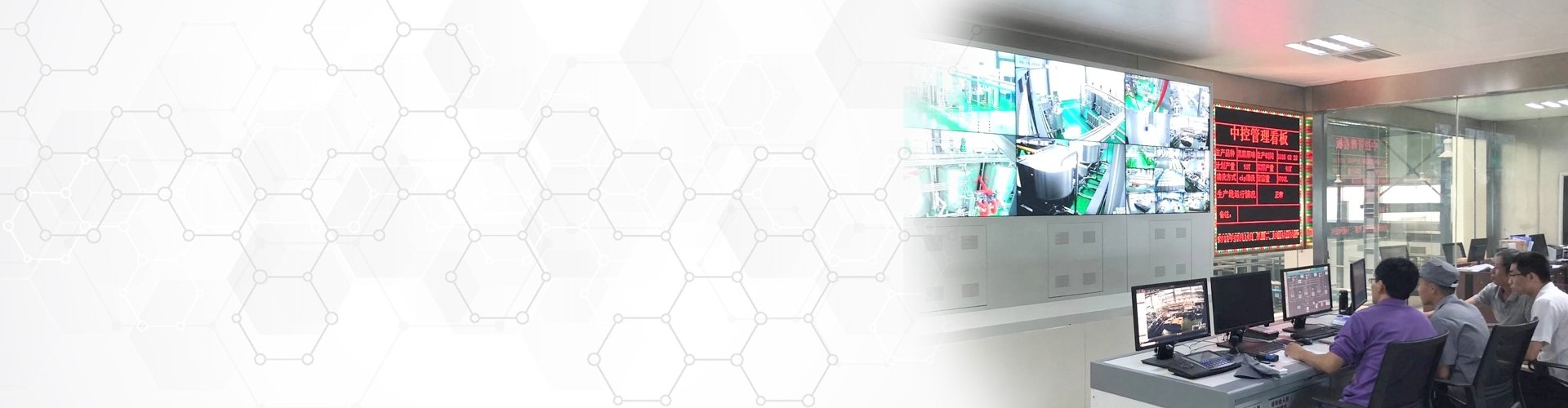
Juice、Tea、Dairy Beverage Processing Line Description
A juice tea dairy beverage processing line is a series of machines and equipment used to produce various beverages such as fruit juices, tea drinks, and dairy-based beverages. The line typically includes the following steps:
Raw material preparation: Fruits, tea leaves, and dairy ingredients are collected and prepared for processing. This may involve washing, sorting, peeling, and grinding or extracting the desired components.
Mixing and blending: The extracted juice, brewed tea, and dairy ingredients are mixed together in a tank to create the desired flavor profile and consistency. Sweeteners, flavorings, and other additives may also be added at this stage.
Pasteurization: The mixture is heated to a specific temperature to kill any harmful bacteria and extend the shelf life of the beverage.
Homogenization: The mixture is passed through a homogenizer to ensure uniform distribution of particles, prevent separation, and improve stability.
Filtration: The beverage is filtered to remove any solids or impurities that may affect the taste or appearance.
Carbonation (optional): If carbonated beverages are being produced, carbon dioxide gas is infused into the liquid under pressure to create the desired level of fizz.
Cooling: The beverage is cooled to a suitable temperature before further processing or packaging.
Packaging: The beverage is filled into bottles, cans, or cartons using filling machines. Packaging materials may vary depending on the type of beverage being produced.
Sealing: The containers are sealed to prevent contamination and ensure product integrity.
Labeling and coding: Labels are applied to the containers, providing important information such as product name, ingredients, nutritional facts, and expiry dates. Codes may also be printed for traceability purposes.
Quality control: Throughout the process, quality control measures are implemented to ensure the beverages meet the desired standards for taste, appearance, safety, and shelf life. This may include sensory evaluation, laboratory analysis, and equipment calibration.
The specific design and configuration of a juice tea dairy beverage processing line may vary depending on the specific requirements and production capacity of the facility.
Classification of Plant Beverage
Cocoa drink
Cocoa beans and cocoa powder are used as raw materials,other auxiliary materials and food additives are added,and the beverage is prepared through blending,homogenization,and sterilization.
Cereal beverages
Use cereals as raw materials,add auxiliary materials and food additives,blend,homogenize,and sterilize beverages.
Herbal drink
The edible parts of plants,including roots,stems,leaves,flowers,fruits,and seeds,are used as raw materials,and flavor substances and ingredients are added to make beverages,such as herbal tea and flower beverages.
Edible fungus beverage
The beverage is prepared by using the edible fungus or extract of the edible fungus fruiting body as the raw material,or the fermented liquid of the edible fungus as the raw material,after preparation,and sterilization.
Algae drink
Use algae as raw material,add auxiliary materials and food additives,blend,homogenize,and sterilize the beverage.
