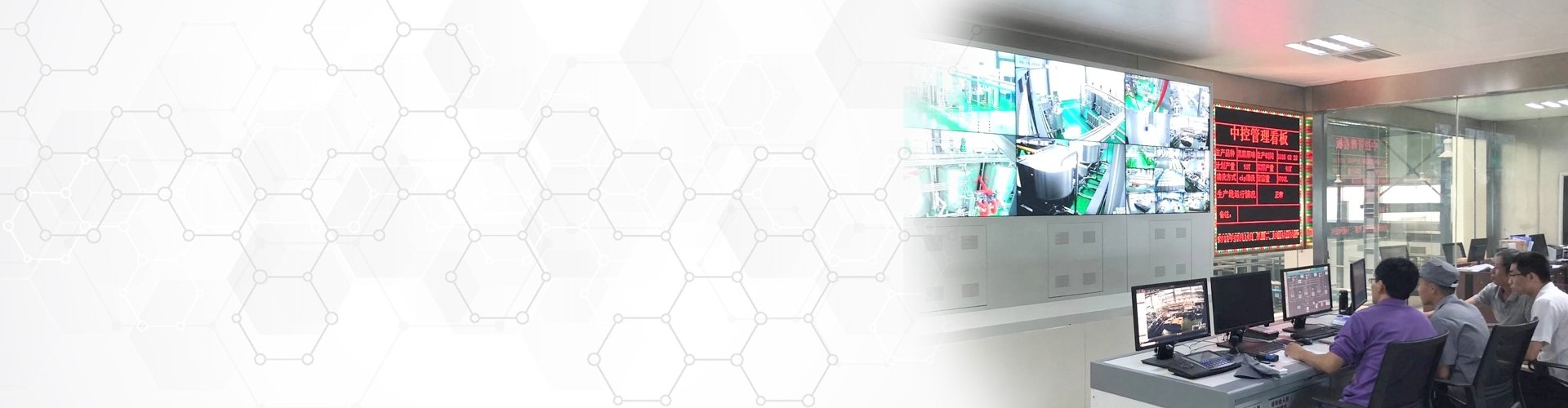
The fully automatic large-scale CIP (Cleaning In Place) system is a system used for automatic cleaning of production equipment in industries such as food, beverage, and pharmaceuticals. It can efficiently clean and disinfect without disassembling the equipment. Its working principle can be roughly divided into the following steps:
1. Pre rinsing stage: First, use clean water (at room temperature or hot water) to preliminarily rinse the interior of the equipment, with the aim of removing residual materials and impurities, in preparation for subsequent cleaning steps.
2. Cleaning agent circulation: Then inject an appropriate cleaning agent solution (such as alkali solution, acid solution, or other specialized cleaning agents), and circulate the cleaning solution inside the equipment through a booster pump. During the circulation process, devices such as nozzles and rotating sprayers are used to ensure that the cleaning solution can cover every corner of the equipment, effectively removing attached dirt and microorganisms.
3. Soaking: In some cases, the equipment may be required to soak in a state filled with cleaning agent for a period of time in order to more thoroughly decompose stubborn stains.
4. Rinse stage: After completing the cleaning agent cycle, rinse the system again with a large amount of water to thoroughly remove any remaining cleaning agent and prevent contamination of the product.
5. Disinfection stage (if necessary): For industries with extremely high hygiene requirements, this step will use hot water or chemical disinfectants (such as peracetic acid, hydrogen peroxide, etc.) to disinfect the system to ensure sterility.
6. Final rinsing: After disinfection, rinse again with clean water to remove all disinfectant residues until the water quality test is qualified.
7. Evacuation and drying (optional): Finally, the liquid in the system is emptied, and some systems can also be air purged or naturally air dried to accelerate the drying process of the equipment and prepare for the next production cycle.
The fully automatic CIP system, through automated control of these cleaning steps, not only greatly improves cleaning efficiency and reduces labor costs, but also ensures consistency and traceability of cleaning effects, making it an indispensable part of modern production lines.
Split Type Full-Auto CIP Cleaning System is a type of cleaning system used in various industries, such as food and beverage, pharmaceutical, and dairy industries. It is designed to clean and sanitize the interior surfaces of tanks, piping systems, and other equipment without disassembling them.
