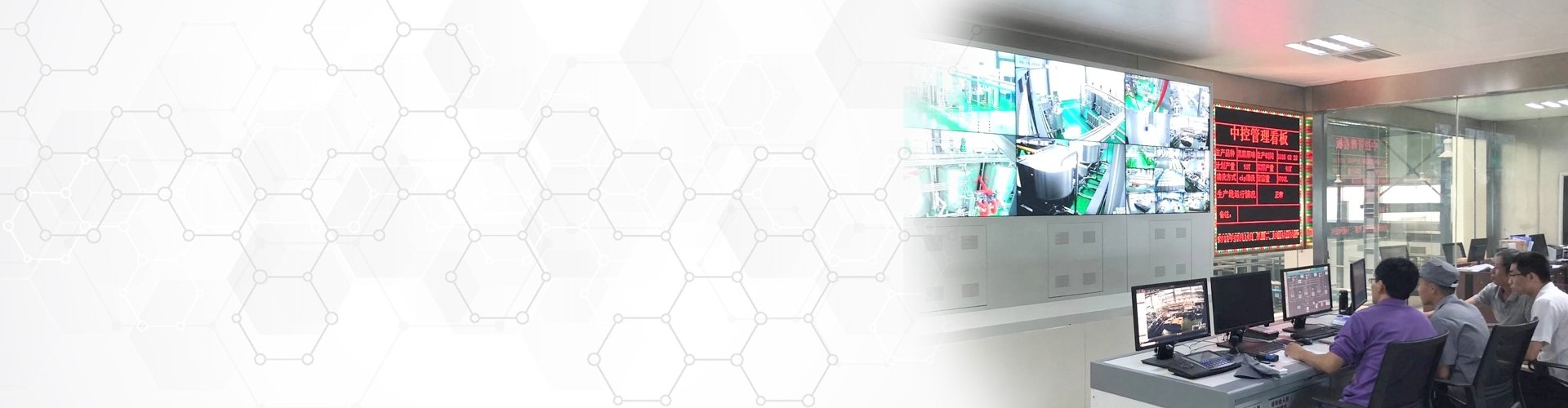
Carrot juice processing line is a facility dedicated to processing fresh carrots into high-quality concentrated or freshly squeezed carrot juice. The following is a detailed description of its principles, equipment, technology and customized needs:
I. Processing principle
1. Raw material reception and pretreatment
• Receive fresh carrots shipped from the field.
• Perform preliminary screening to remove impurities and unqualified carrots.
• Sort by variety and size.
2. Cleaning and disinfection
• Thoroughly wash the carrots to ensure that the soil and pesticide residues on the surface are removed.
• Disinfect when necessary to prevent microbial contamination.
3. Peeling and slicing
• Use mechanical equipment to peel the carrots to reduce fiber and unpleasant flavors.
• Cut the carrots into small pieces or slices for subsequent processing.
4. Crushing and juicing
• Use a crusher to break the carrot pieces into a pulp.
• Extract the juice by pressing or centrifugal separation technology to ensure that the juice is pure and without residue.
5. Heating and Concentration (Optional)
• If concentrated carrot juice is produced, the juice needs to be placed in an evaporator and heated to evaporate the water to achieve the concentration effect.
• Control temperature and time to ensure that the nutrients are not destroyed during the concentration process.
6. Homogenization
• After being processed by a high-pressure homogenizer, the carrot juice has a finer and more uniform texture.
• Improve taste and stability and extend shelf life.
7. Sterilization and Cooling
• Sterilize at high temperature to kill possible harmful microorganisms.
• Cool to a suitable temperature and prepare for subsequent processes.
8. Filling and Packaging
• Aseptically fill the finished carrot juice to ensure product quality.
• Use appropriate packaging materials (such as glass bottles, plastic bottles, metal cans, etc.) and label them for easy transportation and sales.
9. Quality Control and Testing
• Set up online testing points in key processes to monitor product quality in real time.
• Conduct sensory evaluation, physical and chemical index analysis, and microbial testing on each batch of finished products to ensure that they meet quality standards.