Tea drink
Tea beverage is a kind of soft drink containing a certain amount of natural tea polyphenols,caffeine and active ingredients of tea,which is processed from tea leaves or tea powder and tea extract as the main raw materials.This kind of beverage not only has the unique flavor of tea,but also with mutrition,health care and medical effects,it has become a multi-functional beverage popular among consumers.Tea beverage have revolved from the earliest traditional brewing to a family of tea beverages with varieties such as instant tea,fruit juice tea,and health tea.
Plant Beverage Production Line Main Process Introduction
Raw material selecting
There are many varieties of plant raw materials,and the edible parts vary greatly.The raw materials used are of good quality,taste and color,and requir freshness,no mildew,no peculiar smell,and no impurities.If you want to make a composite beverage,fruits and vegerables can also be added.The added fruits and vegetables make the nutrition of the beverage more complete,and at the same,it can also cover up the unpleasant smell and flavor of some raw materials.
Plant beverage refining and extraction machine
Refining and extraction are very important steps in the processing of plant beverages.For raw materials that requir refining(grain beverages),the amount of water added during refining is 75%-80% of the total water content of the blended beverage,and two stage grinding is used when refining for pulp(coarse grinding and fine grinding),the particle diameter after coarse grinding is greater than 80 mesh,and after fine grinding,the particle diameter is greater than 120 mesh.
Plant beverage blending and formulation tank
The sugar-acid ratio directly affects the taste of the beverage.The appropriate sugar-acid ratio is 13.1-15.1.Generally,white sugar is used as a sweetener,citric acid is used as a sour agent,and which is also has a certain preservative effect.As an antioxidant,vitamin C is not only a nutrient needed by the human body,but also has an antioxidant function.In addition,adding different flavors and pigments can not only make different beverages,but also improve the appearance of the product.
Plant beverage clarification and homogenization
Due to the need for clarified and transparent juice,some plant beverages requir clarification during the production process to remove suspended solids in the juice.Usaually need to use a centrifuge to clarify.
Plant beverage sterilizing and filling
According to the composition characteristics of plant beverages,different sterilization processes can be used,generally high-temperature short-term sterilization or ultra-high temperature instantaneous sterilization process is adopted.The homogenized material is sealed and filled,and sterilized at 121℃ and pressure 2kpa for 15-20min.For heat-sensitive and nutrient-containing plant beverages,they can be filled into containers after sterilization at 130-140℃ and 3-4S.
Name |
Model
|
Main technical parameters |
QTY
(piece) |
|
Extracting and filtering system |
|
|||
Extracting tank |
600L
|
SUS 304, insulation, top central paddle mixer, sealed manhols, bottom outlet and discharge,oval head and bottom conical cover angle is more than 45 degree,cylinder stator full auto on-off at the discharge and the self-lock device |
2
|
|
Centrifugal pump |
10T/h
|
SUS 304, H=24m, high-quality mechanical seal, ABB motor |
1
|
|
Duplex cloth filter |
10T/h
|
SUS 304, Duplex type, 200mesh |
1
|
|
Plate cooler |
10T/h
|
SUS304, three stages, temperature cooling from 95-15degree, first stage, cooling by RO water, second stage, cooling by tower water, third stage ice water |
1
|
|
Tea water storage tank |
2000L
|
material SUS 304, single layer, conical cover,Airtight manhole, breathing valve, digital display thermometer |
1
|
|
Centrifugal pump |
5T/H
|
SUS 304, H=24m, high-quality mechanical seal, ABB motor |
1
|
|
Duplex tube filter |
5T/H
|
SUS 304, Duplex type, 200mesh |
1
|
|
Disk centrifuge |
3T/h
|
self discharge |
1
|
|
CIP return pump |
20T/h
|
SUS304, lift:20m, mechanical seal |
2
|
|
Sugar desolving and storaging system |
|
|||
High speed blender |
500L
|
SUS304,insulation,bottom high speed emusifying head, digital display thermometer |
1
|
|
Centrifugal pump |
10T/H
|
SUS 304, H=24m, high-quality mechanical seal, ABB motor |
1
|
|
Duplex tube filter |
10T/h
|
SUS 304, Duplex type |
1
|
|
Plate cooler |
10T/h
|
SUS 304, one stage, cooling from 80 degree to 40 degree |
1
|
|
Diatomite filter |
Q=5t/h
|
Containing the precoat tank and precoat pump |
1
|
|
Sugar liquor |
1500L
|
SUS 304, single layer, conical cover, sealed manhole, breathing value, digital display themometer |
2
|
|
Centrifugal pump |
10T/h
|
SUS 304, H=24m, high-quality mechanical seal, ABB motor |
1
|
|
CIP return pump |
20T/h
|
SUS304, lift:20m, mechanical seal |
1
|
|
Mixing system |
|
|||
Mixing tank |
3000L
|
SUS 304, single layer,top off-set stirring, sealed manhole, digital display themometer, conical cover |
2
|
|
Centrifugal pump |
5T/h
|
SUS 304, H=24m, high-quality mechanical seal, ABB motor |
