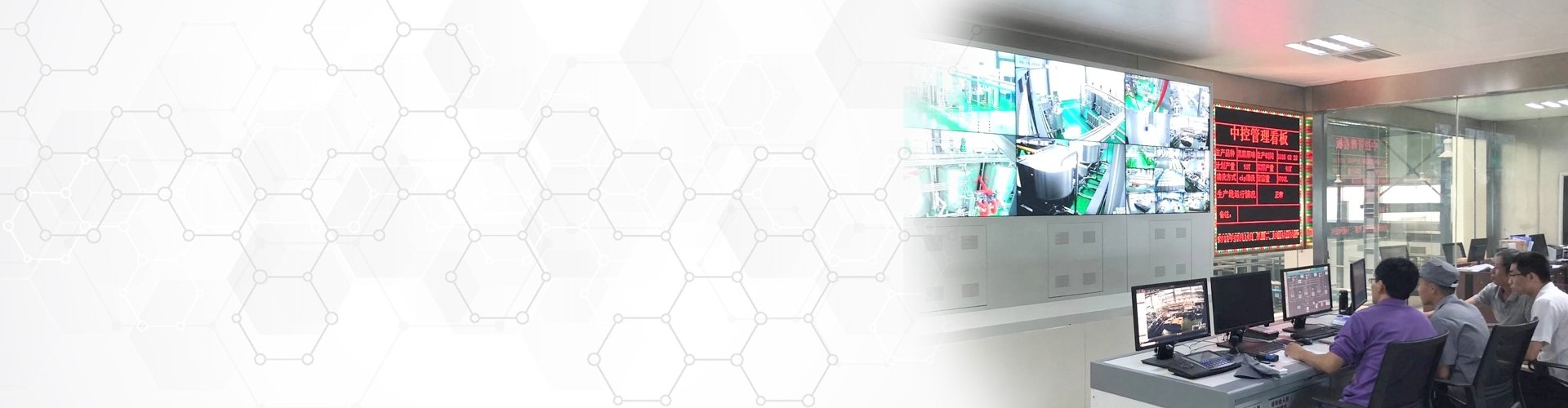
A beer processing line refers to the series of steps and equipment used in the production of beer. This line typically involves several stages, including milling, malting, mashing, boiling, fermentation, filtration, carbonation, and packaging.
Milling: In this stage, the malted barley is crushed into small particles to expose its starches. This process helps in the extraction of sugars during mashing.
Malting: The crushed barley is then soaked in water and allowed to germinate. This activates enzymes that convert complex carbohydrates into simple sugars. After germination, the barley is dried and becomes malt.
Mashing: The malt is mixed with hot water in a vessel called a mash tun. This allows the enzymes in the malt to break down starches into fermentable sugars. This mixture is known as the mash.
Boiling: The mash is transferred to a brew kettle where it is boiled. Hops are added at this stage to provide bitterness, flavor, and aroma to the beer. Boiling also sterilizes the liquid and helps to remove unwanted proteins.
Fermentation: After boiling, the liquid, known as wort, is cooled and transferred to a fermentation vessel. Yeast is added, and fermentation takes place, converting the sugars in the wort into alcohol and carbon dioxide. This process usually takes several days to weeks.
Filtration: Once fermentation is complete, the beer is filtered to remove any remaining solids or impurities. This can be done through various methods, including centrifugation, diatomaceous earth filtration, or membrane filtration.
Carbonation: After filtration, carbonation is added to the beer. This can be achieved by injecting carbon dioxide directly into the beer or by allowing the beer to naturally carbonate through a secondary fermentation process.
Packaging: The final step in the beer processing line is packaging. The beer is typically bottled, canned, or kegged. Labels and packaging materials are applied, and the beer is ready for distribution and consumption.
Throughout the beer processing line, quality control measures are implemented to ensure consistency and adherence to specific brewing standards. These may include regular testing of the product for alcohol content, pH levels, flavor profiles, and microbiological analysis.
Characteristics of beer processing line
All our brewery equipment is made of high quality stainless steel. They have good wear resistance and meet the requirements of equipment. POSCO Stainless Steel Certification.
For welding, we adopt the most advanced welding method, which makes the joint more beautiful and firm. After welding, the internal polishing will be polished to 0.4 μ m. No dead space. It is important that we conduct pickling to avoid rust and prolong the service life of the tank.
We have adopted an electrical control system on the production line to more accurately control the temperature of the saccharification tank and fermentation tank, which can be used on the mobile phone APP or remotely controlled.
Various container combinations and many containers: multi-functional tank (mixing kettle launder, kettle vortex), single process tank (mixing tank, launder, boiling kettle, vortex, hot/cold water tank);
Full piping and wiring, including valves and sensors; Integrated pump system;
CIP system: independent CIP of separate storage tank to prevent cross product interference;
The main interface control system (touch screen control panel), stairs and platforms combine the container into a compact unit, and the perforated and segmented structure of the walkway on the surface ensures that sliding is prevented;
Automatic cleaning, automatic water mixing
High quality thermal insulation effect: rock wool
Beautiful welding and polishing: full argon shielded welding.
The world's top brand of electronic components.
Wear resistant material: inner sheath (SUS304)
Fermentation device: standard stainless steel conical and cylindrical fermentation tank; The number of cans is calculated accurately according to the fermentation cycle of various beers; Including all manholes, valves, pressure gauges, accessories, etc.
Bright pot device: standard stainless steel bright pot, used for beer maturation, regulation, service and carbonation; The number of cans is accurately calculated for various beers and functions; Including all manholes, valves, stones, instruments, accessories, etc.
Cooling device: insulated glycol water tank, with or without copper coil for glycol liquid retention and mixing; High efficiency refrigerator provides cooling energy; Sanitary centrifugal pump for circulating glycol water between storage tank and heat exchanger; Including all pipes, fittings and insulation materials.
Control unit: electrical control cabinet with temperature for brewing switch control; Electrical control cabinet with switch control of temperature and cooling components; Including temperature controller, thermocouple, solenoid valve, etc; PLC with touch screen panel for special requirements.
Perfect patent design, including beer equipment and filling machine, all of which have passed CE certification.
For your turnkey project, we only need to provide an installation team to install the entire project. We have agents in many countries in the world. Therefore, we can provide equipment and services at any time.
Our beer processing lines can be designed and manufactured according to the needs of customers. The beer processing lines are mainly used in medium-sized and large craft breweries for beer production. For retail industrial breweries, equipped with industrial brewing wort machines and modern professional beer production equipment, such as cylindrical and tapered beer fermenters or open fermenters, automatic cooling systems, cleaning and disinfection systems, can be used to produce all known types of beer. The main part of the brewery is the stainless steel wort brewing machine. Its industrial design is simple, aiming to maximize the working efficiency and production capacity of the brewery.