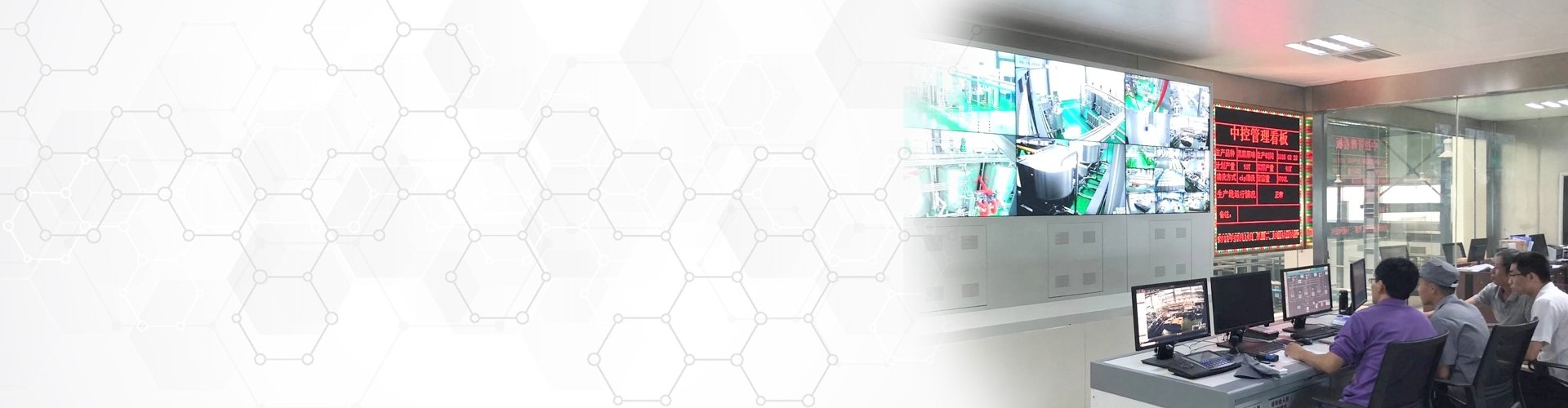
The multi coupling experimental fermentation system is an advanced fermentation equipment that can simultaneously control and monitor multiple fermentation reactions, and couple them together to simulate more accurate biological processes.
This system typically consists of multiple bioreactors, control systems, and data acquisition systems. Each reactor can independently control parameters such as temperature, stirring speed, pH value, oxygen supply, and achieve material transfer and mixing through interconnected pipelines and valves. The control system can coordinate the operations between different reactors to maintain the required coupling conditions.
The main advantages of a multi coupling experimental fermentation system include:
Simulate real environment: By coupling multiple reactors, complex biological reaction processes such as multi bacterial interactions and metabolic product transfer can be more accurately simulated.
Resource saving: A multi coupling system can perform multiple fermentation reactions simultaneously, increasing production efficiency and saving time and resources.
Data acquisition and analysis: The system is equipped with high-precision sensors and data acquisition systems, which can monitor the parameters of various reactors in real-time and provide rich data for analysis and optimization processes.
Scalability: The system can be expanded as needed, increasing or decreasing the number and scale of reactors to meet the experimental needs of different scales and complexities.
The multi coupling experimental fermentation system has wide applications in fields such as biopharmaceuticals, microbiology research, and fermentation engineering. It provides scientists and engineers with a powerful tool for exploring and optimizing biological processes, accelerating the development and production of new products.
Gas treatment
Compressed air,nitrogen,carbon dioxide treatment
1μm gas total filter,0.1μm gas prefilter,0.01μm gas precision filter,three-level aseptic filtraction.The material of filter membrane is PTFE.
Steam treatment
1μm total filter,0.5μm ultimate filter,two-level filtration,The filter material is titanium rod.
Control system
Temperature control
Temperature control:There are temperature sensors on the tanks,automatic control valve of cooling water and thermostatic water at the inlet and outlet of the jacket or inner coil pipe.Control temperature,start and stop temperature of cooling water and the thermostatic water can be set on automatic control touch screen.Under the self-control condition,the control modular can be switched and adjusted according to the control program.Temperature control precision is ±0.1℃
PH control
There is the PH electrode on the tank.User can set the fermentation PH value,and the PH value of acid and alkai refilling's start and stop,at the same time,user can set the speed of acid and alkali peristaltic pump.Under the condition of self-control,the control modular controls acid and alkali peristaltic pump to adjust the PH according to the control program.
