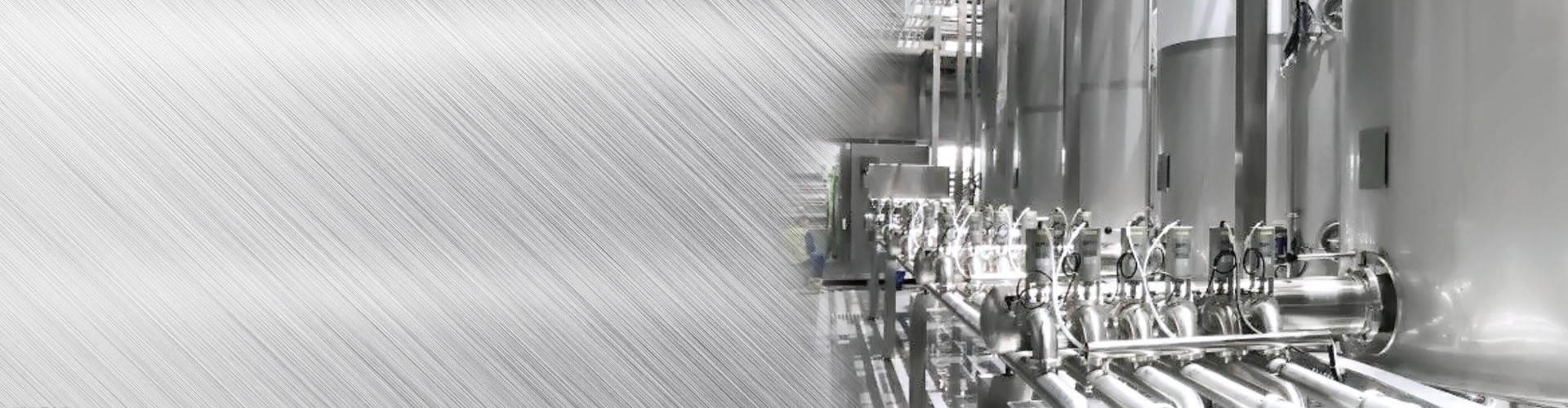
The plum jam production line is an automated equipment system specifically designed for producing plum jam. This production line covers multiple key steps from raw material processing to final product packaging, including raw material receiving, cleaning, de nucleating, shredding, preheating, pulping, concentration, sterilization, cooling, filling, sealing, labeling, and boxing. By adopting advanced automation control, efficient raw material processing, vacuum concentration, continuous sterilization, and intelligent packaging technology, the production line can ensure the quality, safety, and consistency of jam. At the same time, the production line also pays attention to energy utilization and environmental protection, achieving sustainable production through measures such as waste heat recovery, wastewater treatment, and green packaging.
The use of advanced technology and equipment in the design and implementation of plum jam production lines can significantly improve production efficiency, product quality, and safety. Here are some key technological highlights:
1. High degree of automation
•
Automated control system: PLC (programmable logic controller) and SCADA (data acquisition and monitoring control system) are used to achieve automated control of the production line, reducing manual intervention and improving production efficiency and stability.
•
Robot technology: Introducing robots in the packaging and boxing process to improve work efficiency and reduce labor intensity.
2. Efficient raw material processing
•
Multi level cleaning system: using a combination of bubble cleaning machine and spray cleaning machine to effectively remove soil and impurities on the surface of plums, ensuring the cleanliness of raw materials.
•
Efficient Core Removal Machine: Using advanced core removal machines, plum pits can be quickly and accurately removed, reducing raw material loss.
3. Advanced processing technology
•
Preheating and pulping: Use a steam preheater to preheat plums, making them easier to mash. An efficient blender can grind plums into a delicate pulp, enhancing the taste of jam.
•
Vacuum concentration: Using a vacuum evaporator for concentration, jam can be quickly concentrated at lower temperatures, retaining more natural flavors and nutrients.
•
Continuous sterilization: Using a continuous sterilization line, jam is subjected to high-temperature instantaneous sterilization to ensure food safety while reducing the impact on jam flavor.
4. Intelligent packaging and inspection
•
Automatic filling machine: Using high-precision automatic filling machines to ensure consistent capacity of each jam bottle and improve packaging quality.
•
Sealing and labeling: Using a screw cap sealing machine and a heat sealing machine to ensure the sealing of the packaging. Automatic labeling machines can quickly and accurately apply labels, improving production efficiency.
•
Online detection: Set up weight detection, metal detection and other online detection equipment on the packaging line to ensure the quality and safety of each product.
5. Environmental protection and energy conservation
•
Wastewater treatment: equipped with a wastewater treatment system to treat the wastewater generated during the production process, discharge it in compliance with standards, and reduce environmental pollution.
•
Energy recovery: Waste heat recovery technology is adopted in the preheating and concentration stages to improve energy utilization efficiency and reduce production costs.
6. Data management and traceability
•
Production data management: MES (Manufacturing Execution System) is used to collect and manage real-time data during the production process, achieving transparency and traceability of the production process.
