specific production needs and operating conditions. The following are the key steps and considerations involved in the customization process:
1. Requirement analysis: Firstly, we will have in-depth communication with you to understand your specific requirements, including the properties of the processed materials (such as viscosity, thermal sensitivity, crystallinity), expected processing capacity, product concentration requirements, available energy types, and environmental protection requirements.
2. Process design: Based on requirement analysis, our engineering team will design a suitable evaporation process and determine the evaporation parameters of each stage of the three effect evaporator, such as temperature difference, vacuum degree, etc., to ensure efficient and stable operation.
3. Equipment selection and customization: • Heating area and tube bundle design: Customize the size, material (such as stainless steel, titanium), and arrangement of heating tubes based on evaporation capacity and material characteristics to optimize heat transfer efficiency Automation control system: Design a PLC or DCS system that meets your control needs, achieving precise control of key parameters such as temperature, flow rate, and liquid level Material selection: Choose appropriate contact materials based on the corrosiveness of different materials to ensure the durability of the equipment Energy saving plan: Explore the possibility of adopting energy-saving technologies and equipment, such as multi-stage flash evaporation and heat pump system integration, to further improve energy efficiency.
4. 3D design and confirmation: Provide 3D design drawings for your review, visually display equipment layout and structural details, and ensure that the design meets on-site installation conditions.
5. Manufacturing and Quality Control: After confirming your plan, we will begin customized production and implement strict quality control throughout the process to ensure that every step meets design standards and industry norms.
6. On site installation guidance and debugging: Dispatch a professional technical team to the site to guide the installation and conduct system debugging to ensure the smooth operation of the equipment.
7. Training and after-sales service: Provide professional training for operators and long-term after-sales technical support to ensure that your team can effectively manage and maintain equipment.
If you have a need for customized triple effect falling film evaporators, please provide more specific information so that we can provide you with more accurate customized solutions and services.