2. Main equipment
1. Cleaning equipment
•Automatic cleaning machine, equipped with spray device and brushing mechanism.
2. Peeling equipment
•Rotary peeling machine, using friction to remove carrot skin.
3. Cutting equipment
•Slicer or dicer, cut carrots into small pieces or slices of suitable size.
4. Crushing and juicing equipment
•Crusher, crush carrot pieces into pulp.
•Presser or centrifuge, efficient juice extraction.
5. Heating and concentration equipment
•Multi-effect evaporator, suitable for concentrated juice, energy saving and environmental protection.
6. Homogenization equipment
•High-pressure homogenizer, improve product texture and stability.
7. Sterilization equipment
•Sterilizer or tunnel sterilizer, to ensure food safety.
8. Filling and packaging equipment
•Automatic filling machine and sealing machine, to ensure good sealing.
•Packaging production line, including labeling machine, cartoning machine, etc.
3. Key technologies
1. Automation control
•Introduce PLC control system to realize full-line automation operation and improve production efficiency and stability.
2. Hygiene and safety
•Comply with GMP (Good Manufacturing Practice) and HACCP (Hazard Analysis and Critical Control Point) standards to ensure food safety.
3. Environmental protection and energy saving
•Apply wastewater treatment system to reduce environmental pollution.
•Use renewable energy such as solar energy and wind energy to reduce energy consumption and carbon emissions.
4. Fresh-keeping technology
•Adopt advanced fresh-keeping technology and packaging materials to extend the shelf life of products.
4. Customized needs
1. Production capacity customization
•Design production lines with different production capacities according to customer needs, from small experimental lines to large industrial production lines.
2. Product type customization
•Support a variety of product forms, such as freshly squeezed carrot juice, concentrated carrot juice, organic carrot juice, etc.
•Specific nutrients or seasonings can be added to develop functional carrot juice.
3. Process customization
•Adjust the process according to specific customer requirements, such as adding or reducing certain processes.
•Provide flexible modular design to facilitate future expansion and upgrading.
4. Equipment configuration customization
• Select the appropriate equipment combination according to budget and site conditions to ensure the best cost performance.
• Provide equipment maintenance and training services to ensure stable operation of the production line.
Carrot juice processing line: raw materials and products
I. Raw materials
1. Fresh carrots
• Source: Fresh carrots are usually purchased from agricultural bases or cooperative farmers to ensure the quality and stability of raw materials.
• Quality requirements:
• Moderate maturity, bright color, free of pests and diseases.
• Smooth surface, regular shape, uniform size.
• High freshness, sufficient moisture, less fiber.
2. Water
• Use: Used for washing carrots and as a solvent for certain processes in the production process.
• Water quality requirements: Meet drinking water standards, filtered and disinfected to ensure safety and hygiene.
3. Auxiliary materials (optional)
• Sweeteners: such as sucrose, honey, etc., used to adjust the taste.
• Vitamin C: used for antioxidants to maintain the freshness and color of the juice.
• Other additives: such as stabilizers, preservatives, etc., added according to specific needs, but must meet food safety standards.
II. Products
1. Freshly squeezed carrot juice
• Features: It retains the original nutrients and natural flavor of carrots and has a refreshing taste.
• Applicable scenarios: Suitable for daily drinking at home, catering industry and ready-to-drink market.
• Packaging form: glass bottle, plastic bottle, paper box, etc., with a capacity ranging from 200ml to 1L.
2. Concentrated carrot juice
• Features: By removing part of the water through evaporation, the concentrated carrot juice has a higher concentration and is easy to transport and store.
• Applicable scenarios: Mainly used for subsequent processing, such as dilution to make freshly squeezed carrot juice or other products containing carrot ingredients.
• Packaging form: Large-capacity packaging such as metal cans and plastic barrels, suitable for industrial users.
3. Organic carrot juice
• Features: Using organically grown carrots as raw materials, emphasizing no pesticide residues and no chemical fertilizers, which is healthier and more environmentally friendly.
• Applicable scenarios: Targeting health-conscious consumer groups, such as organic food stores, high-end supermarkets, etc.
• Certification: Certification by relevant organic certification agencies is required to ensure product quality.