•
Product quality traceability: Through barcode or QR code technology, each batch of products is identified to achieve full traceability from raw materials to finished products, ensuring product quality.
7. Safety and hygiene
•
Sanitary design: The equipment on the production line is made of stainless steel material, with a simple design that is easy to clean and disinfect, and meets GMP (Good Manufacturing Practice) requirements.
•
Safety protection: Install safety protection devices at critical locations, such as emergency stop buttons, safety doors, etc., to ensure the safety of operators.
8. Flexible production
•
Modular design: The production line adopts modular design, which can flexibly adjust equipment configuration according to different production needs and adapt to the production of multiple products.
•
Quick Line Switching: By using standardized interfaces and quick replacement devices, quick switching between different products can be achieved, improving production flexibility.
9. Intelligent maintenance
•
Remote monitoring: Through IoT technology, remote monitoring and fault diagnosis of production equipment can be achieved, problems can be detected and solved in a timely manner, and downtime can be reduced.
•
Preventive maintenance: Using big data analysis technology to analyze the operational data of equipment, predict potential failures, perform maintenance in advance, and extend equipment lifespan.
Plum jam production line: raw materials and products
1. Raw materials
•
Plums: Choose fresh and moderately ripe plums as the main ingredient. Plums should be free from pests and diseases, have bright colors, and have a good taste.
•
Water: Used for cleaning plums and other purposes in the production process, the water quality should meet food production standards.
•
Sugar: Used to adjust the sweetness of jam, common sugars include white sugar, brown sugar, honey, etc.
•
Lemon juice: Adding lemon juice can increase the acidity of jam, make the taste more rich, and also have a certain preservative effect.
•
Spices (optional): According to product requirements, some spices such as cinnamon, vanilla, etc. can be added to enhance flavor.
2. Product
•
Plum jam: The finished plum jam should have the following characteristics:
•
Color: Deep red or purple red, with uniform color.
•
Taste: Delicate, smooth, with a certain thickness, non stick to teeth.
•
Flavor: Sweet with a hint of acidity, rich fruit aroma, and no off flavors.
•
Shelf life: Under appropriate conditions, it can usually be stored for 6-12 months.
•
Packaging: Common packaging forms include glass bottles, plastic bottles, aluminum foil bags, etc. The packaging should be well sealed, moisture-proof, and oxidation resistant.
Energy utilization and environmental protection are crucial aspects in the design and operation of plum jam production lines. Here are some key energy and environmental measures and technologies:
1. Energy utilization
•
Efficient boiler system: using efficient steam boilers to provide the heat energy required for production. Efficient boilers can reduce fuel consumption and improve thermal efficiency.
•
Waste heat recovery: In the preheating and concentration stages, waste heat recovery technology is used to reuse the generated waste heat and reduce energy consumption. For example, waste heat can be transferred to cold water through a heat exchanger for preheating raw materials or cleaning water.
•
Variable frequency drive technology: Variable frequency drive technology is used in equipment such as motors and pumps to adjust power according to actual needs and reduce unnecessary energy waste.
•
Energy saving lighting: Use energy-saving lighting equipment such as LED to reduce lighting energy consumption.
2. Environmental protection
•
Wastewater treatment: Equipped with a wastewater treatment system to treat the wastewater generated during the production process, ensuring compliance with environmental discharge standards. Common treatment methods include physical methods (precipitation, filtration), chemical methods (neutralization, coagulation), and biological methods (activated sludge, biofilm).
•
Waste gas treatment: During the concentration and sterilization process, some volatile organic compounds (VOCs) may be generated. Using technologies such as activated carbon adsorption and catalytic combustion to treat exhaust gases and reduce their impact on the environment.
•
Solid waste treatment: Reasonably handle solid waste generated during the production process, such as plum pits, fruit peels, etc. Resource utilization can be achieved through composting, biomass energy conversion, and other methods.
•
Noise control: During equipment design and installation, measures such as shock absorption and sound insulation are taken to reduce noise pollution, protect the working environment and the quality of life of surrounding residents.
3. Green packaging
•
Degradable materials: Use biodegradable or recyclable packaging materials to reduce the generation of plastic waste. For example, bio based plastics or paper packaging can be chosen.
•
Lightweight design: Optimize packaging design, reduce the use of packaging materials, and lower carbon emissions during transportation.
•
Reuse: Encourage consumers to reuse packaging containers and reduce the waste of disposable packaging.
4. Environmental monitoring and management
•
Online monitoring: Set up online monitoring equipment during the production process to monitor real-time emissions of wastewater, exhaust gas, etc., to ensure compliance with environmental standards.
•
Environmental Management System: Establish and improve an environmental management system, such as ISO 14001, develop environmental protection policies and procedures, conduct regular environmental audits and improvements.
•
Employee training: Regularly provide environmental awareness and skills training to employees to improve their environmental awareness and operational level.