The split type refers to the separation of the cleaning system into two parts: the cleaning head and the control panel. The cleaning head is installed inside the tank or the equipment to be cleaned, while the control panel is placed outside for easy operation and monitoring.
Some advantages of a Split Type Full-Auto CIP Cleaning System include:
Time and cost savings: Automated cleaning reduces the time required for manual cleaning and eliminates the need to disassemble equipment, resulting in significant cost savings.
Consistent cleaning results: The system ensures consistent and thorough cleaning by following pre-programmed cleaning procedures.
Improved safety and hygiene: By eliminating manual cleaning, the risk of accidents and exposure to hazardous chemicals is reduced. It also helps maintain high standards of hygiene by effectively removing contaminants.
Easy maintenance: The split design allows for easy maintenance and repair of the system, minimizing downtime.
Overall, the Split Type Full-Auto CIP Cleaning System is a reliable and efficient solution for maintaining cleanliness and hygiene in industrial equipment and processes.
The main equipment of the system includes:
CIP cleaning liquid storage tanks(include acid tank,alkali tank,hot water tank,clear water tank);
Two single layer tanks for concentrated acid and alkali;
CIP forward and return pumps;
Two diaphragm pumps for acid/alkali concentrate;
Heat exchanger(plate or tubular type);
One electrical appliance box;
One set of controlling pipe and valve component;
One set of auto-performance components and parts and the electrical appliance;
CIP cleaning liquid storage tank:1000L-10000L;
According to the customer's requirments,we can make the double circuit,three circuit,four circuit and so on,meanwhile we can make multi circuit operating at the same time.
The heating way:plate type,coil tube type,tubular type.
CIP Tank size |
1000L-10000L |
|
CIP tank type |
Alcali tank、acid tank、hot water、clean water tank、water recycle tank |
|
Cleaning recycles |
Single circuit、double circuits、three circuits、four circuits |
|
Heating method |
Coil pipes inside、plate heat exchanger 、tubular heat exchanger |
|
Automatic types and charastics |
1、Auto-flow control for the cleaning solution. 6、System auto alarm-device. |
Features and benefits
Your beyond in place cleaning solution is full of all the features and functions required by world-class CIP machines. These abilities enable you to produce food quickly, accurately and safely again and again.
Efficient – simplify and reduce manual cleaning tasks, which means less time and personnel are required for equipment maintenance
Abundant resources - the effective use and reuse of water, clean chemicals and boiler condensate is equivalent to reducing pollution and dependence on water / energy, using limited facility space more wisely, and production costs
Hygiene - a repeatable cleaning process improves operational hygiene and cleaning efficiency
Streamlined – no need for recirculation tank and collection system, saving space and money
Results - strengthening plant hygiene can improve product quality, recovery and purity
Reliable – safer and more consistent factory hygiene methods
Technology - the most advanced PLC, self-service or manual process control system provides operational flexibility and control
ability
Convenience - a one-stop service to meet the needs of all CIP equipment
Thorough - unique low pressure foam enables detergent and disinfectant to penetrate and clean equipment carefully.
Automatic - fully automatic processes (except cleaning steps) reduce labor demand
Customizable – professionally customized system to meet your exact specifications
Design - based on current international and industry standards
Efficient – shorter cleaning cycles mean longer uptime
Milder - continuous CIP can reduce mechanical damage to equipment
More common manual cleaning of equipment – minimize worker and safety
Support – a global team dedicated to providing world-class customer support
Extensive sanitary and industrial CIP systems, tanks and installations reduce cleaning time and costs while providing maximum flexibility
The characteristics of fully automatic large-scale CIP systems in terms of energy conservation and environmental protection are mainly reflected in the following aspects:
1. Energy efficiency optimized pumping system: using frequency conversion technology for efficient pumping, adjusting the pumping rate according to actual needs, and reducing unnecessary energy consumption.
2. Heat recovery and reuse: The system design may include a heat exchanger that can recover the heat from high-temperature wastewater during the cleaning and disinfection stages, preheat the cleaning solution, or use it in other production processes to reduce energy consumption.
3. Intelligent cleaning program: Automatically adjust the concentration, flow rate, and cleaning time of cleaning agents based on the degree of equipment contamination, avoiding excessive use of resources while ensuring cleaning effectiveness.
4. Water saving strategy: Adopting a circulating water system and precise metering spray technology to reduce water consumption during the cleaning process. Advanced CIP systems can also recycle and process some cleaning water for reuse.