1
|
|
Duplex cloth filter |
5T/h
|
SUS 304, Duplex type, 200mesh |
1
|
|
CIP return pump |
20T/h
|
SUS304, lift:20m, mechanical seal |
|
|
Sterilizing system |
|
|||
Tubular sterilizer |
3000L
|
Tubular type, sterilizing temperature 120 degree, 15 seconds, PLC full automatic control, hot filling |
1
|
|
E. Hot water system | ||||
Hot water tank |
3000L
|
SUS 304, insulation, conical cover, sealed manhole, breathing value, digital display themometer |
1
|
|
centrifugal pump |
10T/h
|
SUS 304, H=24m, high-quality mechanical seal |
1
|
|
Plate cooler |
10T/h
|
SUS304,one stage |
1
|
|
Temperature control system |
10T/h
|
Spirax sarco steam reduced pressure, control system |
1
|
|
Semi automatic CIP system | ||||
Full-automatic CIP system | 3×2T | SUS 304, inner layer 316,single circuit,Germany Burkert temperature control system, America concentrate acid and alkali adding system 100L*2 tanks, automatic temperature control,and automatic acidity , Washing process automatic control, fault alarm concentrated acid/alkali tanks |
1
|
|
Installation system | ||||
Stainless steel piping unit | Including the pipe lines as well as the CIP system before the filling, follows SMS standard pipe size: ¢63,¢51,¢38 |
1
|
||
Power piping unit | Power line and heat preservation for the main line excluding filling system |
1
|
||
Electric control cabinet | Control cabinet for main line excluding filling part |
1
|
||
Electric wires and connecting material | Electric wires and connecting material for main line excluding filling part |
1
|
The installation and debugging process for a Juice, Tea, or Dairy Beverage Processing Line typically involves several key stages to ensure that the equipment is properly set up, operates efficiently, and adheres to food safety standards.
Here's an overview of the general steps involved:
1. Site Preparation
• Clearance and Cleaning: The installation area must be thoroughly cleaned and cleared of any debris. It should also be sanitized to prevent contamination.• Infrastructure Setup: This includes preparing the necessary electrical, plumbing, and drainage systems according to the machinery's requirements.
2. Unpacking and Inspection
• Equipment Arrival: Check that all ordered components have arrived and compare against the shipping manifest.• Visual Inspection: Inspect each part for any damage during transit. Notify the supplier immediately if any issues are found.
3. Assembly
• Following Manual: Each machine or component comes with an installation manual. Adhere strictly to these instructions for proper assembly.• Alignment and Levelling: Ensure all machines are correctly aligned and levelled to prevent vibration and ensure smooth operation.• Piping and Wiring: Connect the necessary pipes for product flow, water supply, cleaning solutions, and waste disposal. Similarly, wire the electrical connections as per the diagrams provided.
4. Integration
• Integration with Control System: Modern beverage processing lines often have PLC (Programmable Logic Controller) systems for automation. Program and integrate all machines into this central control system.• Sensor Calibration: Calibrate sensors for temperature, pressure, and flow rates to ensure accurate readings.
5. Testing and Debugging
• Individual Machine Tests: Run each machine separately to ensure it functions correctly before integrating them.• System Test Runs: Conduct test runs of the entire production line with water or a non-food simulant to check for leaks, blockages, and performance issues.• Debugging: Identify and troubleshoot any problems that arise during testing. This may involve adjusting settings, replacing parts, or reprogramming control systems.
6. Sanitization and Sterilization
• Cleaning Protocol: Once debugging is complete, clean and sterilize the entire line to prepare for actual product processing.
7. Training
• Operator Training: Provide comprehensive training to the operators on how to use the equipment safely and effectively.• Maintenance Training: Train maintenance staff on routine checks, cleaning procedures, and basic troubleshooting.
8. Documentation and Certification
• Record Keeping: Document every step of the installation and debugging process for future reference.• Certification: Depending on the region, you might need to obtain certifications from local health authorities before starting commercial production.
It's crucial to work closely with the equipment manufacturer's technical support team throughout the process to ensure compliance with warranty conditions and optimal performance of the processing line.
Customized juice tea production line
Designing a customized juice tea production line requires consideration of multiple aspects, including production processes, equipment selection, raw material and product characteristics, and the layout of the production line. Here is a detailed solution:
1. Preparation of raw materials for production process
• Raw material reception and storage: Receive fresh fruits and tea leaves, store them in a suitable environment, and avoid spoilage.