5. Continuous improvement
•
Energy audit: Conduct regular energy audits to evaluate energy utilization efficiency, identify areas for improvement, and develop energy-saving measures.
•
Technological innovation: Continuously pay attention to and introduce new energy-saving and environmental protection technologies to enhance the green level of production lines.
•
Social responsibility: Actively participate in environmental protection activities in the community and industry, fulfill corporate social responsibility, and establish a good corporate image.
Customizing a plum jam production line is a complex process involving multiple steps, including raw material processing, processing, packaging, and more. Here is a detailed customized solution to help you plan and implement this project:
1. Requirement analysis
•
Product Objective: Determine the type of plum jam you wish to produce (such as plain, low sugar, organic, etc.).
•
Production scale: Determine the daily or hourly production capacity.
•
Quality standards: Clarify the quality standards of the product, including taste, color, nutritional content, etc.
•
Market positioning: Determine the target market and consumer group of the product.
2. Process flow design
Raw material processing
•
Raw material receiving: Set up a raw material receiving area to ensure the freshness and hygiene of the raw materials.
•
Cleaning: Use a cleaning machine to remove dirt and impurities from the surface of raw materials.
•
De nucleate: Use a de nucleating machine to remove plum pits.
•
Chop: Chop the pitted plums into small pieces for subsequent processing.
machining
•
Preheating: Use a preheater to heat the chopped plums, making them easier to process.
•
Beating: Use a beater to mash the heated plums into a pulp.
•
Concentrate: Use an evaporator to concentrate the slurry to the desired concentration, forming jam.
•
Sterilization: Use sterilization equipment to sterilize concentrated jam at high temperatures to ensure food safety.
•
Cooling: Cool the sterilized jam to a suitable temperature.
packing
•
Filling: Use a filling machine to fill jam into bottles or bags.
•
Sealing: Use a sealing machine to seal the packaging to ensure sealing.
•
Labeling: Use a labeling machine to attach labels to the packaging, indicating product information.
•
Packing: Pack the packaged jam into boxes and prepare for shipment.
3. Equipment selection
•
Raw material receiving area: conveyor belt, storage bin.
•
Cleaning machine: Bubble cleaning machine or spray cleaning machine.
•
De nuclear machine: an efficient de nuclear machine.
•
Chopper: Multi functional chopper.
•
Preheater: Steam preheater or hot water preheater.
•
Beating machine: Efficient beating machine.
•
Evaporator: Vacuum evaporator or thin film evaporator.
•
Sterilization equipment: high-pressure sterilization pot or continuous sterilization line.
•
Cooling equipment: Plate heat exchanger or cooling tower.
•
Filling machine: Automatic filling machine.
•
Sealing machine: rotary sealing machine or heat sealing machine.
•
Labeling machine: automatic labeling machine.
•
Packing machine: Automatic packing machine.
4. Technical consultation and evaluation
•
Cost assessment: Evaluate the cost of equipment, including purchase cost, installation cost, operating cost, and maintenance cost.
•
Technical evaluation: Evaluate the technical performance of equipment to ensure that it meets production requirements and quality standards.
5. Scheme confirmation
•
Technical exchange: Conduct detailed technical exchanges with suppliers to confirm the specific configuration and technical details of the equipment.
•
Contract signing: Sign a contract with the supplier to clarify the rights and obligations of both parties.
6. Production and manufacturing
•
Production preparation: The supplier prepares for production based on the confirmed plan, including raw material procurement, component processing, etc.
•
Assembly and debugging: After the equipment is assembled, preliminary debugging is carried out to ensure the normal operation of each component.
7. Installation and debugging
•
On site installation: Transport the equipment to your factory for on-site installation.
•
System debugging: Debugging the entire production system to ensure smooth operation of every link.
•
Performance testing: Conduct performance testing to ensure that the equipment achieves the expected production efficiency and product quality.
8. Training and Acceptance
•
Operation training: The supplier provides training to your operators to ensure they are proficient in operating the equipment.
•
Equipment acceptance: Conduct a comprehensive acceptance of the equipment to ensure that it meets the technical requirements and performance indicators stipulated in the contract.
9. Post service
•
Technical support: Suppliers provide necessary technical support to solve problems that arise during equipment operation.
•
Maintenance and upkeep: Regularly maintain and upkeep equipment to extend its service life.
Matters needing attention
•
Regulatory compliance: Ensure that the design and production of equipment comply with local food safety regulations and standards.
•
Environmental protection: Consider the environmental performance of equipment and reduce the discharge of wastewater and exhaust gas.
•
Safety measures: Ensure the safety performance of the equipment and prevent accidents during operation.
I hope the above plan can help you smoothly customize an efficient plum jam production line.
Shanghai Beyond Machinery Co., Ltd.
Beyond Machinery specializes in the design and manufacturing of plum jam production line.Please contact us now, and ourprofessional technical engineers will customize the equipment plan for plum jam production line and provide a quotation.Please contact us now to obtain the latest equipment plan and quotation.