5. Application of environmentally friendly cleaning agents: tend to use biodegradable and low toxicity environmentally friendly cleaning agents to reduce the burden on the environment.
6. Remote monitoring and efficiency management: The remote monitoring system can adjust operating parameters in real time to avoid ineffective operation, while data analysis helps identify and improve energy intensive processes.
These measures not only reduce resource consumption and lower operating costs, but also align with the concept of sustainable development and are an important trend in modern industrial production.
In conclusion, you will appreciate our innovative automatic local cleaning equipment because it:
Reduce cleaning time, labor and costs
The automatic disinfection process with more reproducibility than manual cleaning is realized
The combination of automatic and manual cleaning cycles provides you with better and safer cleaning
Reduce mechanical damage to equipment
Support more consistent product quality
Help you achieve more environmentally friendly and sustainable operations
Reduce production costs by reusing and recycling water, cleaning chemicals and boiler condensate
It can be applied to single tank and multi tank systems with or without common base
PLC, self-service or manual control system is allowed
Customizing a fully automated large-scale CIP system is a process that involves in-depth understanding of customer needs and designing adaptive solutions. The main steps include:
1. Requirement analysis: Firstly, we will discuss with you in detail your production line layout, equipment materials, cleaning frequency, special hygiene requirements, etc., to determine the most suitable system configuration.
2. Scheme design: Based on the results of the requirements analysis, our engineering team will design a personalized CIP system scheme, covering equipment selection, pipeline layout, control system design, etc.
3. Energy saving assessment: During the design phase, we will pay special attention to the energy efficiency ratio of the system, evaluate and recommend the most energy-efficient cleaning processes and equipment configurations.
4. Material and component selection: Select high-quality, corrosion-resistant materials to ensure long-term stable operation of the system and compliance with food safety standards.
5. Manufacturing and assembly: After obtaining your approval, the manufacturing and assembly of the system will begin, during which you can keep track of the progress or provide modification suggestions at any time.
6. On site installation and debugging: After the system is completed, our professional team will be responsible for on-site installation and debugging work to ensure smooth operation of the system and seamless integration with the existing production line.
7. Training and after-sales support: Provide operator training to ensure that your team is proficient in using the system. At the same time, we provide long-term after-sales technical support and maintenance services.
The installation and commissioning of a fully automated large-scale CIP system is a professional and meticulous task, typically involving the following key steps:
1. Preliminary preparation: Before installation, ensure that the on-site conditions meet the system installation requirements, including water and electricity supply, drainage facilities, and necessary safety protection measures. At the same time, all system components should be present and undergo quality inspection.
2. Infrastructure construction: Construct or renovate necessary infrastructure according to the design plan, such as equipment bases, pipeline supports, etc., to ensure the stable operation of the support system.
3. Pipeline layout and connection: According to the design drawings, lay and connect the pipelines of the cleaning circuit, including inlet pipes, return pipes, discharge pipes, etc., and install various valves, filters, and monitoring instruments.
4. Equipment installation: Place and secure the main equipment such as cleaning pump, heater, heat exchanger, liquid storage tank, control system, etc., ensuring that all connections are sealed and leak free.
5. Electrical and automation system wiring: Complete the electrical connections between the control system and various equipment, including PLC, sensors, actuators, HMI and other components, and perform preliminary system programming and settings.
6. System testing: Before officially connecting to the production line, separate functional tests should be conducted, such as pump performance testing, electrical control system testing, sensor response testing, etc., to ensure the normal operation of each part.
7. Cleaning cycle verification: Conduct preliminary cycle testing using clean water or simulated cleaning solution to check for leaks, blockages, or insufficient pressure in the system, and adjust and optimize the cleaning program.
8. Docking with the production line: After verifying that all system functions are correct, connect it with the actual production line to ensure interface compatibility and smooth process.
9. Comprehensive debugging and optimization: Conduct comprehensive joint debugging, including simulating the cleaning process under actual production conditions, adjusting parameters based on test results, and achieving the best cleaning effect.
10. Training and Acceptance: Provide system operation and maintenance training for operators to ensure they are proficient in operating. Finally, organize project acceptance, including performance testing, security checks, and document delivery.
11. After sales service launch: After installation and debugging are completed, the after-sales service system will be officially launched to provide users with continuous technical support and maintenance plans.