• Pre processing: Pre processing steps such as cleaning, peeling, and slicing fruits, and pre processing steps such as screening and grading tea leaves.
extract
• Juice extraction: Use a juicer or press to extract juice from fruits.
Tea soup extraction: Use a tea soup extractor to extract tea soup from tea leaves, which can be done through soaking, steaming, and other methods.
blend
• Preparation: Mix the extracted juice and tea soup in a certain proportion, and add appropriate amounts of sugar, citric acid, vitamin C, and other ingredients according to the formula to adjust the taste and nutritional content.
filter
• Filtration: Use a filter to remove solid impurities from the mixed liquid, ensuring the purity of the product.
Homogenization
Homogenization: Use a homogenizer to refine the particles in the mixture, making it more uniform and improving taste and stability.
sterilization
Sterilization: Through high-temperature instantaneous sterilization (UHT) or pasteurization treatment, harmful microorganisms are killed to ensure the safety of the product.
cooling
• Cooling: Quickly cool the sterilized mixture to a suitable temperature to prevent bacterial growth.
filling
• Filling: Fill the cooled mixture into bottles, cans, or bags to ensure good sealing and prevent contamination.
seal
Sealing: Use a sealing machine to seal the packaging container to ensure sealing performance.
Labeling
Labeling: Attach labels to packaging containers, indicating product information, production date, shelf life, etc.
packing
• Packaging: Packaging the finished product for easy transportation and sales.
test
• Inspection: Conduct quality inspection on finished products to ensure compliance with relevant standards and regulatory requirements.
Storage
• Storage: Store qualified products in a suitable environment, usually a cool and dry place, to ensure product quality and shelf life.
2. Equipment selection: Main equipment
Raw material receiving and storage equipment: storage tanks, cold storage.
Pre processing equipment: cleaning machine, peeling machine, slicing machine, screening machine.
Extraction equipment: juicer, press machine, tea soup extractor.
• Mixing equipment: mixing tank, mixer.
• Filtering equipment: filter.
Homogenization equipment: Homogenizer.
Sterilization equipment: UHT sterilizer, pasteurizer.
Cooling equipment: cooling tower, cooling tunnel.
Filling equipment: filling machine.
Sealing equipment: sealing machine.
Labeling equipment: Labeling machine.
• Packaging equipment: packaging machine.
Inspection equipment: quality testing instruments.
Storage equipment: warehouse, cold storage.
3. Raw materials and product raw materials
• Fruits: Fresh, high-quality fruits such as apples, oranges, mangoes, etc.
• Tea: High quality tea such as green tea, black tea, oolong tea, etc.
• Accessories: sugar, citric acid, vitamin C, etc., used to adjust taste and nutritional content.
product
• Regular fruit juice tea: a basic fruit juice tea product.
Functional fruit juice tea: adding specific functional ingredients such as vitamins, dietary fiber, etc.
• Low sugar or sugar free juice tea: suitable for diabetes patients or consumers with strong health awareness.
• Special flavor juice tea: adding special flavors such as vanilla and mint to meet different market demands.
4. Customized demand production capacity
Capacity selection: Select equipment with appropriate capacity based on the size and demand of the factory.
Flexibility: Design adjustable production lines to meet the production needs of different products.
Product diversity
Multi flavor production: Design production lines for multiple flavors to meet the needs of different markets.
Special requirements: Provide juice tea production lines with special needs such as organic and low sugar.
Degree of automation
• Automation level: Select different levels of automation equipment based on budget and management needs.
Information management: Introduce information management systems to improve production efficiency and management level.
Environmental requirements
Wastewater treatment: Design a wastewater treatment system that complies with local environmental regulations.
• Waste management: Reasonably handle the waste generated during the production process.
hygienic standard
GMP and HACCP: Ensure that all equipment and facilities comply with hygiene standards such as GMP and HACCP.
• Cleaning and maintenance: Regularly clean and maintain the equipment to ensure the hygiene of the production environment.
5. Design and plan the overall layout
Raw material receiving area: used for receiving and inspecting the quality of raw materials.
Storage area: used for storing raw materials and finished products.
Processing area: including pre-treatment, extraction, blending, filtration, homogenization, sterilization, cooling and other processes.
Filling area: used for filling and sealing finished products.
Labeling area: used for labeling finished products.
• Packaging area: used for the outer packaging of finished products.
Finished product storage area: used for storing finished products and preparing them for shipment.
• Laboratory: used for quality control and testing.
Office and Rest Area: Provides a place for employees to work and rest.
6. Technical support
Automation and informatization: Introduce automated production lines and information management systems to improve production efficiency and management level.
• Training: Regularly train employees to ensure they master the latest technology and operating procedures.
After sales service: Provide comprehensive after-sales service and technical support to ensure the normal operation of the production line.