Control precision is <0.2
Do control
1、There is DO(dissowed oxygen)electrode on the tank;
2、The mixing motor is adopting variable-frequency and with the mixing speed testing;
3、The gas pipe is loaded with automatic control regulating valve and vortex flowmeter;
4、Exhaust gas pipe is loaded with venting regulating valve.
Sequences adjustment
Adjust the frequency(speed)of mixing motor,ventilation flow,venting flow(the pressure of tanks).
User can set the power supply frequency of default mixing motor on automatic control touch screen.The frequency is usually between 35 and 40 Hz.Under the condition of self-control,the control modular can automatically adjust power supply frequency of mixing according to the control program.
User can set tje pressure of fermentation tank on the automatic control touch screen.The pressure is usaually between 0.02 and 0.05MPa.Under the condition of self-control,the control modular can automatically adjust regulating valve of ventilation to control exhaust gas flow according to the control program.
Control setting
Three levels permission is set in the system.
Junior-level permission:Operating foreman can only set the parameters of present manufacturing;
Senior-level permission:production technical manager can only set the manufacturing parameters of present batch;
Superior-level permission:chief technical engineer can fully set process parameters.
Review management
All production process parameters are automatically saved and can be read and printed according to the authority.
System protection
Automatic control system uses UPS for uninterrupted power supply.
Parameter Category
Parameter Name
Unit Typical
Parameters
Capacity fermentation
Tank capacity
L
10-200
Number
Number of fermentation tanks
A
4-8
Material
Fermentation Tank Material
-
Stainless Steel, Glass, etc
Temperature range
Fermentation temperature
° C
20-50
Control accuracy Temperature
Control accuracy
±° C
±0.1
Heating methods
Heating methods
-
Electric heating, water bath heating etc
Cooling methods
-
Water cooling, air cooling, etc
Mixing system
Mixing speed
Mixing speed
rpm
0-1000
Mixing form
Mixing blade type
-
Flat blade, spiral blade, etc
Ventilation system
Ventilation speed
Ventilation rate
L/min
0-10
Ventilation pressure
Ventilation pressure
bar
0-1
PH control system
PH range
PH adjustment range
-
3-10
Control accuracy
PH control accuracy
±
± 0.05
Dissolved oxygen monitoring
Dissolved oxygen range
Dissolved oxygen concentration
% DO
0-100
Measurement accuracy
Dissolved oxygen measurement accuracy
±% DO
± 0.5
Data recording
Data recording interval
Recording time interval
Min
1-60
Storage Capacity
Data Storage Capacity
GB
1-10
The customized process for a Multi Coupled Experimental Fermentation System typically includes the following steps:
1. Requirement communication: Firstly, we will have detailed communication with you to understand your specific requirements. This includes but is not limited to the
required number of fermentation tanks, capacity size, desired control accuracy, and special functional requirements.
2. Scheme design: Based on the collected requirement information, our technical team will tailor a design scheme for you. This stage may involve the selection of equipment configuration, the design of process flow, and we will present you with a preliminary design plan to obtain feedback.3. Confirm order: Once both parties have reached an agreement on the design proposal, the formal ordering process can begin. At this point, we will provide a clear price list and contract for your review and signature.
4. Manufacturing: After signing the contract, we will begin the production and assembly of the equipment according to the established specifications. This process may take some time, please be patient.
5. Quality inspection: After all components are assembled, a comprehensive quality inspection will be conducted to ensure that each machine meets the factory standards.
6. Shipping and installation: Products that have passed quality inspection will be properly packaged and arranged for transportation to the designated location. After arriving at the destination, professional personnel will be responsible for on-site installation and debugging until the equipment can operate normally.
7. Training guidance: In order to help customers better master the usage methods, we will also provide necessary operational training and technical support services.
8. After sales service: Finally, we promise to provide free maintenance services and other forms of technical support within a certain period of time to safeguard the interests of our customers.