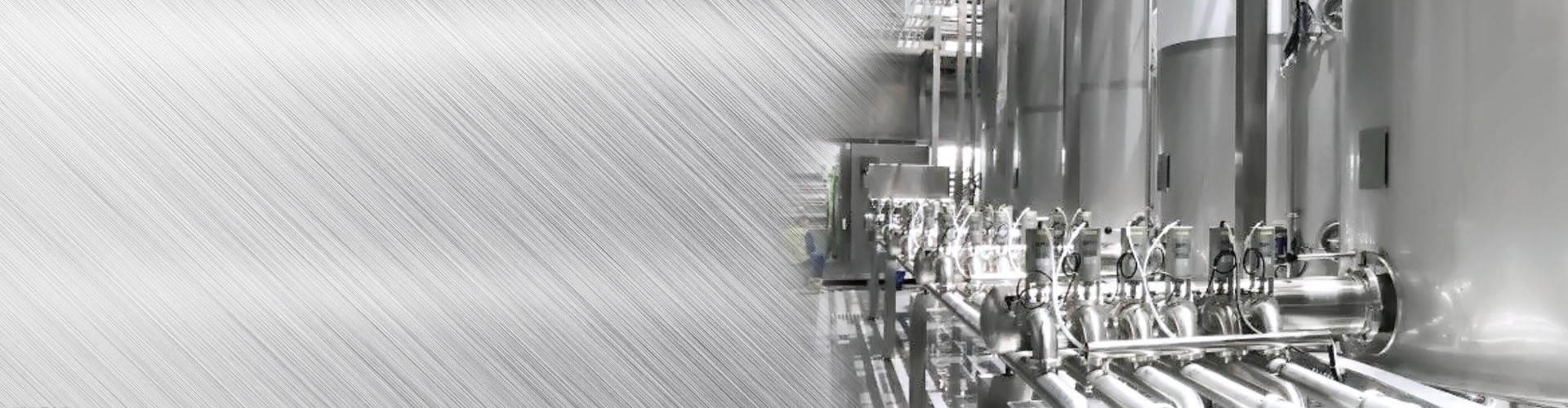
A cream separator is a mechanical device specifically designed to separate cream and whey from milk. In traditional farm operations and modern dairy industry, this type of machine is widely used in the milk processing process. The working principle mainly utilizes the effect of centrifugal force. When milk passes through a rapidly rotating rotor, heavier whey will be thrown towards the container wall and discharged along a specific channel, while lighter cream will gather near the center of the rotor due to the smaller centrifugal force, achieving effective separation of cream and whey. The cream separator not only improves work efficiency, but also ensures the quality and purity of cream products. In addition, different models and specifications of cream separators are suitable for production needs of different scales, from small manually operated family style cream separators to large-scale industrial fully automatic cream separation equipment.
Efficient centrifugal separation technology:
By utilizing the powerful centrifugal force generated by high-speed rotation, the cream (also known as cream or milk fat) in milk can be effectively separated from skim milk in a short period of time, improving production efficiency.
The electric cream separator FJ600EAR is equipped with a high-quality brushless motor and speed regulator, which can adjust the separation speed according to actual needs, adapt to different raw material characteristics and process requirements. At the same time, the motor with a frequency converter can extend the working life of the equipment.
Cold milk separation technology allows for separation at lower temperatures, helping to preserve the nutritional value of milk and cream, reducing flavor loss and nutritional damage caused by high-temperature treatment.
Some cream separators can be integrated into milk pasteurization machines to achieve multiple processes such as cream separation, fat standardization, and pasteurization within a single system.
The airtight cream separator can achieve more flexible production, producing cream products with different fat contents while maintaining high degreasing efficiency, and has the characteristic of no overflow risk, ensuring the safety and hygiene of the production environment.
The equipment comes with a large capacity milk container, such as 50 liters, which can be poured into milk for separation without the need for an additional milk pump; Some high-end models also have fully automatic functions, including automatic slag removal and intelligent control systems.
The use of materials such as stainless steel and anodized aluminum oxide to manufacture the drum and other key components ensures the corrosion resistance and long-term service life of the equipment.
Some cream separators are designed to support switching between multiple formulas and production capacity tasks, allowing one machine to meet the production needs of different products.
Installation and commissioning of cream separator.
The installation and debugging of a cream separator is a relatively professional process that requires following certain steps. The following is the basic process for installing and debugging a cream separator in general. The specific operation should refer to the detailed instructions provided by the equipment manufacturer or be carried out by professional technicians:
Preparation before installation
Ensure that the installation site is flat, dry, well ventilated, and meets hygiene standards for easy cleaning and maintenance.
The ground should have sufficient load-bearing capacity to support the weight of the machine and the vibration during full load operation.
Power supply:
According to the power requirements of the equipment, pre configure appropriate power cables and switches to ensure voltage stability and reliable grounding.
Connect the cooling water system (such as chiller) to ensure that the water pressure, flow rate, and quality meet the equipment requirements.
Equipment unboxing inspection:
Verify the equipment model and accessory list to confirm that there are no damaged or missing components Check if there are any scratches, dents, or other visual defects on the surface of the equipment.
Main body positioning and fixation:
Place the cream separator in the designated position and use a spirit level to calibrate the equipment level Use anchor bolts or fixing brackets to firmly secure the equipment to the ground.
Connect the power cord, control cable, and grounding wire correctly according to the electrical drawings or instructions.
• Cooling system connection (if necessary): • Install cooling water pipes, connect to the designated interface of the equipment, and ensure that the seal is leak free. • Pre test run inspection: • Check if all fasteners are securely tightened, and if moving components such as drums and valves operate smoothly without any jamming. • Check if the electrical control system is functioning properly, and if all indicator lights and instrument displays are functioning properly.
Empty load test run: • Start the equipment and conduct a short period of empty load run. Observe whether the sound, vibration, temperature, and other conditions of the equipment are normal, and there is no abnormal noise or severe vibration Check whether the electrical control system operates stably, and whether all sensors and alarm devices respond sensitively.
Load test run: After the no-load operation is normal, inject an appropriate amount of clean water for a simulated separation test, observe the separation effect, and adjust relevant parameters (such as speed, feed speed, etc.) to the optimal working state After the successful water test, a milk separation test will be conducted to ensure that the quality and efficiency of cream separation meet the requirements.
Cleaning and disinfection: After completing the debugging, carry out the first comprehensive cleaning and disinfection according to the equipment cleaning and disinfection procedures, and prepare for formal production Operation training: Provide training to operators on equipment operation, maintenance, troubleshooting, and other aspects to ensure that they are familiar with equipment performance and operating procedures.
Matters needing attention
During the entire installation and debugging process, the safety operation guidelines and relevant regulations provided by the equipment manufacturer should be strictly followed.
In case of equipment malfunction or unclear situation, timely contact the equipment supplier or professional technical personnel for handling, and do not disassemble or forcibly operate without authorization.The above is the installation and debugging process for a general cream separator. The specific steps may vary due to factors such as equipment model and manufacturer regulations. It is necessary to refer to the installation manual provided with the equipment or be guided by professional technical personnel.
Shanghai Beyond Machinery Co., Ltd
Beyond Machinery specializes in the design and manufacturing of cream separator machine. Please contact us now, and our professional technical engineers will customize the equipment plan for cream separator machine and provide a quotation. Please contact us now to obtain the latest equipment plan and quotation.