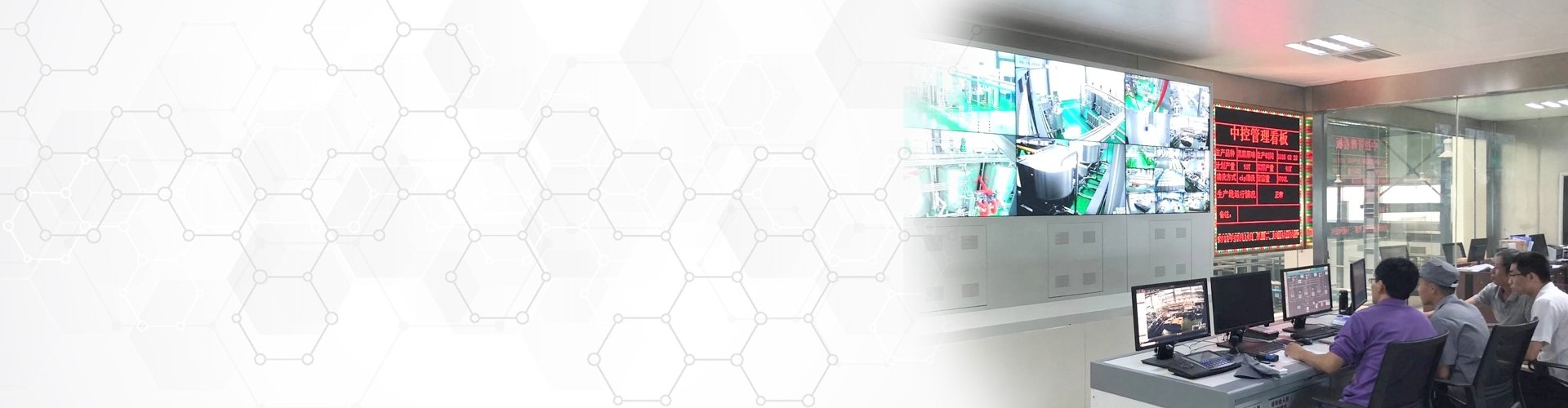
A three effect concentrator is a device used for separating, concentrating, and treating substances. It combines multiple technologies and principles to achieve efficient process operations.
The working principle of a three effect concentrator is to utilize a multi-stage evaporation process. Its core consists of three main steps: evaporation, condensation, and recompression. When the liquid mixture enters the concentrator, it first passes through the first evaporator. During this process, thermal energy is input, causing the liquid to partially evaporate and form steam. These vapors are then condensed through the condenser, releasing thermal energy and converting the steam back into a liquid state.
Then, the liquid substance passes through a second evaporator and undergoes higher levels of heating and evaporation, forming more steam. The steam condenses again through the condenser, producing more liquid substances. This process can be repeated multiple times at each level to achieve higher substance concentration effects.
Finally, the final concentration of the liquid is achieved through a third evaporator. During this process, a re compressor is used to compress and reheat the steam, converting it back into a liquid state, forming a more concentrated product. This multi-stage evaporation and condensation process enables the three-effect concentrator to achieve efficient material separation and concentration.
Triple effect concentrators are widely used in many industrial applications, such as in industries such as food processing, chemical engineering, and environmental protection. It can effectively reduce the discharge of waste and wastewater, and recycle and utilize valuable substances. In addition, the three effect concentrator also has the advantages of energy conservation, reducing production costs, and improving product quality and purity.
Overall, a three effect concentrator is an efficient device that achieves the separation and concentration of substances through multi-stage evaporation and condensation processes, and is widely used in various industries.
The working principle of the three effect concentrator is as follows:
The feed liquid first enters the first stage evaporator and is heated to a temperature above its boiling point. This can provide heat through steam or other thermal media.
The heated liquid partially evaporates in the first effect evaporator, generating steam. These vapors will be utilized in the next (second) evaporator.
In the second effect evaporator, through heat exchange, the steam generated in the first effect evaporator is used to evaporate more liquid and generate steam again.
Similarly, the steam generated in the second effect evaporator will be transmitted to the third effect evaporator.
In the third effect evaporator, further evaporation is carried out using the steam generated in the second effect evaporator, ultimately producing a more concentrated solution.
Throughout the process, steam will be recycled to improve energy efficiency. The concentrated liquid will also flow out of the last effect.
Compared to a single effect evaporator, a three effect concentrator has the following advantages:
Efficient and energy-saving: Through the design of multi effect evaporation, the principle of transferring heat from one effect to another is utilized, greatly improving energy utilization efficiency and significantly reducing energy consumption.
Greatly improved concentration efficiency: Due to the continuous utilization of steam heat, the three-effect concentrator can more effectively evaporate and concentrate the liquid, resulting in higher concentrations of products.
Strong adjustability: The three effect concentrator can be adjusted and controlled as needed to meet different process requirements and product concentration requirements.
However, the cost of a three effect concentrator is high, the equipment structure is complex, and maintenance and operation are also cumbersome. Therefore, when selecting evaporation equipment, factors such as production scale, cost-effectiveness, and operational requirements need to be considered.
Use
The concentractor adapted to trditional Chinese medicine,western medicine,dextrose,amylum,monosodium glutamate,foodstuff,chemical industry and other liquid material concentration shrinkage,especially for the low temperature heat-sensitive species in vacuo.
Characteristics
The concentrator adapt exterior heating natual circulation and vacuum evaporation,it has features of high evaporation speed and high concentration than the major,receive paste in closed condition.
Concentration of recoverable alcohol around 80℃.
It can feed material intermittent or continuously,reach concentration by once.
Each heating chamber tube,condenser tube,the intermediate connecting pipes are used inside and outside the ISO stand polished mirror surface of the pipe,to ensure the smooth flow of material,non-coking heating chamber clogging,reducing fouling and cleaning times,improve production efficiency.
The concentrator uses three effect evaporator while secondary steam to get reused,saving investment of boiler,but also save energy consumption,the energy consumption is 70% lower compared to other concentrators.
Technical parameters