4. Functional carrot juice
• Features: Add specific nutrients or seasonings, such as rich in vitamin A, low sodium, low sugar, etc., and develop special flavors, such as spicy and garlic flavors.
• Applicable scenarios: meet the needs of different consumers, such as athletes, the elderly, children and other specific groups.
• Packaging form: diversified design to attract target consumer groups.
5. By-products
• Carrot residue: the residue after juicing can be further processed into feed, organic fertilizer or dried to make carrot powder to achieve resource recycling.
• Wastewater treatment: wastewater generated during the production process can be used for irrigation or other non-food purposes after treatment to reduce environmental pollution.
To ensure that the carrot juice processing line can fully meet your needs, every step from initial consultation to final delivery needs to be carefully planned and implemented. The following is the detailed customization process:
1、 Needs assessment
1. Preliminary communication
• Content: Understand your specific needs, including production scale, product types, budget range, site conditions, etc.
• Method: Detailed communication through phone, email, or face-to-face meetings.
2. On site inspection (optional)
• Content: Conduct on-site inspections of factories or proposed sites, evaluate the actual situation of spatial layout, infrastructure, etc.
Purpose: To provide a basis for designing a reasonable production line.
3. Requirement confirmation
• Document: Based on the communication results, form a "Requirements Specification" to clarify various technical parameters and functional requirements.
• Signature: Both parties confirm and sign the document as the basis for subsequent design and manufacturing.
2、 Scheme design
1. Process flow design
Content: Design the optimized production process based on the characteristics of raw materials, product quality requirements, and production capacity targets.
• Tools: Use professional software to draw process flow diagrams, ensuring that each step is clear and concise.
2. Equipment selection
• Content: Select suitable key equipment such as cleaning machines, peeling machines, crushers, juicers, sterilizers, filling machines, etc.
Standards: Adhere to food safety standards such as GMP and HACCP to ensure equipment quality and safety.
3. Automation control design
Content: Introduce PLC control system to achieve automated operation of production line, improve efficiency and stability.
Modular design: easy to expand and upgrade in the future, adapting to business development needs.
4. Auxiliary facility design
Content: Design supporting facilities such as wastewater treatment system, air purification system, temperature control system, etc. to ensure environmental protection and energy conservation.
Integration: Organically integrate all equipment and systems to form a complete processing line.
5. Scheme review
• Meeting: Hold an internal review meeting and invite technical personnel, project managers, and relevant experts to attend.
Feedback: Collect opinions from all parties and optimize and adjust the design scheme.
6. Customer confirmation
• Demo: Show you the final design plan, including 3D models, process animations, etc.
• Modification: Make necessary adjustments based on your feedback until satisfactory.
3、 Manufacturing and installation
1. Equipment manufacturing
Factory production: Equipment manufacturing is carried out in a professional factory according to the design plan to ensure quality and progress.
Quality inspection: After each process is completed, strict quality inspection is carried out to ensure the factory pass rate.
2. Transportation and delivery
• Packaging: shockproof and waterproof packaging is used to ensure the safe delivery of the equipment to the destination.
Logistics tracking: Real time monitoring of the transportation process and timely handling of unexpected situations.
3. On site installation
• Team: Dispatch a professional installation and technical service team to work on site.
Construction management: Strictly follow the construction plan for installation and commissioning to ensure timely completion.
4. Trial operation
• Testing: Conduct a comprehensive trial run test to check the operational status of each device and system.
Problem solving: Identify and resolve issues that arise during trial operation to ensure the stability and reliability of the production line.
4、 Acceptance and Training
1. Project acceptance
Standard: Conduct acceptance according to the standards stipulated in the contract to ensure that the production line achieves the expected results.
Report: Provide a detailed acceptance report, recording various indicators and test results.
2. Operation training
• Content: Provide comprehensive operational training for your employees, including equipment use, maintenance, troubleshooting, etc.
• Information: Provide detailed user manuals and technical documentation for easy daily reference.
3. After sales service
Promise: Provide long-term technical support and after-sales service to ensure the continuous and stable operation of the production line.
Follow up: Regular follow ups to understand usage and promptly resolve issues.